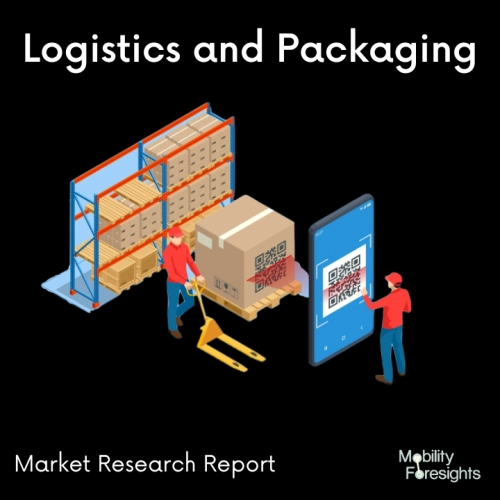
- Get in Touch with Us
Last Updated: Apr 25, 2025 | Study Period: 2022-2030
Foam sheet material is more expensive and more complex to produce than other materials that are used to make foams. Signs, displays, wall cladding, pop-up displays, air conditioning ducts, exhibition boards, models, indoor/outdoor decoration, partitions, windows, false ceilings, control cabinets, and panels are just a few uses for foam in various industries. It is also used to build structures for corrosive environments.
A major element in the market's expansion is the rising need for foam in other sectors like packaging and building & construction.
The key constraints limiting the growth of the foam sheet market, however, include price fluctuations for raw materials such refined petroleum products, inorganic chemicals, and resins, strict government restrictions, and a slowing economy.
The global foam sheets and partitions market accounted for $XX Billion in 2021 and is anticipated to reach $XX Billion by 2030, registering a CAGR of XX% from 2022 to 2030.
A new product category for polyurethane foams sheets and partitions has been officially launched by TECHNONICOL. In order to meet all potential needs of the builders, the selection comprises professional sealing, fire-resistant, and gluing foams in addition to high-performance spray foam insulation.
TECHNONICOL Corporation has been manufacturing polyurethane foams sheet with the greatest raw materials and contemporary technology. To adhere to the strictest environmental safety requirements, the factory was constructed using a closed cycle approach.
The Swiss business Pamasol has created a high-tech automated production line with a total yearly capacity of up to 7,000 tonnes of PU foams sheets.
The company also opened a brand-new R&D facility to create novel compositions and continuously improve the functional aspects of items. Customers and applicators can profit greatly from TECHNONICOL's PU foams. Large primary foam volume, obtained immediately after application, ensures that even wide joints will be filled quickly.
Additionally, the ultimate amount of the cured foam is visible immediately after injection into the joint, obviating the possibility of the structure's subsequent misalignment. Because of the ideal balance between drying time and cured foam density, foam does not flow off vertical surfaces.
All of these ensure the excellent quality of joints, ensuring their sturdiness and longevity. The money is also saved by an increased volume of foam emissions and a negligible amount of cut trash.
Sl no | Topic |
1 | Market Segmentation |
2 | Scope of the report |
3 | Abbreviations |
4 | Research Methodology |
5 | Executive Summary |
6 | Introduction |
7 | Insights from Industry stakeholders |
8 | Cost breakdown of Product by sub-components and average profit margin |
9 | Disruptive innovation in the Industry |
10 | Technology trends in the Industry |
11 | Consumer trends in the industry |
12 | Recent Production Milestones |
13 | Component Manufacturing in US, EU and China |
14 | COVID-19 impact on overall market |
15 | COVID-19 impact on Production of components |
16 | COVID-19 impact on Point of sale |
17 | Market Segmentation, Dynamics and Forecast by Geography, 2022-2030 |
18 | Market Segmentation, Dynamics and Forecast by Product Type, 2022-2030 |
19 | Market Segmentation, Dynamics and Forecast by Application, 2022-2030 |
20 | Market Segmentation, Dynamics and Forecast by End use, 2022-2030 |
21 | Product installation rate by OEM, 2022 |
22 | Incline/Decline in Average B-2-B selling price in past 5 years |
23 | Competition from substitute products |
24 | Gross margin and average profitability of suppliers |
25 | New product development in past 12 months |
26 | M&A in past 12 months |
27 | Growth strategy of leading players |
28 | Market share of vendors, 2022 |
29 | Company Profiles |
30 | Unmet needs and opportunity for new suppliers |
31 | Conclusion |
32 | Appendix |