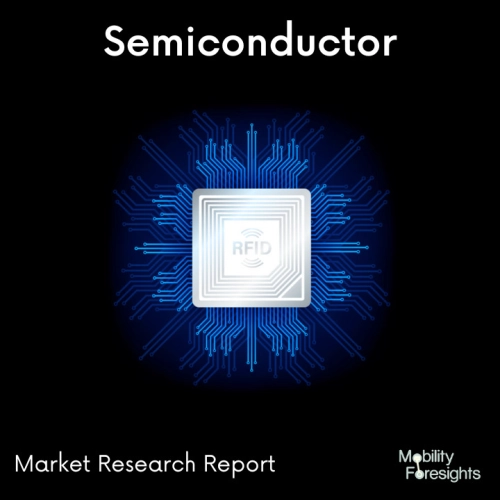
- Get in Touch with Us
Last Updated: Apr 25, 2025 | Study Period:
A technique for connecting dies, such as semiconductor devices, IC chips, integrated passive devices, and microelectromechanical systems, to external circuitry using solder bumps that have been deposited onto the chip pads is known as flip chip, also known as controlled collapse chip connection or by its abbreviation.
The Light Military Electronics Department of General Electric created the method. During the last stage of wafer processing, solder bumps are placed on the chip pads on the top side of the wafer.
The chip is turned over so that its top side is facing down, positioned so that its pads line up with complementary pads on the external circuit, and then the solder is reflowed to complete the interconnect in order to mount it to external circuitry. In contrast, the chip is attached vertically when using wire bonding.
The process of mounting a flip-chip upside-down (flip), face-down on a substrate, printed circuit board, or other carrier is referred to as flip chip microelectronics assembly.
The conductive chip bumps are eutectically linked after being correctly positioned with regard to the bump pad (chip bond pad).
A Flip-Chip Die Bonder from works with a beam splitting camera (Flip-Chip Ultra or Flip Chip Ultra MPA) to ensure the extremely precise alignment of the chip with respect to the substrate, in contrast to wire bonding, a method used to electrically connect chips on the upper side (face-up) with a wire connection.
The Global Flip Chip Bonder market accountedfor $XX Billion in 2023 and is anticipated to reach $XX Billion by 2030, registering a CAGR of XX% from 2024 to 2030.
The tool combines high precision, flexibility, quick cycle time, and innovative design. It is the first in a new line of SET flip-chip bonders that are solely intended for production. It was created in association with CEA-Leti as a component of the 3D integration programme at IRT Nanoelec.
Nicolas Raynaud, project manager at SET, continued, "This extensive, interesting, and rewarding collaboration allowed us to build a bonding solution tailored to fine-pitch assembly needs.
The world's first surface-mount, flip-chip, back-emitting VCSEL array without the requirement for a package submount or bond wires for mobile sensing cameras has been introduced by TriLumina, the industry's leading developer of VCSEL technology for 3D sensing.
In comparison to traditional VCSELs for 3D sensing, this novel VCSEL-on-Board technology allows improved performance, smaller size, lower costs, and streamlines time-of-flight camera supply chains.
With an alignment accuracy of roughly 1um, the Finetech Fineplacer Lambda tool is made for flip-chip bonding of two pieces. The apparatus is a semiautomatic bonder with complete computer control over the bonding parameters and a built-in side-camera system for bonding observation.
It is possible to accommodate sample sizes ranging from 500 um on a side to 50 mm on a side. The pieces can be subjected to forces ranging from 0.3 N to 500 N. Bonding can occur at temperatures as high as 400C.
During heated indium bonding, the system additionally features a formic acid module (reduced atmosphere environment) that is employed to stop oxide formation.
Sl no | Topic |
1 | Market Segmentation |
2 | Scope of the report |
3 | Abbreviations |
4 | Research Methodology |
5 | Executive Summary |
6 | Introduction |
7 | Insights from Industry stakeholders |
8 | Cost breakdown of Product by sub-components and average profit margin |
9 | Disruptive innovation in the Industry |
10 | Technology trends in the Industry |
11 | Consumer trends in the industry |
12 | Recent Production Milestones |
13 | Component Manufacturing in US, EU and China |
14 | COVID-19 impact on overall market |
15 | COVID-19 impact on Production of components |
16 | COVID-19 impact on Point of sale |
17 | Market Segmentation, Dynamics and Forecast by Geography, 2024-2030 |
18 | Market Segmentation, Dynamics and Forecast by Product Type, 2024-2030 |
19 | Market Segmentation, Dynamics and Forecast by Application, 2024-2030 |
20 | Market Segmentation, Dynamics and Forecast by End use, 2024-2030 |
21 | Product installation rate by OEM, 2023 |
22 | Incline/Decline in Average B-2-B selling price in past 5 years |
23 | Competition from substitute products |
24 | Gross margin and average profitability of suppliers |
25 | New product development in past 12 months |
26 | M&A in past 12 months |
27 | Growth strategy of leading players |
28 | Market share of vendors, 2023 |
29 | Company Profiles |
30 | Unmet needs and opportunity for new suppliers |
31 | Conclusion |
32 | Appendix |