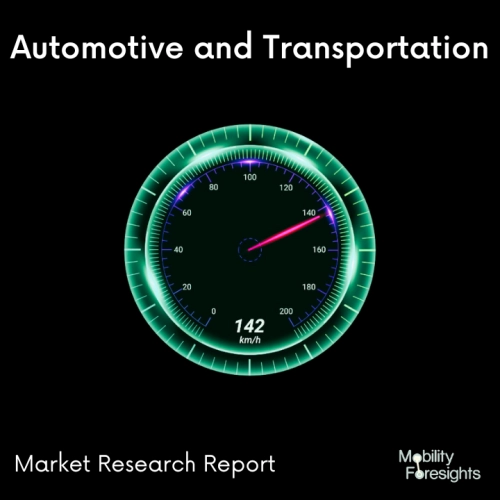
- Get in Touch with Us
Last Updated: Apr 25, 2025 | Study Period: 2024-2030
The majority of high-volume EV applications use silicon steel motor laminations, according to the alloys business. High-induction and low-loss iron-cobalt alloys, on the other hand, come to the fore in EVs with higher performance levels and in heavy-duty commercial vehicles, where the application calls for more torque and power density.
This is important because, according to the supplier of alloys, adopting soft magnetic materials with high induction and low loss properties, such the aforementioned iron cobalt, could be one way to increase these parameters in EV traction motors.
In stamping machines with progressive die sets, for instance, the sheet metal is typically cut and shaped into laminates for traction motors produced in large quantities.
As the material is moved from one stage to the next, a straightforward cutting or bending operation is performed at each stage to create the finished component.
It is anticipated that traction motors will gain from changes in the way backpack is utilized, with a focus on increasing automation to cope with issues emerging from the need to manage loose laminations, for example, better suited it to mass manufacturing.
The Global EV traction motor lamination market accounted for $XX Billion in 2023 and is anticipated to reach $XX Billion by 2030, registering a CAGR of XX% from 2024 to 2030.
By avoiding the usage of pricey rare earth elements, Ricardo is creating a new type of electric vehicle motor that will be far less expensive than current models. The prototype 85kW synchronous reluctance drive was created particularly for EV traction applications.
It is the result of the collaborative research and development initiative known as RapidSR (Rapid Design and Development of a Switched Reluctance Traction Motor). The Ricardo synchronous reluctance electric machine employs low-cost components, straightforward manufacturing techniques, and a traditional dispersed stator winding.
The flux is focused and directed over the air gap by the rotor, which is formed of cut steel laminations. Performance can be improved in a compact, lightweight design without the use of rare earth elements by optimizing this flux coupling between the stator and rotor. It is crucial to look into alternatives to permanent magnet traction motors, which utilize pricey and more and more difficult-to-find rare earth elements, as the market for electric vehicles expands.
This prototype exemplifies what is possible when the most recent methods for designing electric machines are used. In order to eliminate the rare earth elements commonly utilized in permanent magnets, the RapidSR project has been investigating the construction of next-generation affordable electric motors.
The team contends that it has created a framework for the future design and manufacture of EV motors that offer the performance, compact packaging, and light weight necessary for EV applications, but at a lower cost than permanent magnet machines. This framework was developed through the development of effective CAE-led design processes as well as prototype designs.
They have developed a credible, next-generation EV motor concept with a lot of promise by fusing simulation technologies with cutting-edge electric machine design. As a design that offers a balance of performance, compact package, light weight, and low cost, the prototype is now created and will be tested over the coming weeks to validate the positive results that it has demonstrated in simulation.
The traction system motor/generator was developed for integration into a full-sized, high-performance passenger car being built by a significant automotive manufacturer. The performance criteria for traction motors are outlined in the article, which also discusses the electromagnetic, mechanical, and thermal design considerations for the high-speed, 100 kW peak power induction machine.
The designs of the motor controller and traction motor/generator were created to facilitate the development of a full-sized PHEV passenger automobile by a significant international automaker. The manufacturing and assembly methods that were taken into consideration for the prototype machine were limited by the short motor development program timetable.
The traction motor envelope's dimensions and the placement of the mounting tabs and electrical terminals were determined by vehicle integration concerns. The shaft, front flange, and bolt pattern for the completely enclosed, liquid-cooled traction motor were determined by the interaction with the case of the single-speed vehicle gearbox.
Additionally included in the design specification were performance curves and efficiency maps that covered the design speed and power range. In the section on electromagnetic design, more information about the performance requirements is provided.
It summarizes some of the important traction system factors that were taken into account when designing the induction motor/generator. As is the case with many traction motors, the motor performance standards were extremely strict. High volumetric and gravimetric power density was required for the application, and the torque requirements were fairly high, especially at low speeds.
The need for high torque was driven by the need for quick acceleration and hill climbing ability. Table II provides more details on the motor parameters at various speeds and loads. The motor's nominal ratings of 50 kW, 5,000 rpm, and 200 Vac made it possible to develop the baseline design. This translates into a base frequency of 167 Hz for the 4-pole configuration.
Sl no | Topic |
1 | Market Segmentation |
2 | Scope of the report |
3 | Abbreviations |
4 | Research Methodology |
5 | Executive Summary |
6 | Introduction |
7 | Insights from Industry stakeholders |
8 | Cost breakdown of Product by sub-components and average profit margin |
9 | Disruptive innovation in the Industry |
10 | Technology trends in the Industry |
11 | Consumer trends in the industry |
12 | Recent Production Milestones |
13 | Component Manufacturing in US, EU and China |
14 | COVID-19 impact on overall market |
15 | COVID-19 impact on Production of components |
16 | COVID-19 impact on Point of sale |
17 | Market Segmentation, Dynamics and Forecast by Geography, 2024-2030 |
18 | Market Segmentation, Dynamics and Forecast by Product Type, 2024-2030 |
19 | Market Segmentation, Dynamics and Forecast by Application, 2024-2030 |
20 | Market Segmentation, Dynamics and Forecast by End use, 2024-2030 |
21 | Product installation rate by OEM, 2023 |
22 | Incline/Decline in Average B-2-B selling price in past 5 years |
23 | Competition from substitute products |
24 | Gross margin and average profitability of suppliers |
25 | New product development in past 12 months |
26 | M&A in past 12 months |
27 | Growth strategy of leading players |
28 | Market share of vendors, 2023 |
29 | Company Profiles |
30 | Unmet needs and opportunity for new suppliers |
31 | Conclusion |
32 | Appendix |