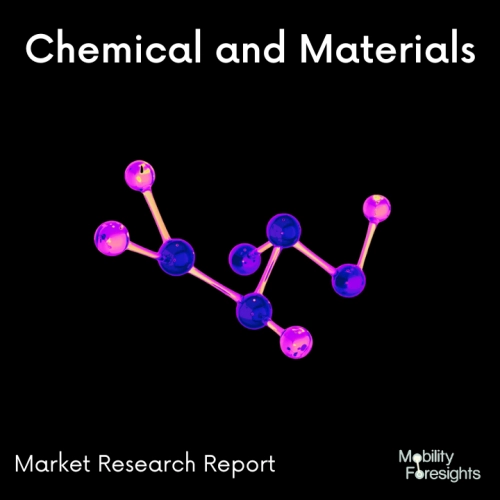
- Get in Touch with Us
Last Updated: Apr 25, 2025 | Study Period: 2024-2030
A falling film evaporator is an industrial device to concentratesolutions, especially with heat sensitive components. Theevaporatoris a special type ofheat exchanger.
In general evaporation takes place inside vertical tubes, but there are also applications where the process fluid evaporates on the outside of horizontal or vertical tubes.
In all cases, the process fluid to be evaporated flows downwards by gravity as a continuous film. The fluid will create a film along the tube walls, progressing downwards (falling) - hence the name.
The fluid distributor has to be designed carefully in order to maintain an even liquid distribution for all tubes along which the solution falls. These distributors are usually called ferrules due to their concentric shape.
In the majority of applications the heating medium is placed on the outside of the tubes. High heat transfer coefficients are required in order to achieve equally balanced heat transfer resistances. Therefore, condensing steam is commonly used as a heating medium.
For internally evaporating fluids, separation between the liquid phase (the solution) and the gaseous phase takes place inside the tubes. In order to maintain conservation of mass as this process proceeds, the downward vapor velocity increases, increasing the shear force acting on the liquid film and therefore also the velocity of the solution.
The result can be a high film velocity of a progressively thinner film resulting in increasingly turbulent flow. The combination of these effects allows very highheat transfer coefficients.
The Global Falling Film Evaporator market accounted for $XX Billion in 2023 and is anticipated to reach $XX Billion by 2030, registering a CAGR of XX% from 2024 to 2030.
APTIA Falling Film evaporator - Falling film evaporators achieve their high thermal performance via the creation and maintenance of a very thin-film of rapidly descending liquid that is laminated to the interior surface of the evaporation tubes.
An evenly distributed liquid film maximizes the contact between the process liquid and the heating media, and allows for the greatest rate of energy transfer from the media to the process fluid
Aptia Engineering optimizes their flow lamination system for each and every FFE that Aptia engineers and manufactures. Aptia recognizes that different applications may have a unique combination of characteristics, such as solids content, extract content, desired (%) reduction in solvent, and vapor velocity.
that need to be accounted for when optimizing the flow lamination system. The result is a compact FFE with superior throughput that is resistant to fouling and provides uniform, controlled evaporation temperatures.
Sl no | Topic |
1 | Market Segmentation |
2 | Scope of the report |
3 | Abbreviations |
4 | Research Methodology |
5 | Executive Summary |
6 | Introduction |
7 | Insights from Industry stakeholders |
8 | Cost breakdown of Product by sub-components and average profit margin |
9 | Disruptive innovation in the Industry |
10 | Technology trends in the Industry |
11 | Consumer trends in the industry |
12 | Recent Production Milestones |
13 | Component Manufacturing in US, EU and China |
14 | COVID-19 impact on overall market |
15 | COVID-19 impact on Production of components |
16 | COVID-19 impact on Point of sale |
17 | Market Segmentation, Dynamics and Forecast by Geography, 2024-2030 |
18 | Market Segmentation, Dynamics and Forecast by Product Type, 2024-2030 |
19 | Market Segmentation, Dynamics and Forecast by Application, 2024-2030 |
20 | Market Segmentation, Dynamics and Forecast by End use, 2024-2030 |
21 | Product installation rate by OEM, 2023 |
22 | Incline/Decline in Average B-2-B selling price in past 5 years |
23 | Competition from substitute products |
24 | Gross margin and average profitability of suppliers |
25 | New product development in past 12 months |
26 | M&A in past 12 months |
27 | Growth strategy of leading players |
28 | Market share of vendors, 2023 |
29 | Company Profiles |
30 | Unmet needs and opportunity for new suppliers |
31 | Conclusion |
32 | Appendix |