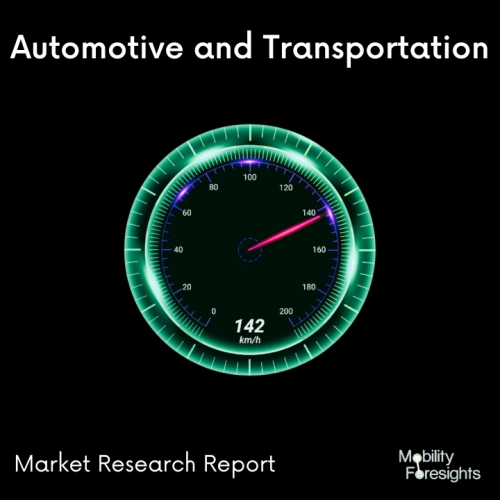
- Get in Touch with Us
Last Updated: Apr 25, 2025 | Study Period: 2024-2030
Because of their low density and exceptional corrosion resistance, titanium and titanium alloys are frequently used in components for aviation, aerospace, marine, chemical industry, biomedical equipment, and other fields.
Examples include aerospace engine parts and marine internal combustion engine parts. However, due to the disadvantages of titanium alloy's high coefficient of friction, poor wear resistance, and low hardness while in use, the bearing members fail before their expected lifespans and the service life is significantly shortened, which significantly restricts the areas in which titanium alloys can be used.
One of the most efficient ways to address the issues of titanium alloy's poor wear resistance and low surface hardness at the moment is the production of a hard coating on its surface.
Traditional hard coatings typically use a single type or scale of ceramic particles for the reinforcing phase.and by increasing the volume percentage of the reinforcing phase, the coating's hardness and wear resistance are enhanced.
The wear resistance and toughness, however, clearly exhibit a "inverse connection," with an increase in hardness and wear resistance typically being accompanied by a large drop in toughness.
Materials scientists from both home and abroad have designed and developed some novel structural wear-resistant coating with high hardness and high toughness, inspired by the unique microstructure of natural high-performance organisms, between the wear resistance and toughness of the hard coating on the surface of titanium alloy.
such multi-scale structure coating, layered structure coating, and gradient structure coating. The gradient design of the microstructure is primarily responsible for the gradient structure coating.
The Global EV Wear-resistant coating market accounted for $XX Billion in 2022 and is anticipated to reach $XX Billion by 2030, registering a CAGR of XX% from 2024 to 2030.
ITW Performance Polymers has introduced ITW Ev Wear Guard 300RTC, its next-generation EV wear resistance coating compound, which is intended to safeguard equipment in high-temperature wet and dry situations.
In high solid, wet settings with temperatures up to 3000F, such as those found in cement plants, power plants, petrochemical facilities, mines, and pulp and paper mills, this improved room temperature cure coating is extremely resistant to chemical attacks.
Customers may achieve exceptional equipment protection with this distinct mix without the challenges of pricey post-baking encountered with competing products.
Customers may do this with simplicity, rapidly continue using the product, and boost equipment uptime. To offer a great customer experience and to provide impressive resistance to wear in both dry and wet corrosive situations, EV Wear Resistant Guard 300RTC has undergone rigorous testing and evaluation.
Field tests have demonstrated the great product durability, allowing customers to run their equipment for longer periods of time between applications or with thinner coats, increasing product output. Customers can reduce equipment failures and maintenance expenses because to this flexibility.
ITW Wear resistance Guard 300RTC, a room temperature cure product, enables the product to be applied onsite, minimising the expensive transportation and remote Post Cure costs necessary with other systems. Removing the need for an oven baked post cure increases equipment uptime while saving time, money, and energy.
Sl no | Topic |
1 | Market Segmentation |
2 | Scope of the report |
3 | Abbreviations |
4 | Research Methodology |
5 | Executive Summary |
6 | Introduction |
7 | Insights from Industry stakeholders |
8 | Cost breakdown of Product by sub-components and average profit margin |
9 | Disruptive innovation in the Industry |
10 | Technology trends in the Industry |
11 | Consumer trends in the industry |
12 | Recent Production Milestones |
13 | Component Manufacturing in US, EU and China |
14 | COVID-19 impact on overall market |
15 | COVID-19 impact on Production of components |
16 | COVID-19 impact on Point of sale |
17 | Market Segmentation, Dynamics and Forecast by Geography, 2023-2030 |
18 | Market Segmentation, Dynamics and Forecast by Product Type, 2023-2030 |
19 | Market Segmentation, Dynamics and Forecast by Application, 2023-2030 |
20 | Market Segmentation, Dynamics and Forecast by End use, 2023-2030 |
21 | Product installation rate by OEM, 2023 |
22 | Incline/Decline in Average B-2-B selling price in past 5 years |
23 | Competition from substitute products |
24 | Gross margin and average profitability of suppliers |
25 | New product development in past 12 months |
26 | M&A in past 12 months |
27 | Growth strategy of leading players |
28 | Market share of vendors, 2023 |
29 | Company Profiles |
30 | Unmet needs and opportunity for new suppliers |
31 | Conclusion |
32 | Appendix |