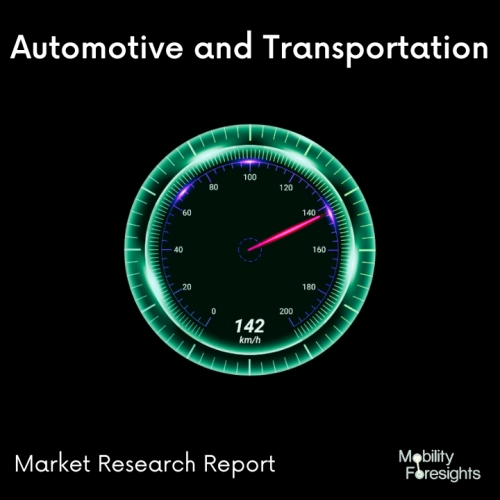
- Get in Touch with Us
Last Updated: Apr 25, 2025 | Study Period: 2023-2030
Although the phrases "potting" and "encapsulation" are frequently used interchangeably, potting really describes a technique in which the resin-filled shell or "pot" becomes a part of the final component.
The component and solidified resin are then taken out of the pot during encapsulation and put in an assembly. Thermal Potting Material To stop electrical components, motors, and appliances from overheating, a protective barrier made of a high thermal conductivity potting compound is placed around them.
The most popular potting compounds are made of silicone, acrylic, epoxy resin, polyurethane, and the latter three. These materials, which range in hardness from extremely soft to hard and unyielding, are made to resist a wide range of environmental conditions.
In the field of electronics, potting is the process of covering an entire electronic assembly with a solid or gelatinous substance to protect it against gaseous phenomena like corona discharge, shock, and vibration, as well as water, moisture, and corrosive substances.
The best material for electronic assembly is the electrical potting compound, which offers sturdy, adaptable, and mechanical protection for sensitive parts and cabling. Electronic assemblies must be potted using high-quality materials that can survive difficult circumstances.
The global EV thermal potting and gel encapsulation market accounted for $XX Billion in 2022 and is anticipated to reach $XX Billion by 2030, registering a CAGR of XX% from 2023 to 2030.
To succeed in the cutthroat market of today, producers must have reliable products. It becomes more difficult to guarantee that electrical circuits operate as intended for a long time when customers seek ever-increasing levels of performance at reduced unit prices.
Due to severe heat build-up and electrical interference, fragile components, densely populated printed circuit boards (PCBs), constrictive packaging, and extremely demanding service environments have the potential to result in elevated failure rates. The highest level of protection from environmental, thermal, chemical, mechanical, and electrical environments is provided by potting and encapsulating materials.
These specifically created compounds, which are intended to entirely encapsulate a component, module, or PCB, successfully screen the unit from its surroundings while offering structural support. Contrary to conformal coatings, potting compounds provide a higher level of physical, chemical, electrical, and temperature protection. On the other hand, potting frequently results in increased processing time, expense, and weight.
Prioritising the needs and understanding that there are trade offs when selecting a material are important steps in selecting the ideal product. It is necessary to strike a balance between handling and processing issues such as open time, viscosity, cure schedule, and other parameters, as well as the final qualities.
Because of their extensive variety of qualities and unrivalled adaptability, epoxies are the most often used material for potting and encapsulating. Epoxies have outstanding physical qualities, great adhesion to metals, most polymers, ceramics, and composites, which are materials frequently used for potting housings, and exceptional chemical resistance.
Sl no | Topic |
1 | Market Segmentation |
2 | Scope of the report |
3 | Abbreviations |
4 | Research Methodology |
5 | Executive Summary |
6 | Introduction |
7 | Insights from Industry stakeholders |
8 | Cost breakdown of Product by sub-components and average profit margin |
9 | Disruptive innovation in the Industry |
10 | Technology trends in the Industry |
11 | Consumer trends in the industry |
12 | Recent Production Milestones |
13 | Component Manufacturing in US, EU and China |
14 | COVID-19 impact on overall market |
15 | COVID-19 impact on Production of components |
16 | COVID-19 impact on Point of sale |
17 | Market Segmentation, Dynamics and Forecast by Geography, 2023-2030 |
18 | Market Segmentation, Dynamics and Forecast by Product Type, 2023-2030 |
19 | Market Segmentation, Dynamics and Forecast by Application, 2023-2030 |
20 | Market Segmentation, Dynamics and Forecast by End use, 2023-2030 |
21 | Product installation rate by OEM, 2023 |
22 | Incline/Decline in Average B-2-B selling price in past 5 years |
23 | Competition from substitute products |
24 | Gross margin and average profitability of suppliers |
25 | New product development in past 12 months |
26 | M&A in past 12 months |
27 | Growth strategy of leading players |
28 | Market share of vendors, 2023 |
29 | Company Profiles |
30 | Unmet needs and opportunity for new suppliers |
31 | Conclusion |
32 | Appendix |