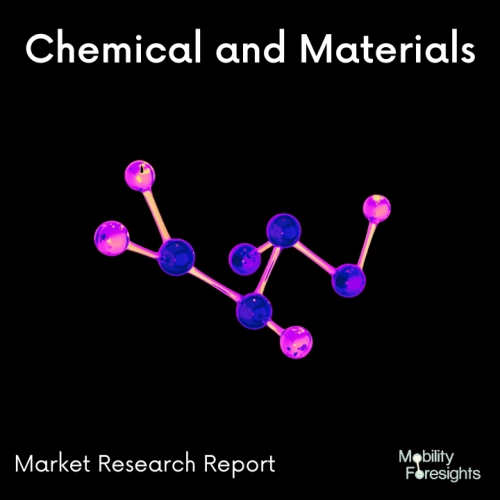
- Get in Touch with Us
Last Updated: Apr 25, 2025 | Study Period: 2024-2030
The best grades of flax are used for linen fabrics such as damasks, lace and sheeting. Coarser grades are used for the manufacture of twine and rope. Flax fibre is also a raw material for the high quality paper industry for use in printed banknotes and rolling paper for cigarettes. flax, (Linum usitatissimum), plant of the family Linaceae, cultivated both for its fibre, from which linen yarn and fabric are made, and for its nutritious seeds, called flaxseed or linseed, from which linseed oil is obtained long as you have Flax in your inventory, you can immediately convert it into Flax Fibres at the Fletching Table.
It's a one to one ratio meaning you'll get 1 Flax Fibre for every 1 Flax used.Flax fibre is extracted from the past or skin of the stem of flax plant. Flax fibres are arranged in the form of thin filaments, grouped in longitudinal slender bundles distributed circularly around a central wooden cylinder. These bundles are fully embedded into an intermediary holding tissue binding them outwardly to the protective outer skin and inwardly to the inner supporting wooden cylinder.
The holding tissue is made up entirely of dynamic cells, having semi-permeable membranes. The wooden cylinder, the fibres and the outer skin, in contrast, are totally made up of fixed static cells, having normal permeable membranes. Flax fibre is soft, lustrous and flexible, stronger than cotton fibre but less elastic.
Global flax fiber market accounted for $XX Billion in 2023 and is anticipated to reach $XX Billion by 2030, registering a CAGR of XX% from 2024 to 2030.
Cobra Advanced Composites launches flax fiber-based visual finish components.In response to strong demand from leading OEM customers, Cobra Advanced Composites (CAC, Chonburi, Thailand), the automotive business of composite products manufacturer Cobra International, has launched a range of production-ready, flax fiber-based, visual finish components.The new natural fiber composite solutions offer a sustainable option compared to traditional carbon look visual components, CAC says.CAC has used flax fiber prepregs with autoclave processing to create the new components.
The low-density flax fibers, typically cultivated in Western Europe, are reported to be much less energy-intensive to produce than carbon fiber, provide good impact resistance and high vibration damping. This makes them suitable for a wide variety of parts including interior and exterior components. Structural flax fibre composites were unveiled by ARRIS Composites. As the team scales Additive Moulding for a production capacity in the millions to fulfil demand, sustainability and new material development are at the centre of everything ARRIS accomplishes.
To supplement its previously existing bio-nylon resin material that is utilised with carbon and glass fibre for goods, the ARRIS R&D team has been working on the development of natural-fibre composites with high-performance characteristics.Since the beginning,their R&D team has been looking into recycled, recovered, and natural fibres as well as recycled, bio-based, and bio-synthesized polymers that assist brands in achieving necessary sustainability initiatives without compromising the best-in-class performance that their customers have come to expect.
They are thrilled to have made this advancement in the handling of flax fibres. Although it has previously been used for decorative components like veneers and panelling, they see a method to utilise these fibres for actual structural purposes. These advanced composites have a significant influence on further lowering CO2 emissions because flax fibre has a CO2e footprint that is just 5% that of carbon fibre.
The first flax-based fabrics were introduced by Saertex. It is the most readily available in terms of quantity and consistency of quality to meet our clients, with a carbon impact at least 50% lower than that of glass reinforcements.
It has acceptable mechanical properties and a density that is nearly two times lower than that of glass fibres. Additionally, it fits both a statutory mandate to reduce emissions and a market demand in the boating sector.
Three productsâone 800 g/m2 quadriaxial and two 400 g/m2 bi-axials âare being marketed by Saertex to kick off this new line. They are great for non-structural components of boats like hoods, seats, bulkheads, doors, or tables. The design process must be modified for the usage of linen in the boating sector. In order to get the most of the natural fibre, builders and architects must reconsider the architecture of buildings. The flax composite is twice as thick as glass for the same weight of impregnated fibres.
It also weighs less for the same thickness and has a nice aesthetic finish. In order to obtain the best mechanical performance and user comfort, flax yarn has been included in the design of SAERTEX reinforcements. Despite being a little slower than for glass, infusion is still achievable with all of the most popular resins, whether they are thermosetting or thermoplastic.
Sl no | Topic |
1 | Market Segmentation |
2 | Scope of the report |
3 | Abbreviations |
4 | Research Methodology |
5 | Executive Summary |
6 | Introduction |
7 | Insights from Industry stakeholders |
8 | Cost breakdown of Product by sub-components and average profit margin |
9 | Disruptive innovation in the Industry |
10 | Technology trends in the Industry |
11 | Consumer trends in the industry |
12 | Recent Production Milestones |
13 | Component Manufacturing in US, EU and China |
14 | COVID-19 impact on overall market |
15 | COVID-19 impact on Production of components |
16 | COVID-19 impact on Point of sale |
17 | Market Segmentation, Dynamics and Forecast by Geography, 2024-2030 |
18 | Market Segmentation, Dynamics and Forecast by Product Type, 2024-2030 |
19 | Market Segmentation, Dynamics and Forecast by Application, 2024-2030 |
20 | Market Segmentation, Dynamics and Forecast by End use, 2024-2030 |
21 | Product installation rate by OEM, 2023 |
22 | Incline/Decline in Average B-2-B selling price in past 5 years |
23 | Competition from substitute products |
24 | Gross margin and average profitability of suppliers |
25 | New product development in past 12 months |
26 | M&A in past 12 months |
27 | Growth strategy of leading players |
28 | Market share of vendors, 2023 |
29 | Company Profiles |
30 | Unmet needs and opportunity for new suppliers |
31 | Conclusion |
32 | Appendix |