FLEXOGRAPHIC PRINTING PLATES MARKET
KEY FINDINGS
- Due to its widespread use in packaging applications, the market will witness a growth across different regions with a CAGR of 5-10% from 2024-2030
- Asia will be the largest market for flexographic printing followed by Europe and USA, but the largest growth will be coming in from Africa over the forecast period due to the increase in manufacturing set up in that region
- Flexographic printing plates are used to print on a variety of materials, including plastic, paperboard, and metal, among others. Global demand for packaged food items and growing consumer awareness of product safety are expected to drive market expansion over the coming years.
- Rapid growth in e-commerce, globalization of brands, evolving advertising and labeling needs, and expansion of flexographic printing in corrugated packaging is driving the market
- Increasing people are becoming aware of sustainable options and are using environmental packaging, which has increased demand for flexographic printing plates.
- When the market for eco-friendly packaging increases and becomes more widely accepted, flexographic printing plates will be more in demand.
- The growing popularity of digital flexo plates for shorter runs, personalization, and faster changeovers, and high definition flexo printing and plates raise the bar for image quality and detail, rivaling gravure and offset are also driving the growth in the market
- Due to their rapid printing speeds and ability to use both oil- and water-based inks, flexographic printing machines are popular in the print media, office and administrative use, and industrial applications. One of the growth regulators for the markets for flexographic printing machines is a higher initial setup cost.
- The market for flexographic printing machines appears to be moderately fragmented and competitive. Few of the top players today control a large portion of the market. These major firms, who hold a sizable market share, want to increase their consumer base in other nations.
- The global flexographic printing plates market is poised for continued growth, driven by technological innovation, sustainability trends, and the overall expansion of the packaging industry.
FLEXOGRAPHIC PRINTING PLATES MARKET OVERVIEW
Flexographic printing plates are at the heart of the flexographic printing process, a versatile technique widely used for packaging, labeling, and various other applications. These plates carry the raised image or design that gets inked and transferred onto flexible substrates.
Flexographic Printing Plates Market Dynamics:
- Growing Popularity: The flexographic printing plates market is experiencing steady growth. Key factors propelling this growth include:
- Packaging Boom: The exploding demand for packaging in the food, beverage, pharmaceutical, and e-commerce sectors directly fuels demand for flexographic printing solutions and the associated plates.
- Versatility: Flexo printing's adaptability to printing on various materials (papers, films, foils, etc.) makes it a popular choice, driving the need for plates.
- Efficiency and Cost: Advancements in flexo plates boost efficiency and cost-effectiveness compared to some alternative printing processes.
Types of Flexo Plates
- Analog Plates: Traditional photopolymer plates created through light exposure and development.
- Digital Plates: Increasingly popular, created using laser engraving or thermal imaging for faster turnaround and flexibility.
- Sustainable Options Growing focus on water-washable, solvent-free, and potentially biodegradable plate materials to reduce environmental impact.
Key Applications:
Flexo plates find wide-ranging uses within several industries. Major application areas include:
- Flexible Packaging: Bags, pouches, food wraps, etc.
- Corrugated Products: Shipping boxes, product displays, etc.
- Labels & Tags: Product labels, informational tags across various industries.
- Other: Newspapers, publications, and more.
The flexographic printing plates market promises continued evolution, driven by technological Leaps in which HD Flexo and other innovations are pushing image quality boundaries, potentially increasing flexo's share in high-end printing and emerging markets in which developing regions with rising consumer sectors will present growth opportunities for flexo printing and associated plates.
INTRODUCTION TO FLEXOGRAPHIC PRINTING PLATES MARKET
Flexography is a printing technique that makes use of rotating in-line elements. As a result, flexible materials like paper, plastic, cellophane, and metallic film can be printed on. You can use multiple inks, have varied repetition lengths, and more with flexo printing, as it is also known. Rubber stamp printing, which became popular in the early the origin of flexography.
The FDA changed the inks being used and renamed the process after determining that the inks were dangerous for use in food packaging, which was the technologyâs primary application at the time. A roll-feed web printing technique is flexography. Numerous labels and pieces of packaging are frequently printed in bulk using flexographic printing. Presses may print at speeds of up to feet per minute on a range of films, foils, papers, corrugated boards, and paperboard.
Plastic bags, pouches, packages, gift wrap, tissue, envelopes, wallpaper, ice cream cartons, folding cartons, bottle wraps, adhesive and shrink-sleeve labels, shopping bags, and disposable plates and cups are among the items printed on flexo presses. For each colour, a flexible photopolymer plate is wrapped around a turning cylinder. The images and text for each color are raised from the surface of the plate, just like in letterpress printing. The plate is only inked in the elevated portions.
For flexographic printing, the pre-press procedure is crucial. Due to the fast speed of this process, errors in plate making or artwork preparation might result in significant ink and material waste. Itâs crucial to remember that the plate will probably result in image enlargement since the flexible plate will be stretched when it is fastened to the plate cylinder. Additionally, itâs crucial to confirm that the ink type will be able to print clearly onto the substrate.
FLEXOGRAPHIC PRINTING PLATES MARKET SIZE AND FORECAST
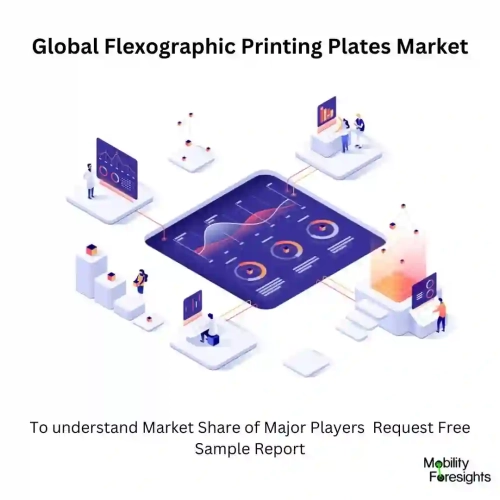
The Global Flexographic Printing plates market accounted for $XX Billion in 2023 and is anticipated to reach $XX Billion by 2030, registering a CAGR of XX% from 2024 to 2030.
FLEXOGRAPHIC PRINTING PLATES MARKET RECENT TECHNOLOGICAL DEVELOPMENTS
- HD Flexo and Full HD Flexo:High Definition (HD) Flexo and Full HD Flexo technologies have revolutionized flexographic printing by significantly enhancing print quality. These advancements in plate imaging and processing allow for sharper images, finer details, smoother gradients, and improved color consistency. HD and Full HD Flexo plates enable flexographic printers to achieve results comparable to offset and gravure printing, making flexography a more competitive option for high-quality packaging applications.
- Digital Flexographic Plate Making:Digital plate making technologies have streamlined the plate production process, reducing turnaround times and increasing efficiency. Computer-to-Plate (CTP) systems eliminate the need for film-based workflows, allowing flexographic printers to directly image printing plates from digital files. This digital workflow improves accuracy, reduces waste, and enables quick adjustments to plate designs, enhancing productivity and flexibility in plate production.
- Flat Top Dot (FTD) Technology:Flat Top Dot (FTD) technology has emerged as a preferred method for achieving consistent ink transfer and excellent print quality in flexographic printing. FTD plates feature a flat, uniform surface on the printing dots, which reduces dot gain, minimizes dot bridging, and enhances color saturation. This technology improves print fidelity and allows for finer line work and text reproduction, making it ideal for high-resolution packaging graphics.
- Thermal and UV-Curable Plate Materials:Advancements in plate material formulations have led to the development of thermal and UV-curable flexographic plates with improved durability, stability, and sustainability. These plates offer faster processing times, better resistance to abrasion and chemicals, and reduced environmental impact compared to traditional solvent-based plates. Thermal and UV-curable plate materials enable higher run lengths, lower plate waste, and enhanced recycling capabilities, aligning with the industry's sustainability goals.
- Sustainable Plate Solutions:With increasing emphasis on sustainability, manufacturers are developing eco-friendly flexographic plate solutions that minimize environmental impact throughout the production process. This includes plates made from renewable or recycled materials, water-based processing systems, and solvent-free plate imaging technologies. Sustainable plate solutions help reduce carbon emissions, conserve resources, and support circular economy initiatives in the packaging industry.
- Advanced Plate Surface Treatments:Surface treatment technologies, such as laser ablation and chemical etching, are being used to enhance the surface properties of flexographic printing plates. These treatments improve ink adhesion, reduce plate swelling, and extend plate life, resulting in better print consistency and longer-lasting plates. Advanced surface treatments also enable finer plate features and more intricate designs, expanding the capabilities of flexographic printing for complex packaging applications.
FLEXOGRAPHIC PRINTING PLATES MARKET RECENT LAUNCHES
- DuPont:DuPont is a leading supplier of flexographic printing plates. They have introduced new plate technologies aimed at enhancing print quality, productivity, and sustainability. Recent launches may include advancements in plate materials, such as water-washable or thermally processed plates, as well as innovations in plate imaging technologies to improve image reproduction and consistency.
- Esko:Esko, a provider of software and hardware solutions for the packaging industry, offers a range of flexographic plate-making systems. Recent launches from Esko may include upgrades to their Digital Flexo Suite software, which optimizes plate production processes, as well as advancements in plate imaging equipment to support high-definition flexographic printing.
- MacDermid Graphics Solutions:MacDermid Graphics Solutions specializes in providing flexographic printing plates and associated equipment. Recent launches from MacDermid may include new plate formulations designed to improve print quality and durability, as well as innovations in plate processing equipment to enhance efficiency and consistency in plate production.
- Kodak:Kodak is known for its flexographic plate technologies, including the KODAK FLEXCEL NX System. Recent launches from Kodak may include updates to their plate imaging and processing systems, introducing features such as higher resolution imaging, faster processing times, and improved sustainability credentials through solvent-free processing options.
- Asahi Photoproducts:Asahi Photoproducts is a manufacturer of flexographic photopolymer plates. Recent launches from Asahi may include advancements in plate materials and construction, such as improved dot reproduction and durability, as well as innovations in plate imaging technologies to achieve finer details and smoother vignettes in printed images.
FLEXOGRAPHIC PRINTING PLATES MARKET COMPETITIVE LANDSCAPE
Company | Strengths | Weaknesses | Opportunities | Threats |
DuPont | Pioneer in flexo technology, vast portfolio, strong R&D | Potential reliance on analog plate technologies | High-growth digital flexo segment, expansion in emerging markets | Competition from plate specialists |
Asahi Kasei | Innovation in water-washable plates, strong brand recognition | Limited presence in some developing markets | Sustainability trend favors water-washable technologies | Price competition in mature markets |
Flint Group | Wide product range, global distribution network | Potential for less focus on niche plate applications | Growth of specialized flexo printing for high-end packaging | Increased market consolidation |
Esko | Integrated workflow solutions, expertise in digital flexo plates | Reliance on partnerships for some plate technologies | Prepress and platemaking automation trend | Intensifying competition from other workflow providers |
FLEXOGRAPHIC PRINTING PLATES MARKET DEVELOPMENTS AND INNOVATIONS
Overview of Development | Development Detailing | Region of Impact | Possible Future Outcomes |
Advancements in Digital Flexo Plates | Faster production of plates using laser engraving or thermal imaging. | Global | Increased flexibility and shorter turnaround times More accessible small-quantity printing jobs Potential decrease in analog plate usage |
HD Flexo | Developments in plates and printing systems for very high-resolution flexo printing | Primarily Developed Markets (Europe, North America) | Flexo competes with offset/gravure in higher-end packaging Potential for expansion with brands demanding quality |
Sustainable Plate Technologies | Focus on water-washable, solvent-free, compostable plate materials | Global (higher initial emphasis in regions with stricter regulations) | Reduced environmental footprint of printing Appeals to sustainability-conscious brands ThisMight drive regulatory changes |
Flat-Top Dot Plates | Specialty plates with flat-top dots for more uniform ink coverage and tonal consistency | Global | Improved print quality and color vibrancy Potential for wider adoption as technology matures |
Automation & Integration | Integration of platemaking with prepress workflows for greater efficiency | Global | Reduced setup times and labor costs in printing Potential for smaller print shops to offer flexo services |
FLEXOGRAPHIC PRINTING PLATES MARKET NEW TRENDS
- High Definition (HD) and Full HD Flexo:The adoption of HD and Full HD Flexo technologies continues to grow in the flexographic printing plates market. These technologies offer improved print quality, allowing for sharper images, finer details, and smoother gradients. As brand owners demand higher quality packaging, HD and Full HD Flexo plates are becoming increasingly popular for achieving premium print results.
- Water-Washable and Solvent-Free Plates:There is a rising trend towards eco-friendly plate solutions in the flexographic printing market. Water-washable plates, which eliminate the need for harsh solvents in the plate processing stage, are gaining traction due to their environmental benefits. Similarly, solvent-free plate options are being developed to reduce the environmental impact of plate production and processing.
- Digital Flexographic Plate Making:The transition towards digital flexographic plate-making systems is accelerating, driven by the need for faster turnaround times and greater production flexibility. Digital plate-making technologies enable direct imaging of plates from digital files, eliminating the need for film-based workflows and reducing setup times. This trend is particularly prominent in short-run and variable data printing applications.
- Advanced Plate Surface Treatments:Surface treatment technologies, such as laser ablation and chemical etching, are being increasingly utilized to enhance the surface properties of flexographic printing plates. These treatments improve ink transfer, reduce dot gain, and enhance overall print consistency. Advanced surface treatments enable finer details and better ink laydown, leading to higher-quality printed materials.
- Sustainable Plate Solutions:Sustainability is a key focus area in the flexographic printing plates market. Plate manufacturers are developing sustainable plate solutions that use renewable materials, reduce waste, and minimize environmental impact. This includes the development of bio-based plate materials, recycling programs for used plates, and the implementation of energy-efficient plate-making processes.
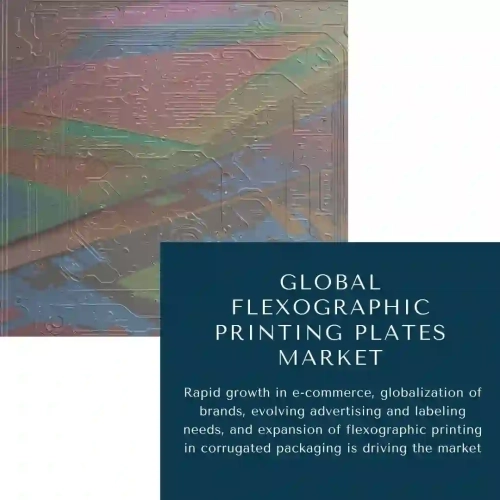
FLEXOGRAPHIC PRINTING PLATES MARKET DYNAMICS
S. No. | Timeline | Company | Developments |
1 | Oct 2022 | Asahi Kasei | Launched new water-washable flexo plate with "Pinning Technology for Clean Transfer" (reduced ink build-up), further refining its sustainable plate offerings. |
2 | July 2022 | DuPont | Expanded its Cyrel FAST plate portfolio with new thermal and solvent-based processing options offering speed and flexibility for printers. |
3 | May 2023 | Esko | Announced partnerships with several plate suppliers to streamline platemaking integration within its prepress workflows, aiming for greater efficiency in flexo production. |
4 | 2022 (ongoing) | Various | Multiple smaller plate manufacturers (often regionally focused) introduce 'direct-to-plate' technologies, increasing competition in the digital flexo arena. |
5 | 2021-2023 | Flint Group | Continued expansion in developing regions (Asia, Latin America), aiming to capture growth in those markets alongside its established global presence. |
FLEXOGRAPHIC PRINTING PLATES MARKET SEGMENTATION
By Plate Material
- Photopolymer Plates
- Rubber Plates
- Others (such as Metal Plates)
By Plate Type
- Digital Flexographic Plates
- Analog Flexographic Plates
By Geography
- USA
- Europe
- China
- Asia Ex China
- ROW
By Application
- Flexible Packaging
- Labels
- Folding Cartons
- Corrugated Boxes
- Others (such as Beverage Cartons, Wallpaper)
FLEXOGRAPHIC PRINTING PLATES MARKET COMPANY PROFILES
- DuPont
- Asahi Kasei
- Flint Group
- Esko
- Kodak
- MacDermid Graphics Solutions
- Toyobo
- 3M
- E.I. du Pont de Nemours and Company
- Dantex Group
FLEXOGRAPHIC PRINTING PLATES MARKET REPORT WILL ANSWER FOLLOWING QUESTIONS
- How many Flexographic Printing Plates are manufactured per annum globally? Who are the sub-component suppliers in different regions?
- Cost breakup of Flexographic Printing plates and key vendor selection criteria
- Where are the Flexographic Printing plates manufactured? What is the average margin per unit?
- Market share of Global Flexographic Printing market manufacturers and their upcoming products
- Cost advantage for OEMs who manufacture Flexographic Printing plates in-house
- 5 key predictions for next 5 years in Flexographic Printing plates market
- Average B-2-B Flexographic Printing market price in all segments
- Latest trends in Flexographic Printing plates market, by every market segment
- The market size (both volume and value) of the Flexographic Printing plates market in 2024-2030 and every year in between?
- Production breakup of the Flexographic Printing plates market, by suppliers and their OEM relationship
- What recent advancements have been made in high-definition (HD) and Full HD Flexo technologies for flexographic printing plates?
- How are digital flexographic plate-making systems evolving to meet the demands for faster turnaround times and greater production flexibility?
- What role do automation and workflow integration play in improving efficiency and productivity in the production of flexographic printing plates?
- Can you explain the technological innovations behind solvent-free flexographic printing plates and their environmental benefits?
- How are manufacturers leveraging sustainable materials and processes to develop eco-friendly flexographic printing plate solutions?
- What are the challenges and opportunities associated with the integration of digital plate-making technologies into traditional flexographic printing workflows?
- How do advancements in plate surface treatments contribute to achieving finer details and better ink laydown in flexographic printing?
- What impact do customized and personalized plate solutions have on the flexibility and agility of flexographic printing operations?
- How are manufacturers addressing the need for higher print quality and consistency through advancements in plate imaging and processing technologies?
- Can you discuss the potential of artificial intelligence (AI) and machine learning in optimizing plate design and production processes in the flexographic printing industry?