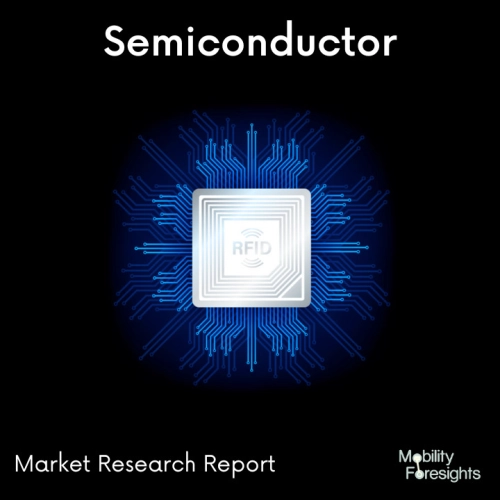
- Get in Touch with Us
Last Updated: Apr 25, 2025 | Study Period: 2024-2030
A Fluidized Bed Reactor (FBR) is a type of reactor used in various chemical processes. FBRs are widely used in chemical and petrochemical industries due to their high efficiency and flexibility. FBRs are designed to contain a bed of solid particles, such as sand, which are suspended in a gas stream. The gas stream is usually air that is heated to a temperature that is just below the boiling point of the particles. This creates a fluidized state where the particles are suspended in the gas stream and can move around freely.
FBRs have many advantages over other types of reactors. They have a much larger surface area for reaction, making them more efficient than other types of reactors. This means that more reactions can occur in a shorter amount of time. FBRs also have a higher degree of temperature control and can operate at temperatures that are too high for other types of reactors. Additionally, FBRs are able to handle higher pressures than other types of reactors, making them suitable for a wide range of reactions.
In addition to their efficiency, FBRs are also relatively low cost and easy to maintain. They can be used in a wide range of processes, from simple reactions to complex catalytic reactions. FBRs can be used in many different industries, from petroleum and petrochemical processing to food and beverage production.
The Global Fluidized Bed Reactor market accounted for $XX Billion in 2023 and is anticipated to reach $XX Billion by 2030, registering a CAGR of XX% from 2024 to 2030.
The first new product launch is the K-Fluidized Bed Reactor (K-FBR). Developed by a Korean company, this reactor is designed to provide an efficient method of producing chemicals and pharmaceuticals. It uses an advanced fluidized bed design that is capable of simultaneously carrying out chemical reactions and separations. The reactor also features a low operating temperature, which helps to reduce energy costs. The K-FBR is an ideal choice for applications that require high product yields and low operating costs.
The second new product launch is the High-Temperature Fluidized Bed Reactor (HTFBR). This reactor is designed to be used in high temperature chemical processes such as cracking, reforming, and hydro-treating. The HTFBR is a compact and efficient reactor that is capable of producing higher yields than other types of reactors. The reactor also features a high degree of automation, which allows for increased safety and control.
The third new product launch is the BioFBR. Developed by a French company, this reactor is designed to be used for biological processes such as fermentation and waste water treatment. The BioFBR is a highly efficient reactor that can carry out multiple processes simultaneously. The reactor also features a low operating temperature and pressure, which helps to reduce energy costs.
The fourth new product launch is the NanoFBR. Developed by a Japanese company, this reactor is designed to be used for nanotechnology applications such as nanofiltration and nanosynthesis. The NanoFBR is a compact and efficient reactor that is capable of carrying out multiple processes simultaneously. The reactor also features a low operating temperature and pressure, which helps to reduce energy costs.
Sl no | Topic |
1 | Market Segmentation |
2 | Scope of the report |
3 | Abbreviations |
4 | Research Methodology |
5 | Executive Summary |
6 | Introduction |
7 | Insights from Industry stakeholders |
8 | Cost breakdown of Product by sub-components and average profit margin |
9 | Disruptive innovation in the Industry |
10 | Technology trends in the Industry |
11 | Consumer trends in the industry |
12 | Recent Production Milestones |
13 | Component Manufacturing in US, EU and China |
14 | COVID-19 impact on overall market |
15 | COVID-19 impact on Production of components |
16 | COVID-19 impact on Point of sale |
17 | Market Segmentation, Dynamics and Forecast by Geography, 2024-2030 |
18 | Market Segmentation, Dynamics and Forecast by Product Type, 2024-2030 |
19 | Market Segmentation, Dynamics and Forecast by Application, 2024-2030 |
20 | Market Segmentation, Dynamics and Forecast by End use, 2024-2030 |
21 | Product installation rate by OEM, 2023 |
22 | Incline/Decline in Average B-2-B selling price in past 5 years |
23 | Competition from substitute products |
24 | Gross margin and average profitability of suppliers |
25 | New product development in past 12 months |
26 | M&A in past 12 months |
27 | Growth strategy of leading players |
28 | Market share of vendors, 2023 |
29 | Company Profiles |
30 | Unmet needs and opportunity for new suppliers |
31 | Conclusion |
32 | Appendix |