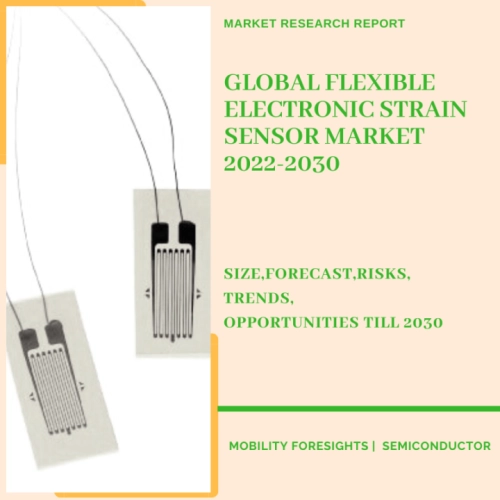
- Get in Touch with Us
Last Updated: Apr 25, 2025 | Study Period: 2022-2030
Mechanical distortions are mostly converted into electrical signals via flexible strain sensors. There are various strain sensor types, including liquid metal, Raman shift, and triboelectric, however these have poor dynamic performance, low resolution, and simple measurement equipment.
As a result, capacitive or resistive strain sensors are more frequently employed as flexible strain sensors. They provide more flexibility, stretchability, and relatively simple readout systems.
There are numerous possible applications for flexible strain sensors, notably in the area of soft electronics. Low-strain gauges, for instance, can be utilised for pressure sensing, mass measurement, and systemic health monitoring. As electronic tools for body integration, very flexible and adaptive strain sensors are another option.
They may be specifically laminated on human skin or affixed to probes that determine body tension from minute skin movements. The heartbeat or breathing mechanism may cause these minute skin movements.
TheGlobal flexible electronic strain sensor marketaccounted for $XX Billion in 2021 and is anticipated to reach $XX Billion by 2030, registering a CAGR of XX% from 2022 to 2030.
Numerous top-notch strain sensors have been created as a result of the wearable technology sector's quick development. Modern strain sensors have satisfied a number of criteria, including mechanical application, quick response times, and high sensitivity.
However, the strain sensors' processing technology, wearing comfort, and safety, which have not received enough attention, have significantly hampered their commercial growth and widespread use.
A high-performance, secure, cosy, waterproof, breathable, affordable, and trustworthy wearable strain sensor is easily and swiftly created using sophisticated electrospinning and screen-printing.
This strain sensor has outstanding repeatability, stability, and sensitivity with a high working strain range (500%) and an extremely quick response time (maximum gauge factor = 520). (100 ms).
Sl no | Topic |
1 | Market Segmentation |
2 | Scope of the report |
3 | Abbreviations |
4 | Research Methodology |
5 | Executive Summary |
6 | Introduction |
7 | Insights from Industry stakeholders |
8 | Cost breakdown of Product by sub-components and average profit margin |
9 | Disruptive innovation in the Industry |
10 | Technology trends in the Industry |
11 | Consumer trends in the industry |
12 | Recent Production Milestones |
13 | Component Manufacturing in US, EU and China |
14 | COVID-19 impact on overall market |
15 | COVID-19 impact on Production of components |
16 | COVID-19 impact on Point of sale |
17 | Market Segmentation, Dynamics and Forecast by Geography, 2022-2030 |
18 | Market Segmentation, Dynamics and Forecast by Product Type, 2022-2030 |
19 | Market Segmentation, Dynamics and Forecast by Application, 2022-2030 |
20 | Market Segmentation, Dynamics and Forecast by End use, 2022-2030 |
21 | Product installation rate by OEM, 2022 |
22 | Incline/Decline in Average B-2-B selling price in past 5 years |
23 | Competition from substitute products |
24 | Gross margin and average profitability of suppliers |
25 | New product development in past 12 months |
26 | M&A in past 12 months |
27 | Growth strategy of leading players |
28 | Market share of vendors, 2022 |
29 | Company Profiles |
30 | Unmet needs and opportunity for new suppliers |
31 | Conclusion |
32 | Appendix |