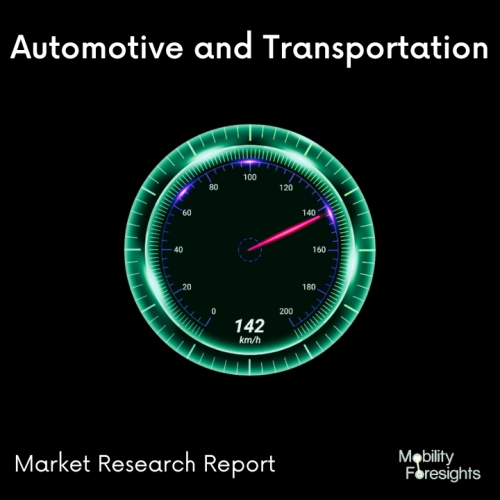
- Get in Touch with Us
Last Updated: Apr 25, 2025 | Study Period: 2024-2030
EV Thermoplastic Vulcanizates, also known as TPVs, are generally made of polypropylene and EPDM rubber and belong to the family of polymers known as thermoplastic elastomers.Vulcanization of the EPDM rubber inside the polypropylene matrix results in good compression set resistance.
The automobile sector uses TPV primarily in products like air bag covers for CVJ boots. And because of its tendency to melt, it is also used in building and construction for things like weather strips and glazing seals.
Over the past few years, the automotive business has become increasingly interested in thermoplastic vulcanizates. Panel hole plugs, gaskets, vibration dampeners, air inlet duct covers, headlamp seals, and weather stripping seals are frequently made of TPV.
To put it simply, TPV has become more popular for automotive applications because of what the substance offers:
Excellent performance over the long term makes it a strong option for achieving vehicle durability standards. Weight-reduction - Engineers may create smaller profiles out of this material, which makes it even lighter and helps to further reduce weight.
Flexible design. Recyclability - This reduces waste and saves money. Processing simplicity - This leads to higher production rates and, in many circumstances, lower piece prices.
The Global EV thermoplastic vulcanizate market accounted for $XX Billion in 2023 and is anticipated to reach $XX Billion by 2030, registering a CAGR of XX% from 2024 to 2030.
An alloy of fully vulcanised EPDM rubber dispersed in a PP phase makes up Santoprene TPV thermoplastic rubber. It is available in natural and black colours and can be supplied from Shore A 35 to Shore D 50.
There are grades that are UV- and Copper-stabilised, flame-retardant, and low-fogging for car interiors. Santoprene TPV is used in 2-component injection moulding, industrial & consumer applications, and a number of automotive approvals.
This type combines the advantages of vulcanised rubber with the processing simplicity of thermoplastics, and it also provides lower system costs, potential sustainability at a distinctive constant level, and global availability.
A buffer pad that contains and or is otherwise made of thermoplastic vulcanizates is offered here TPV. For instance, in electric automobiles, this buffer pad is particularly located between battery cells or modules.
TPV-based buffer pads have a number of benefits over conventional buffer pads, including balanced stiffness and compression, improved sealing, increased flexibility, and ease of manufacture. The battery pack is provided with a high-quality and economical solution by the TPV-based buffer pad.
Sl no | Topic |
1 | Market Segmentation |
2 | Scope of the report |
3 | Abbreviations |
4 | Research Methodology |
5 | Executive Summary |
6 | Introduction |
7 | Insights from Industry stakeholders |
8 | Cost breakdown of Product by sub-components and average profit margin |
9 | Disruptive innovation in the Industry |
10 | Technology trends in the Industry |
11 | Consumer trends in the industry |
12 | Recent Production Milestones |
13 | Component Manufacturing in US, EU and China |
14 | COVID-19 impact on overall market |
15 | COVID-19 impact on Production of components |
16 | COVID-19 impact on Point of sale |
17 | Market Segmentation, Dynamics and Forecast by Geography, 2023-2030 |
18 | Market Segmentation, Dynamics and Forecast by Product Type, 2023-2030 |
19 | Market Segmentation, Dynamics and Forecast by Application, 2023-2030 |
20 | Market Segmentation, Dynamics and Forecast by End use, 2023-2030 |
21 | Product installation rate by OEM, 2023 |
22 | Incline/Decline in Average B-2-B selling price in past 5 years |
23 | Competition from substitute products |
24 | Gross margin and average profitability of suppliers |
25 | New product development in past 12 months |
26 | M&A in past 12 months |
27 | Growth strategy of leading players |
28 | Market share of vendors, 2023 |
29 | Company Profiles |
30 | Unmet needs and opportunity for new suppliers |
31 | Conclusion |
32 | Appendix |