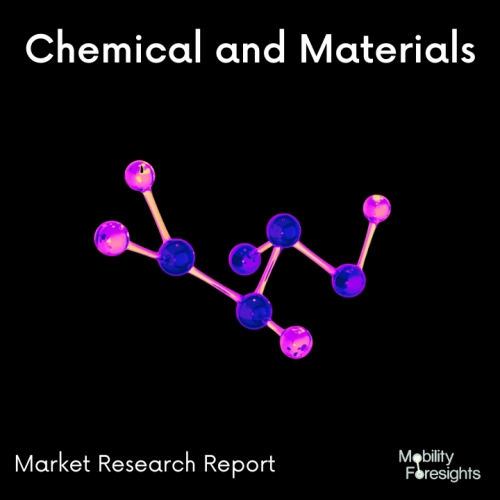
- Get in Touch with Us
Last Updated: Apr 25, 2025 | Study Period: 2024-2030
By forcing material through a die with the desired cross-section, the extrusion process produces objects with set cross-sectional profiles. Its ability to produce extremely intricate cross-sections and its ability to deal with brittle materials because the material only experiences compressive and shear stresses are two of its key benefits over other production procedures.
Additionally, it produces exceptional surface finishes and allows for a great deal of form freedom during the design phase.
A comparable procedure is drawing, which involves pulling the material through the die utilising the material's tensile strength. It can only be used for simpler shapes since it restricts the amount of change that can be made in a single step; numerous steps are typically required. The primary method for producing wire is drawing.
The Global Extrusion Transfer System Market accounted for $XX Billion in 2023 and is anticipated to reach $XX Billion by 2030, registering a CAGR of XX% from 2024 to 2030.
Tecumseh, Michigan The Uniloy UCS.E continuous extrusion shuttle machine has just been introduced, and Uniloy Inc., a leading blow moulding machine and mould technology provider serving the plastics processing industry, is pleased to announce its release.
For more than 50 years, Uniloy has been a market leader in the manufacture of blow moulding equipment and moulds as well as a forerunner in the development of continuous extrusion shuttle machines.
The third version of their all-electric shuttle line is the UCS.E. Since acquiring the venerable brands Comec in 1985 (Italy) and B&W in 1995, Uniloy has consistently been at the forefront of shuttle machine technologies (Germany).
The Uniloy Product Development and Engineering teams created the UCS.E, the most sophisticated Uniloy, using those strong building foundations.
Sl no | Topic |
1 | Market Segmentation |
2 | Scope of the report |
3 | Abbreviations |
4 | Research Methodology |
5 | Executive Summary |
6 | Introduction |
7 | Insights from Industry stakeholders |
8 | Cost breakdown of Product by sub-components and average profit margin |
9 | Disruptive innovation in the Industry |
10 | Technology trends in the Industry |
11 | Consumer trends in the industry |
12 | Recent Production Milestones |
13 | Component Manufacturing in US, EU and China |
14 | COVID-19 impact on overall market |
15 | COVID-19 impact on Production of components |
16 | COVID-19 impact on Point of sale |
17 | Market Segmentation, Dynamics and Forecast by Geography, 2024-2030 |
18 | Market Segmentation, Dynamics and Forecast by Product Type, 2024-2030 |
19 | Market Segmentation, Dynamics and Forecast by Application, 2024-2030 |
20 | Market Segmentation, Dynamics and Forecast by End use, 2024-2030 |
21 | Product installation rate by OEM, 2023 |
22 | Incline/Decline in Average B-2-B selling price in past 5 years |
23 | Competition from substitute products |
24 | Gross margin and average profitability of suppliers |
25 | New product development in past 12 months |
26 | M&A in past 12 months |
27 | Growth strategy of leading players |
28 | Market share of vendors, 2023 |
29 | Company Profiles |
30 | Unmet needs and opportunity for new suppliers |
31 | Conclusion |
32 | Appendix |