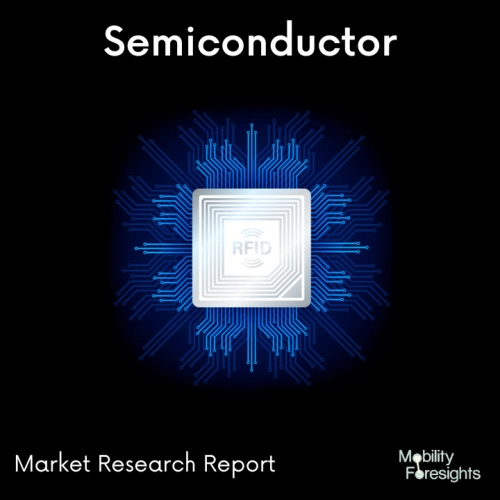
- Get in Touch with Us
Last Updated: Apr 25, 2025 | Study Period:
With a few extra processes, flip chip packaging processing is very similar to traditional IC manufacture. The attachment pads are metalized towards the end of the manufacturing process to make them more solder friendly. This often includes a number of therapies.
Each metalized pad is then covered with a tiny solder dot. The chips are then conventionally sliced from the wafer. The flip chip must be reversed in order to bring the solder dots down onto connectors on the underlying electronics or circuit board in order to be attached to a circuit.
The solder is then frequently remelted using a thermionic bonding or alternatively a reflow solder process to create an electrical connection.
In order to create a heat bridge, strengthen the mechanical connection, and prevent the solder joints from being stressed as a result of differential heating between the chip and the rest of the system, an electrically insulating adhesive is frequently "underfilled" after that.
The underfill spreads out the thermal expansion mismatch between the chip and the board, minimizing stress buildup in the solder junctions that can cause early failure.
Compared to direct chip attach or chip on board, FCCSP offers superior chip protection and solder junction durability. In low-cost test and burn-in, FCCSP outperforms known excellent die and KGD in terms of electrical performance.
The Global Flip chip packaging Market accounted for $XX Billion in 2023 and is anticipated to reach $XX Billion by 2030, registering a CAGR of XX% from 2024 to 2030.
The Mnano II series of small pitch devices from YES TECH caught many attendees' attention when it was launched at ISE in Spain. In terms of applications, full flip-chip COB technology has risen to the top of the heap and is now driving the growth of the display sector.
Cold screen touch, low power dissipation, homogeneous heat dissipation, minimal temperature rise, and long-term consistency in ink colour are advantages. Higher reliability and stability, six protection assurances, and super lamp anti-collision capability.
With improved vision and a better viewing experience, surpass the formal encapsulation chip's pixel pitch restriction.
The screen can also maintain the print colour consistency for a long time, have contrast up to 10,000:1, have a matte fog surface design, be anti-glare, and have a superior viewing experience using a tiny COB flip chip with Nano-optical composite packaging coating.
Sl no | Topic |
1 | Market Segmentation |
2 | Scope of the report |
3 | Abbreviations |
4 | Research Methodology |
5 | Executive Summary |
6 | Introduction |
7 | Insights from Industry stakeholders |
8 | Cost breakdown of Product by sub-components and average profit margin |
9 | Disruptive innovation in the Industry |
10 | Technology trends in the Industry |
11 | Consumer trends in the industry |
12 | Recent Production Milestones |
13 | Component Manufacturing in US, EU and China |
14 | COVID-19 impact on overall market |
15 | COVID-19 impact on Production of components |
16 | COVID-19 impact on Point of sale |
17 | Market Segmentation, Dynamics and Forecast by Geography, 2024-2030 |
18 | Market Segmentation, Dynamics and Forecast by Product Type, 2024-2030 |
19 | Market Segmentation, Dynamics and Forecast by Application, 2024-2030 |
20 | Market Segmentation, Dynamics and Forecast by End use, 2024-2030 |
21 | Product installation rate by OEM, 2023 |
22 | Incline/Decline in Average B-2-B selling price in past 5 years |
23 | Competition from substitute products |
24 | Gross margin and average profitability of suppliers |
25 | New product development in past 12 months |
26 | M&A in past 12 months |
27 | Growth strategy of leading players |
28 | Market share of vendors, 2023 |
29 | Company Profiles |
30 | Unmet needs and opportunity for new suppliers |
31 | Conclusion |
32 | Appendix |