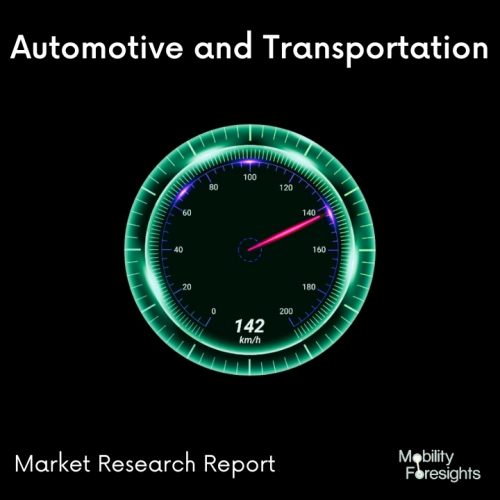
- Get in Touch with Us
Last Updated: Apr 25, 2025 | Study Period: 2024-2030
Electric vehicles (EVs) and hybrid electric vehicles (HEVs) use electronic components called EV power chokes, often referred to as electric vehicle power chokes or EV chokes.
They are a component of the power electronics systems in charge of controlling the flow of electricity inside the car. The primary purpose of EV power chokes is to control the current flowing through the car's electrical circuits.
By minimizing fluctuations and guaranteeing stable and effective performance of the electrical components, they aid in controlling the flow of electricity.
In order for a circuit to function well, a variety of electrical components must be used in its design. Understanding these parts is crucial due to the integration of electronic circuits in next-generation cars.
Toroids are the best forms for magnetic designs because they have the shortest magnetic path and the smallest core volume, but up until now, automating their mass manufacture has been highly difficult and expensive.
The Global EV Power Chokes Market accounted for $XX Billion in 2022 and is anticipated to reach $XX Billion by 2030, registering a CAGR of XX% from 2024 to 2030.
4CMCN065R0-16H and 4CMCN065R0-32H: High-frequency noise in power lines can be effectively filtered using the 4CMCN065R0-16H and 4CMCN065R0-32H chokes' design, which also lessens electromagnetic interference. They are best suited for usage in electric vehicles, which must maximize space and efficiency.
Both the 4CMCN065R0-16H and 4CMCN065R0-32H chokes are capable of managing currents, respectively, making them both incredibly versatile and suitable for usage in a range of electric car charging applications.
They are an important addition to the product lineup of any producer of electric vehicles because of their small size, great efficiency, and adaptable design with the option for customization. With thermal interface materials like CoolMag, the designs are created for maximum thermal coupling of the copper and core.
For the production of these common mode chokes, PREMO has created a fully automated process that includes fully automatic winding. Premo Robotics collaborative robots are being used to totally automate the existing production, which is being done in plants in Vietnam.
Sl no | Topic |
1 | Market Segmentation |
2 | Scope of the report |
3 | Abbreviations |
4 | Research Methodology |
5 | Executive Summary |
6 | Introduction |
7 | Insights from Industry stakeholders |
8 | Cost breakdown of Product by sub-components and average profit margin |
9 | Disruptive innovation in the Industry |
10 | Technology trends in the Industry |
11 | Consumer trends in the industry |
12 | Recent Production Milestones |
13 | Component Manufacturing in US, EU and China |
14 | COVID-19 impact on overall market |
15 | COVID-19 impact on Production of components |
16 | COVID-19 impact on Point of sale |
17 | Market Segmentation, Dynamics and Forecast by Geography, 2024-2030 |
18 | Market Segmentation, Dynamics and Forecast by Product Type, 2024-2030 |
19 | Market Segmentation, Dynamics and Forecast by Application, 2024-2030 |
20 | Market Segmentation, Dynamics and Forecast by End use, 2024-2030 |
21 | Product installation rate by OEM, 2023 |
22 | Incline/Decline in Average B-2-B selling price in past 5 years |
23 | Competition from substitute products |
24 | Gross margin and average profitability of suppliers |
25 | New product development in past 12 months |
26 | M&A in past 12 months |
27 | Growth strategy of leading players |
28 | Market share of vendors, 2023 |
29 | Company Profiles |
30 | Unmet needs and opportunity for new suppliers |
31 | Conclusion |
32 | Appendix |