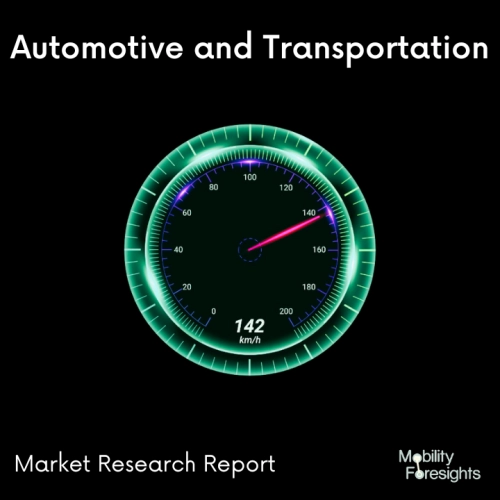
- Get in Touch with Us
Last Updated: Apr 25, 2025 | Study Period: 2024-2030
The amount of kinetic energy that an electron gains as it is propelled in an electric field created by a one-volt potential difference is known as an electron volt.
Wide-bandgap semiconductors, commonly referred to as WBG semiconductors or WBGSs, are types of semiconductors with a wider band gap than traditional semiconductors.
A band gap is the amount of energy needed for electrons and holes to move from the valence band to the conduction band. The band gap of Si (Silicon) is 1.12 electron volts. Wide-band-gap semiconductors are defined as having a big value.
The Global EV Wide band gap semiconductors market accounted for $XX Billion in 2023 and is anticipated to reach $XX Billion by 2030, registering a CAGR of XX% from 2024 to 2030.
Wide Bandgap Technology Enhances Performance of Electric-Drive Vehicles. Silicon-based traction drive inverters for EDV applications need two separate radiators and thermal management systems for the internal combustion engine (ICE) and the electric-drive components.
One barrier to widespread consumer acceptance of hybrid electric and plug-in hybrid electric cars in a competitive market dominated by ICE vehicles is the increased weight, mass, complexity, expense, and lack of efficiency.
WBG-based components, which incorporate silicon carbide-based devices, can decrease the size of power electronics components and perhaps lower system or component costs while enhancing performance and reliability, giving EDVs a competitive edge in the market.
Researchers at NREL are analysing the thermal performance and dependability of these new WBG-based packaging solutions, which may function more effectively and dependably at higher temperatures than the silicon-based components used today.
The world's first commercial high-temperature (140° C ambient), high-power density automobile traction drive inverter was created as a result of continuous research and development at NREL into thermal management solutions for WBG power electronics systems.
On this project, NREL worked in partnership with Toyota, Wolfspeed, the National Centre for Reliable Electric Power Transmission at the University of Arkansas, and the DOE's Vehicle Technologies Office, contributing knowledge for the thermal management, thermomechanical, and reliability aspects of the inverter development.
Industry is currently utilising this R&D 100 Award-winning technology in parts like Wolfspeed's High-Temperature, Wide Bandgap Underhood Inverter for EDVs.
Comparing the WBG inverter to the silicon-based inverter used in the EDVs now on the road, Wolfspeed and NREL's development has shown that the WBG inverter is a more compact, lighter, greater power density, and more effective system.
Sl no | Topic |
1 | Market Segmentation |
2 | Scope of the report |
3 | Abbreviations |
4 | Research Methodology |
5 | Executive Summary |
6 | Introduction |
7 | Insights from Industry stakeholders |
8 | Cost breakdown of Product by sub-components and average profit margin |
9 | Disruptive innovation in the Industry |
10 | Technology trends in the Industry |
11 | Consumer trends in the industry |
12 | Recent Production Milestones |
13 | Component Manufacturing in US, EU and China |
14 | COVID-19 impact on overall market |
15 | COVID-19 impact on Production of components |
16 | COVID-19 impact on Point of sale |
17 | Market Segmentation, Dynamics and Forecast by Geography, 2024-2030 |
18 | Market Segmentation, Dynamics and Forecast by Product Type, 2024-2030 |
19 | Market Segmentation, Dynamics and Forecast by Application, 2024-2030 |
20 | Market Segmentation, Dynamics and Forecast by End use, 2024-2030 |
21 | Product installation rate by OEM, 2023 |
22 | Incline/Decline in Average B-2-B selling price in past 5 years |
23 | Competition from substitute products |
24 | Gross margin and average profitability of suppliers |
25 | New product development in past 12 months |
26 | M&A in past 12 months |
27 | Growth strategy of leading players |
28 | Market share of vendors, 2023 |
29 | Company Profiles |
30 | Unmet needs and opportunity for new suppliers |
31 | Conclusion |
32 | Appendix |