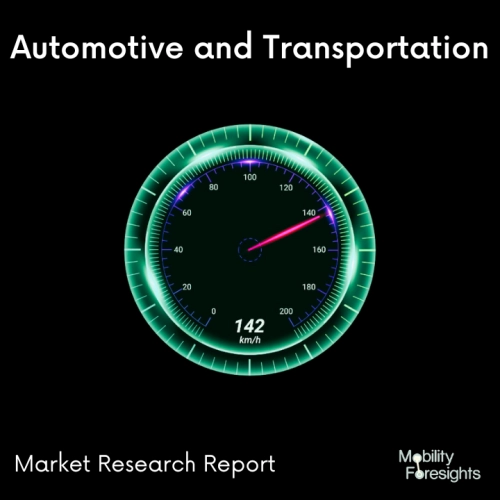
- Get in Touch with Us
Last Updated: Apr 25, 2025 | Study Period: 2023-2030
Any plastic polymer substance that becomes malleable or moldable at a specific elevated temperature and solidifies upon cooling is referred to as thermoplastic or thermoset plastic.
The majority of thermoplastics have large molecules. The intermolecular forces that hold the polymer chains together diminish quickly with rising temperature, resulting in a viscous liquid.
Thermoplastics may be reshaped in this state and are frequently utilized to make parts using a variety of polymer processing processes, including extrusion, calendering, injection molding, and compression molding.
Thermoplastics are distinct from thermosetting polymers (sometimes known as "thermosets"), which during the curing process create irreversible chemical connections.
Thermosets often break down and do not reform after cooling, yet they do not melt when heated.
All-electric vehicles (commonly referred to as EVs or BEVs) donât use gasoline and instead have a large battery that powers one or more electric motors.
Currently, all-electric vehicles have a driving range of 80 to more than 300 miles, with ranges increasing as new models are introduced.
In addition to driving past the gas station, all-electric vehicles donât require much maintenance (such as oil changes, smog checks, spark plug changes, and replacing a catalytic converter or various other parts that wear out and break down) compared to gas cars.
The Global EV thermoplastics market accounted for $XX Billion in 2022 and is anticipated to reach $XX Billion by 2030, registering a CAGR of XX% from 2023 to 2030.
Saudi Basic Industries Corporation (SABIC) continues to create EV thermoplastics-based solutions as automakers quicken their transition to all-electric vehicles, utilizing experience and knowledge to assist the automotive sector in maximizing the performance of electric vehicles (EV).
The most notable of these is that SABIC's automotive business unit has adopted a system engineering approach to develop an electric vehicle (EV) battery pack concept based on lightweight plastics to explore the value of such materials and to address the automotive industry's needs for flexible design, performance enhancement, the need to strengthen safety, and increased economic effectiveness.
SABIC uses a lightweight thermoplastic battery pack concept as opposed to conventional battery pack designs that use traditional materials like aluminum and other metals.
This concept could potentially reduce the weight of each component by 30% to 50%, increase energy density, and simplify the assembly process. It could also lower costs, improve thermal control and safety, and increase crash resistance.
Sl no | Topic |
1 | Market Segmentation |
2 | Scope of the report |
3 | Abbreviations |
4 | Research Methodology |
5 | Executive Summary |
6 | Introduction |
7 | Insights from Industry stakeholders |
8 | Cost breakdown of Product by sub-components and average profit margin |
9 | Disruptive innovation in the Industry |
10 | Technology trends in the Industry |
11 | Consumer trends in the industry |
12 | Recent Production Milestones |
13 | Component Manufacturing in US, EU and China |
14 | COVID-19 impact on overall market |
15 | COVID-19 impact on Production of components |
16 | COVID-19 impact on Point of sale |
17 | Market Segmentation, Dynamics and Forecast by Geography, 2023-2030 |
18 | Market Segmentation, Dynamics and Forecast by Product Type, 2023-2030 |
19 | Market Segmentation, Dynamics and Forecast by Application, 2023-2030 |
20 | Market Segmentation, Dynamics and Forecast by End use, 2023-2030 |
21 | Product installation rate by OEM, 2023 |
22 | Incline/Decline in Average B-2-B selling price in past 5 years |
23 | Competition from substitute products |
24 | Gross margin and average profitability of suppliers |
25 | New product development in past 12 months |
26 | M&A in past 12 months |
27 | Growth strategy of leading players |
28 | Market share of vendors, 2023 |
29 | Company Profiles |
30 | Unmet needs and opportunity for new suppliers |
31 | Conclusion |
32 | Appendix |