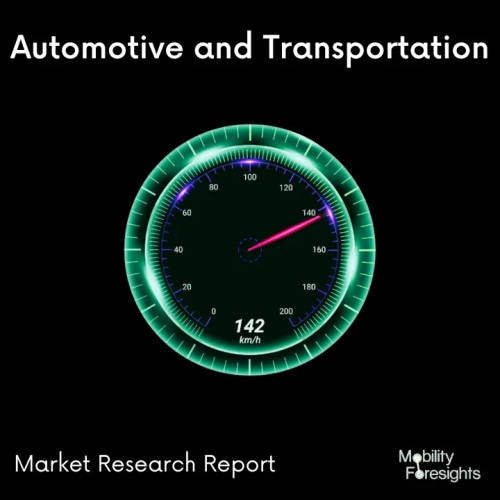
- Get in Touch with Us
Last Updated: Apr 25, 2025 | Study Period: 2024-2030
The market is primarily driven by the increasing adoption of electric vehicles worldwide. As governments implement stringent emissions regulations and consumers become more environmentally conscious, there has been a significant shift towards electric mobility. Structural adhesives offer lightweight, durable, and efficient bonding solutions that contribute to the overall performance and safety of EVs.
EV structural adhesives are used in various applications within electric vehicles. They are commonly employed in bonding battery cells and modules, providing structural integrity to the battery pack. Additionally, these adhesives are used in body assembly to join lightweight materials such as aluminum and carbon fiber composites. They also play a crucial role in sealing and insulation, preventing water ingress and enhancing thermal management within the vehicle.
Manufacturers in the EV structural adhesives market are continuously innovating to meet the evolving needs of EV manufacturers. This includes the development of adhesives with enhanced thermal conductivity for efficient heat dissipation in battery packs. Additionally, advancements in adhesive formulations result in improved adhesion strength, durability, and resistance to temperature extremes.
One notable trend in the global EV structural adhesives market is the increasing focus on sustainability and eco-friendliness. Manufacturers are developing adhesives with reduced VOC emissions and environmentally friendly formulations to align with sustainability goals. Moreover, there is a growing demand for adhesives that enable multi-material bonding, allowing for the joining of dissimilar substrates commonly found in EVs.
The market's growth is not uniform across regions. While developed regions such as North America and Europe lead in terms of technological advancements and adoption of electric vehicles, emerging markets in Asia-Pacific, particularly China and India, are experiencing rapid growth. This growth is driven by government initiatives, investments in infrastructure, and the expansion of the automotive industry.
Global EV structural adhesives refer to specialized adhesive products designed and utilized in electric vehicles (EVs) for bonding and joining various structural components. These adhesives play a critical role in providing strength, durability, and integrity to the structural framework of EVs, including components such as battery packs, chassis, body panels, and interior structures.
They are formulated to meet the specific requirements of EV manufacturing, including lightweight properties, thermal management capabilities, and compatibility with diverse materials used in EV construction. Global EV structural adhesives are essential for ensuring the safety, performance, and longevity of electric vehicles in the rapidly evolving automotive industry.
Epoxy adhesives are versatile and widely used in EV manufacturing due to their excellent bonding strength, chemical resistance, and durability. They are suitable for bonding various substrates, including metals, composites, and plastics. Epoxy adhesives cure through a chemical reaction between the resin and hardener, forming a rigid and strong bond.
Polyurethane adhesives offer flexibility, impact resistance, and good adhesion to a wide range of materials. They are commonly used in EVs for applications that require vibration damping and stress distribution, such as bonding battery modules and sealing joints. Polyurethane adhesives can also provide thermal management properties when formulated with additives for heat dissipation.
Acrylic adhesives offer fast curing times and good adhesion to a wide range of substrates, including metals, plastics, and composites. They provide flexibility and durability, making them suitable for bonding dissimilar materials in EV assemblies. Acrylic adhesives are often used in applications requiring rapid assembly or where vibration resistance is essential.
Thermally conductive adhesives are formulated with additives to enhance heat transfer properties, making them suitable for applications requiring thermal management, such as bonding battery cells and modules in EVs. These adhesives help dissipate heat effectively, reducing the risk of overheating and extending the lifespan of EV components.
The Global EV Structural Adhesive Market accounted for $XX Billion in 2023 and is anticipated to reach $XX Billion by 2030, registering a CAGR of XX% from 2024 to 2030.
Increased Demand for Lightweight Solutions:
As industries seek to reduce vehicle weight for improved fuel efficiency and performance, there is a growing demand for lightweight structural adhesives. Manufacturers are developing advanced adhesive formulations that offer high strength-to-weight ratios, enabling the use of lighter materials in automotive, aerospace, and other applications.
Rise in Sustainable and Eco-Friendly Adhesives:
With increasing focus on sustainability, there is a growing demand for structural adhesives made from renewable and eco-friendly materials. Manufacturers are developing bio-based adhesives derived from sources such as plant-based polymers, recycled materials, and biodegradable compounds. These adhesives offer environmental benefits and help reduce carbon footprint.
Technological Advancements:
Continuous innovation in adhesive technology is driving the development of high-performance structural adhesives with enhanced properties. This includes adhesives with improved bonding strength, durability, temperature resistance, and curing times. Advanced formulations enable bonding of diverse materials and substrates, including metals, plastics, composites, and ceramics.
Adoption of Smart Adhesives:
Smart adhesives embedded with sensors or functional additives are gaining traction in various industries. These adhesives offer additional functionalities such as temperature monitoring, structural health monitoring, and corrosion protection. Smart adhesives enable real-time monitoring and diagnostics, enhancing product performance and reliability.
Expansion of End-Use Industries:
The increasing adoption of structural adhesives across diverse end-use industries such as automotive, aerospace, construction, electronics, and healthcare is driving market growth. Structural adhesives are used in applications ranging from vehicle assembly and aircraft manufacturing to structural bonding in buildings and medical device assembly.
Shift towards Hybrid Adhesives:
Hybrid adhesives combining the properties of multiple adhesive chemistries, such as epoxy, polyurethane, and silicone, are gaining popularity. These versatile adhesives offer a balance of strength, flexibility, and durability, making them suitable for a wide range of applications. Hybrid adhesives enable manufacturers to address specific performance requirements and application challenges effectively.
May 2023,Henkel has extended its electric vehicle (EV) battery systems portfolio with a âfirst-of-its-kindâ injectable thermally conductive adhesive. The new adhesive, branded Loctite TLB 9300 APSi, provides the battery systemâs structural bonding and thermal conductivity. Due to its precise application, enhanced design flexibility and improved bond strength, the injectable thermally conductive adhesive offers the benefits of a simplified manufacturing process.
Loctite TLB 9300 APSi is a two-component polyurethane thermally conductive adhesive with a high thermal conductivity of 3 W/mK, moderate viscosity and self-leveling characteristics. It is designed for bonding battery cells to modules or bonding cells directly to cooling systems.
In February 2020, Huntsman Corporation developed a fast-curing polyurethane resin, VITROX RTM 00410. The product could be used in structural adhesives and sealants for the automotive industry.