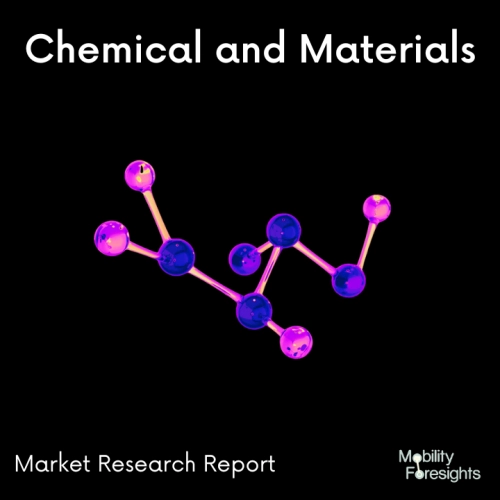
- Get in Touch with Us
Last Updated: Apr 25, 2025 | Study Period: 2024-2030
Extrusion The simplest kind of blow molding is called blow molding. An extruder discharges a hot plastic tube, which is caught in a water-cooled mold.
After the molds are sealed, air is fed into the container through the top or neck, just like one does while blowing up a balloon.
PET is a type of polyester that is typically blow-injected into clear containers. Extrusion blow molding PET is not difficult, but it is less popular because the resin needs a lot of time to dry.
Water and soft drink bottles make up the largest segment of the PET blow molding industry. Reheating a pre-molded PET preform that is then automatically positioned into a mold is how the PET bottle blow molding process operates.
The preform is then injected with high pressure, food-grade compressed air, which causes the preform to expand and take on the form of the mold.
Plastic material feedstock is supplied through a hopper and onto a feeding transfer screw in extrusion blow molding.
This feeds material into a blow molding die that is specially made to guide the flow of the material to produce an extruded hollow tube known as a parison.
The global extrusion blow molding PET resin market accounted for $XX Billion in 2023 and is anticipated to reach $XX Billion by 2030, registering a CAGR of XX% from 2024 to 2030.
Aspira One, a new recyclable PET polymer designed specifically for extrusion blow molding (EBM) processes and packaging applications like clear handleware and large-size bottles, has been added to Eastman Chemical Co.'s line of resins.
In comparison to other polyester resins on the market for the EBM industry, Eastman claims that the new PET polymer offers a "ideal balance of recyclability, product performance, production efficiency, and aesthetics."
Aspira One, a new recyclable PET polymer designed specifically for extrusion blow molding (EBM) processes and packaging applications like clear handleware and large-size bottles, has been added to Eastman Chemical Co.'s line of resins.
In comparison to other polyester resins on the market for the EBM industry, Eastman claims that the new PET polymer offers a "ideal balance of recyclability, product performance, production efficiency, and aesthetics."
They were aware of a product line gap, "According to Eastman's worldwide market development manager for speciality plastic packaging, PlasticsToday.
They had the chance to complete our product line and present extrusion blow molders with a fresh perspective on container resins."
Sl no | Topic |
1 | Market Segmentation |
2 | Scope of the report |
3 | Abbreviations |
4 | Research Methodology |
5 | Executive Summary |
6 | Introduction |
7 | Insights from Industry stakeholders |
8 | Cost breakdown of Product by sub-components and average profit margin |
9 | Disruptive innovation in the Industry |
10 | Technology trends in the Industry |
11 | Consumer trends in the industry |
12 | Recent Production Milestones |
13 | Component Manufacturing in US, EU and China |
14 | COVID-19 impact on overall market |
15 | COVID-19 impact on Production of components |
16 | COVID-19 impact on Point of sale |
17 | Market Segmentation, Dynamics and Forecast by Geography, 2024-2030 |
18 | Market Segmentation, Dynamics and Forecast by Product Type, 2024-2030 |
19 | Market Segmentation, Dynamics and Forecast by Application, 2024-2030 |
20 | Market Segmentation, Dynamics and Forecast by End use, 2024-2030 |
21 | Product installation rate by OEM, 2023 |
22 | Incline/Decline in Average B-2-B selling price in past 5 years |
23 | Competition from substitute products |
24 | Gross margin and average profitability of suppliers |
25 | New product development in past 12 months |
26 | M&A in past 12 months |
27 | Growth strategy of leading players |
28 | Market share of vendors, 2023 |
29 | Company Profiles |
30 | Unmet needs and opportunity for new suppliers |
31 | Conclusion |
32 | Appendix |