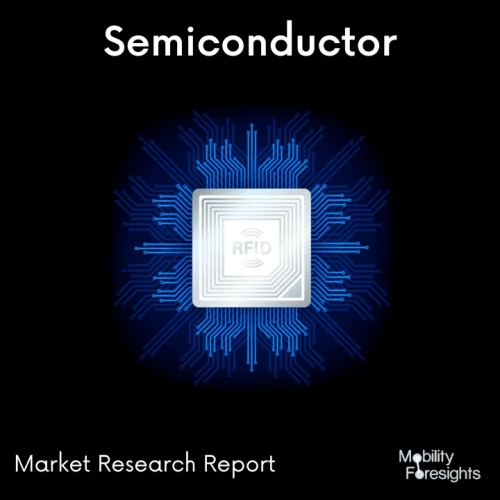
- Get in Touch with Us
Last Updated: Apr 25, 2025 | Study Period:
A graphitic carbon or oleophilic graphite as a thickening is included in a fire-resistant grease along with a fire-resistant base oil. Hydraulic fluids that are fire-resistant, especially phosphorus acid esters or amides and, more specifically, tri hydrocarbyl phosphates, are suitable base oils.
An easy way to get started with fire-resistant greases is to utilise a liquid base oil that is typically used in fire-resistant hydraulic fluids.
Fire-resistant greases are currently being researched for use in lubricating bearings and other moving surfaces in mines, but such greases may be useful in any other environments where fire is a risk. Clearly, these greases cannot be utilised with regular mineral lubricating base oils.
Even though the majority of conventional grease thickeners are fairly fire-resistant, there are still some practical challenges involved in creating fire-resistant greases using a fire-resistant fluid as the base oil, especially when the nature of the thickener calls for relatively high temperatures to produce the grease.
The Global Fire Resistant Greases market accounted for $XX Billion in 2023 and is anticipated to reach $XX Billion by 2030, registering a CAGR of XX% from 2024 to 2030.
The grease that resists firing a Master Roc TSG 800 is the newest model in BASF's line of Master Builders Solutions products for tunnel boring machines. Customers can cut back on consumption thanks to the reduced density product. Furthermore, better packaging makes recycling simpler.
This and other solutions from BASF's portfolio of inventive chemistry will be presented by experts from its Master Builders Solutions division. Their Chemicals and services for effective underground excavation activities make up the bulk of their company. Customers can increase cost effectiveness and safety simultaneously by utilising MasterRoc TSG 800.
A new generation soil conditioning compound called MasterRoc SLF 50 has been specifically created to enhance performance by controlling the soil during tunnelling operations in difficult soil conditions.
This soil conditioner produces a highly stable foam with a great half-life to sustain face pressure throughout operation and scheduled or unforeseen stoppages.
Through torque reduction, it can improve soil extraction, reduce cutterhead wear, and lower power consumption. One of the longest diameter tunnels in the world, being built near Seattle, utilises MasterRoc SLF 50 with success.
Synthetic fire-resistant hydraulic oil has been added to the product lineup by BioBlend Renewable Resources, LLC, a pioneer in environmentally friendly lubricating oils and greases. In order to maintain machinery operating at full efficiency, hydraulic fluids, also known as oils, are used in industries all over the world.
Because they provide dependable, economical performance, hydraulic fluids based on mineral oil are frequently employed. On the other hand, mineral oil, which is made from crude oil, is not fire resistant.
BioBlend is happy to expand its line of industrial hydraulic oils with the addition of BioFlo Synthetic HFDU, a new synthetic fire-resistant product. Offering both biobased and synthetic hydraulic oil options gives consumers a secure, dependable option to satisfy their company's stringent performance criteria.
This product offers a safer alternative to mineral oil and won't compromise performance along with their original BioFlo HFDU product, which is semi-synthetic.
Both goods have earned Factory Mutual approval and are environmentally friendly. The BioFlo HFDU is a fantastic product that performs well in 80% of applications. These goods also have a naturally high viscosity index and are minimally hazardous in addition to the characteristics mentioned above.
Whatever the application, BioBlend has a safe, fire-resistant, high-performing hydraulic fluid that may help lower risk, boost production, and assure a safer environment.
A fire-resistant grease composition made in accordance with the present invention consists of a base oil thickened to a grease consistency by (a) a graphitic carbon with a surface area of at least 170 square metres per gramme as evaluated by nitrogen adsorption.
A heat of adsorption of n-dotriacontane from n-heptane of at least 1 calorie per gramme and a ratio of at least 3.5:1 between the heats of adsorption of n-butanol from n-heptane, or (b) an oleophilic graphite, as defined below, distinguished by the fact that the base oil is a fire-resistant base oil.
Any of the fire-resistant oils that are known to be used as hydraulic fluids may be the fire-resistant base oil. Esters or amides of phosphorus acids, notably phosphate esters and more specifically tri hydrocarbyl phosphates, are the preferred base oils.
The hydrocarbon components of the ester can range in carbon atom count from 3 to 15, and they can be either aryl, alkyl, or a combination of both. Tri(alkylaryl) phosphates might be especially appropriate. Coalite NTP is one brand of such a substance that is available for purchase.
Low toxicity is another advantageous quality of the base oil; the word "NTP'' stands for Non-Toxic Phosphate. Other halogenated hydrocarbons that may withstand fire include chlorinated biphenyls, hexachlorobutadiene, chlorinated paraffins, and chloro-fluoro hydrocarbons.
However, using at least some of these substances may raise environmental concerns. The term "fire-resistant base oil" refers to an oil that passes at least one of the tests listed in NCB Specification 570/1970, ASTM Method D3119-72T, and SAE Specification AMS 3150C as suitable tests for the base oil's fire resistance.
Sl no | Topic |
1 | Market Segmentation |
2 | Scope of the report |
3 | Abbreviations |
4 | Research Methodology |
5 | Executive Summary |
6 | Introduction |
7 | Insights from Industry stakeholders |
8 | Cost breakdown of Product by sub-components and average profit margin |
9 | Disruptive innovation in the Industry |
10 | Technology trends in the Industry |
11 | Consumer trends in the industry |
12 | Recent Production Milestones |
13 | Component Manufacturing in US, EU and China |
14 | COVID-19 impact on overall market |
15 | COVID-19 impact on Production of components |
16 | COVID-19 impact on Point of sale |
17 | Market Segmentation, Dynamics and Forecast by Geography, 2024-2030 |
18 | Market Segmentation, Dynamics and Forecast by Product Type, 2024-2030 |
19 | Market Segmentation, Dynamics and Forecast by Application, 2024-2030 |
20 | Market Segmentation, Dynamics and Forecast by End use, 2024-2030 |
21 | Product installation rate by OEM, 2023 |
22 | Incline/Decline in Average B-2-B selling price in past 5 years |
23 | Competition from substitute products |
24 | Gross margin and average profitability of suppliers |
25 | New product development in past 12 months |
26 | M&A in past 12 months |
27 | Growth strategy of leading players |
28 | Market share of vendors, 2023 |
29 | Company Profiles |
30 | Unmet needs and opportunity for new suppliers |
31 | Conclusion |
32 | Appendix |