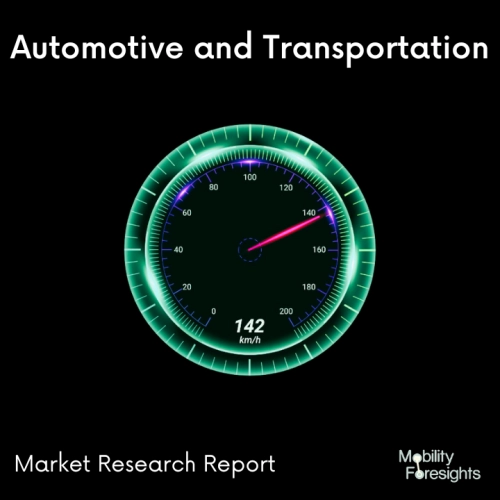
- Get in Touch with Us
Last Updated: Apr 25, 2025 | Study Period: 2023-2030
Thermoplastic Polyolefins (TPO) compounds are resin blends of polypropylene (PP) and un-crosslinked EPDM rubber and polyethylene. They are characterised by high impact resistance, low density and good chemical resistance.
They are used in automotive dashboards and bumpers, among other places, where they must be more durable and tough than standard PP copolymers. The elastomeric properties are limited and the properties are restricted to the upper end of the hardness scale.
By injection, extrusion, or blow molding, TPOs can be easily processed. Polypropylene-based thermoplastic polyolefins (TPOs) have been modified to be more ductile and resistant to impacts than standard PP grades available on the market.
TPOs maintain PP's chemical resistance, lightweight nature, and ease of processing.PVC is more expensive per square foot of material than TPO. TPO, on the other hand, requires about the same amount of labor to install as the other material, if not slightly more.
While the cost of TPOs are often slightly higher than traditional PP compounds, TPOs are still a very cost effective choice for applications requiring good impact resistance and stiffness when other Polyethylene (PE) or PP materials do not meet the application demands.
TPO compounds can be formulated for increased UV weathering and scratch/mar resistance when needed. The UV grades of RTP Companyâs TPO compounds were designed to be compatible with common paint systems to provide an all-in-one solution for situations where some parts are painted and some are not.
The Global EV TPO Compound market accounted for $XX Billion in 2022 and is anticipated to reach $XX Billion by 2030, registering a CAGR of XX% from 2023 to 2030.
Aurora Guard - Through its Aurora Guard product line, Aurora Plastics provides both halogenated and non-halogenated TPO-based materials.
In the wire and cable industry, Aurora Guard TPOs are primarily utilized as polyethylene-based flame retardants; polypropylene with flame retardancy for the battery industry (UL 94 V0 and V2); and paintable applications for the interior, exterior, and automotive market.
To meet material and design engineers' requirements, various fillers and additives are also included. For instance, all AuroraGuard TPOs can be color-matched using UV additives to pass the OEM's accelerated weathering and outdoor weathering tests for two years.
High-melt flow compounds for thin wall and complex injection molding applications are the focus of recent TPO development efforts. We are able to maintain the required physical properties of low weight, low CLTE, stiffness, and impact balance while simultaneously achieving a high melt flow rate.
Sl no | Topic |
1 | Market Segmentation |
2 | Scope of the report |
3 | Abbreviations |
4 | Research Methodology |
5 | Executive Summary |
6 | Introduction |
7 | Insights from Industry stakeholders |
8 | Cost breakdown of Product by sub-components and average profit margin |
9 | Disruptive innovation in the Industry |
10 | Technology trends in the Industry |
11 | Consumer trends in the industry |
12 | Recent Production Milestones |
13 | Component Manufacturing in US, EU and China |
14 | COVID-19 impact on overall market |
15 | COVID-19 impact on Production of components |
16 | COVID-19 impact on Point of sale |
17 | Market Segmentation, Dynamics and Forecast by Geography, 2023-2030 |
18 | Market Segmentation, Dynamics and Forecast by Product Type, 2023-2030 |
19 | Market Segmentation, Dynamics and Forecast by Application, 2023-2030 |
20 | Market Segmentation, Dynamics and Forecast by End use, 2023-2030 |
21 | Product installation rate by OEM, 2023 |
22 | Incline/Decline in Average B-2-B selling price in past 5 years |
23 | Competition from substitute products |
24 | Gross margin and average profitability of suppliers |
25 | New product development in past 12 months |
26 | M&A in past 12 months |
27 | Growth strategy of leading players |
28 | Market share of vendors, 2023 |
29 | Company Profiles |
30 | Unmet needs and opportunity for new suppliers |
31 | Conclusion |
32 | Appendix |