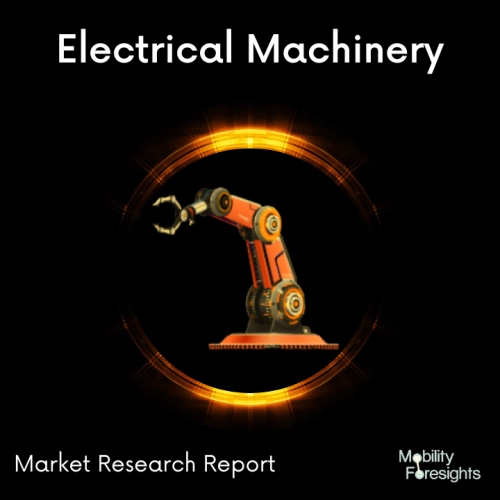
- Get in Touch with Us
Last Updated: Apr 25, 2025 | Study Period: 2023-2030
Thermoforming is the process of stretching a hot plastic sheet over a mold, trimming the design after the sheet has cooled, and then assembling the design to create unique packing solutions.
A massive piece of manufacturing machinery called a thermoforming machine allows you to mold a sheet of plastic onto an object while sucking the air out of the gap. Thermoforming machines are used and benefited by a variety of industries to efficiently package their goods.
A substantial piece of industrial machinery called a thermoforming machine allows you to mold a plastic sheet onto an object while sucking out the air between them. Thermoforming machines are used by several businesses to efficiently package their products, to their advantage.
The Global Fiber Thermoforming machine market accounted for $XX Billion in 2022 and is anticipated to reach $XX Billion by 2030, registering a CAGR of XX% from 2023 to 2030.
Kiefel develops fiber thermoforming machines for cellulose-based packaging.a newly created fiber thermoforming system that, in conjunction with a novel material, opens up a complementary technical field for the company.
Kiefel has also become the first plastic thermoforming machine maker to move into fully automated fiber thermoforming systems with the development of the Natureformer. The new method is known as Kiefel-Fibre-Thermoforming, or KFT for short.
Kiefel used its knowledge in plastics processing to create a new machine that is closely modeled on its iconic KMD steel rule machine while inventing the fiber thermoformer.
Flow simulations are used to ensure a uniform distribution of fibers as the raw paper pulp is treated in batches up to 1% fiber content. The fibers are left in the tool as a filter cake when the suction tool is dipped into the slurry and suctions off. The handling robot, which moves the component from station to station, has the suction tool installed on it.
The component is then sent to the hot press after passing via a flexible counter tool of the pre-pressing station. Temperatures of up to 200°C in the upper and lower tools combined with a clamping force of up to 600 kN eradicate any remaining moisture.
Sl no | Topic |
1 | Market Segmentation |
2 | Scope of the report |
3 | Abbreviations |
4 | Research Methodology |
5 | Executive Summary |
6 | Introduction |
7 | Insights from Industry stakeholders |
8 | Cost breakdown of Product by sub-components and average profit margin |
9 | Disruptive innovation in the Industry |
10 | Technology trends in the Industry |
11 | Consumer trends in the industry |
12 | Recent Production Milestones |
13 | Component Manufacturing in US, EU and China |
14 | COVID-19 impact on overall market |
15 | COVID-19 impact on Production of components |
16 | COVID-19 impact on Point of sale |
17 | Market Segmentation, Dynamics and Forecast by Geography, 2023-2030 |
18 | Market Segmentation, Dynamics and Forecast by Product Type, 2023-2030 |
19 | Market Segmentation, Dynamics and Forecast by Application, 2023-2030 |
20 | Market Segmentation, Dynamics and Forecast by End use, 2023-2030 |
21 | Product installation rate by OEM, 2023 |
22 | Incline/Decline in Average B-2-B selling price in past 5 years |
23 | Competition from substitute products |
24 | Gross margin and average profitability of suppliers |
25 | New product development in past 12 months |
26 | M&A in past 12 months |
27 | Growth strategy of leading players |
28 | Market share of vendors, 2023 |
29 | Company Profiles |
30 | Unmet needs and opportunity for new suppliers |
31 | Conclusion |
32 | Appendix |