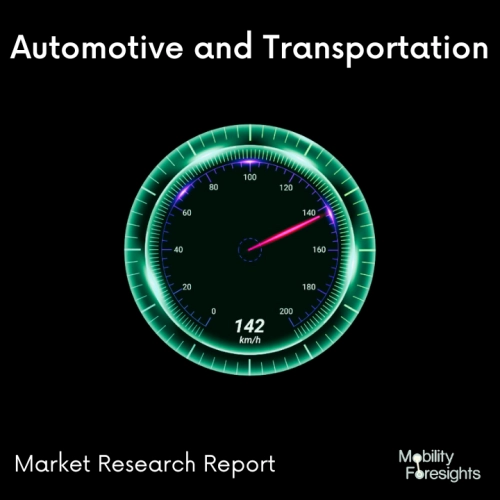
- Get in Touch with Us
Last Updated: Apr 25, 2025 | Study Period: 2024-2030
An electric motor known as a traction motor is one that is created primarily for propulsion in vehicles like trains, electric cars, and hybrid electric cars. It provides the necessary traction to power the vehicle's movement by delivering torque to drive the wheels or axles of the vehicle.
A traction motor is a crucial part of the powertrain of contemporary automobiles since it is often made to work with great efficiency and power density. A rotor (a revolving portion) and a stator (a stationary part) are the two fundamental parts of an electric vehicle (EV) traction motor.
When given an electric current, the stator's windings produce a magnetic field. The vehicle's rotor, which is connected to the drive shaft, has a collection of permanent magnets. The magnetic field produced by the rotating stator interacts with the rotating rotor's magnetic field to cause the rotor to rotate as well.
The torque necessary to move the vehicle is produced by the interaction of the magnetic fields between the rotor and stator. The quantity of electric current fed to the stator windings governs how much torque the motor produces. A motor controller manages the flow of current to the motor to control the electric current.
The motor controller also functions as a converter, converting the battery's DC current into the motor's AC current. For EVs, traction motors deliver great torque during initial movement and low power and efficiency at high speeds.
The Global EV traction motor shaft market accounted for $XX Billion in 2022 and is anticipated to reach $XX Billion by 2030, registering a CAGR of XX% from 2024 to 2030.
The second-generation E-Axle electric vehicle traction motor system from Nidec has begun mass production. Nidec became the first tier-1 business in the world to begin mass manufacturing the E-Axle, an electric vehicle traction motor system that incorporates a motor, a gear, and an inverter ("Gen.1").
Since then, a growing number of our Chinese and international clients have incorporated Gen.1 into their vehicles, with 13 of their models featuring it. Based on magnetic circuit designing, oil cooling, and other technological know-how that they have nurtured through Gen.1's development and mass production.
Gen.2, the E-Axle that the Company started mass-producing at Guangzhou Nidec Auto Drive System Co., Ltd. in China is both lighter and quieter than its predecessor, Gen.1.
E-GMP, the first vehicle architecture specifically designed for electric cars (EVs), has been introduced by the Hyundai Motor Group. Although the E-GMP's standard architecture is rear-wheel drive, adding a traction motor to the front axle is a simple way to add all-wheel drive capability, as is customary for many modern EV platforms.
Hyundai's E-GMP, like the majority of other modern EV platforms, makes use of the typically reduced size of electric motors to develop a platform with a RWD basic configuration. Simple construction for all-wheel-drive applications is made possible by the compact motor size and lack of a standard longitudinal driveshaft. The platform's overall proportions were set up with a long wheelbase and small front and rear overhangs.
The business stated in a press statement that E-GMP will be able to accommodate a wide range of vehicle sizes, and that the flat floor, which is currently typical of most specialized EVs, maximizes passenger capacity and enables a number of possible seating arrangements.
With its rear-wheel driven based E-GMP, Samsung is extending its technological superiority into markets where customers expect superb driving dynamics and exceptional efficiency. Hyundai asserts that the dual-voltage charging technology found in the E-GMP design is a first.
The system is typically designed to operate at 800 volts, which Porsche currently uses and is intended to provide the fastest and most efficient charging possible.The E-GMP charging system can work at 400 volts without the use of any adapters or additional parts, internally scaling up 400-V input to 800 V, as a respect to the probability that 800-V charging infrastructure may take time to develop.
The system also allows for bi-directional energy flow, allowing an E-GMP car to use battery power to feed up to 3.5 kW into a home's electrical system or even charge the battery pack of another EV. A moderately sized household air conditioner plus a television can be run for up to 24 hours on a completely charged battery, according to Hyundai.
Although the bi-directional capability is distinct, it is not a world first because Nissan has long supplied the feature for its iconic Leaf.More specifically, the company claimed that the adaptable charging system can accept enough charge for 26 miles (100 km) of driving in about five minutes, a figure likely chosen for its approximation of the time it takes to refuel an internal-combustion vehicle.
The adaptable charging system can recharge the E-GMP-equipped vehicle's battery pack to 80% in 18 minutes at today's increasingly-available DC fast-charging rates of 350 kW, the company said. Currently, the majority of production EVs have a maximum DC fast-charge capacity of roughly 150 kW.
An emerging technology, a power inverter using silicon-carbide (SiC) semiconductors, is included into the E-GMP architecture. SiC often enables switching frequencies that are substantially more efficient, allowing for the employment of smaller, lighter, and higher-speed traction motors.
Sl no | Topic |
1 | Market Segmentation |
2 | Scope of the report |
3 | Abbreviations |
4 | Research Methodology |
5 | Executive Summary |
6 | Introduction |
7 | Insights from Industry stakeholders |
8 | Cost breakdown of Product by sub-components and average profit margin |
9 | Disruptive innovation in the Industry |
10 | Technology trends in the Industry |
11 | Consumer trends in the industry |
12 | Recent Production Milestones |
13 | Component Manufacturing in US, EU and China |
14 | COVID-19 impact on overall market |
15 | COVID-19 impact on Production of components |
16 | COVID-19 impact on Point of sale |
17 | Market Segmentation, Dynamics and Forecast by Geography, 2024-2030 |
18 | Market Segmentation, Dynamics and Forecast by Product Type, 2024-2030 |
19 | Market Segmentation, Dynamics and Forecast by Application, 2024-2030 |
20 | Market Segmentation, Dynamics and Forecast by End use, 2024-2030 |
21 | Product installation rate by OEM, 2023 |
22 | Incline/Decline in Average B-2-B selling price in past 5 years |
23 | Competition from substitute products |
24 | Gross margin and average profitability of suppliers |
25 | New product development in past 12 months |
26 | M&A in past 12 months |
27 | Growth strategy of leading players |
28 | Market share of vendors, 2023 |
29 | Company Profiles |
30 | Unmet needs and opportunity for new suppliers |
31 | Conclusion |
32 | Appendix |