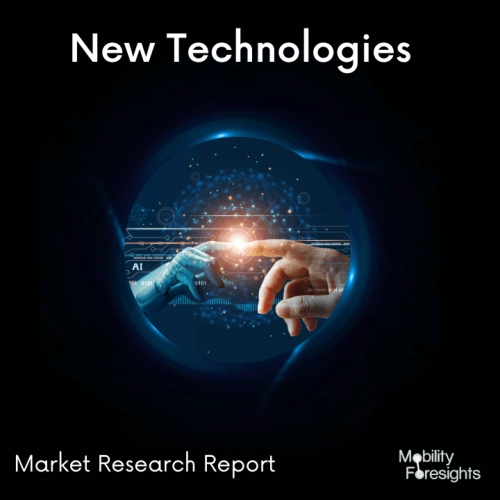
- Get in Touch with Us
Last Updated: Apr 25, 2025 | Study Period:
Most industrial processes today rely on monitoring systems to guarantee product quality and process effectiveness. Choosing the right sensor technology for the application is essential for getting accurate findings. Sensors must be resilient, adaptable, and dependable regardless of the environment in order to meet these requirements.
The capabilities, constraints, and compatibility of the sensor for the planned application must all be carefully taken into account. In order to avoid process malfunction, sensors are essential parts of the monitoring and control system in the food business. Sensors are based on environmental responses that are physical, chemical, or biological.
The Global Food & Beverage Pressure Sensors Market accounted for $XX Billion in 2023 and is anticipated to reach $XX Billion by 2030, registering a CAGR of XX% from 2024 to 2030.
IFM, a sensor maker, has added numerous new instances of British-made food processing technology to its ever-expanding portfolio of smart technology. The Middlesex makers have given the food and beverage sector two new sanitary sensor alternatives for use in abrasive CIP cleaning applications with the inclusion of their OG-Cube photoelectric sensors and PM pressure sensor.
With its lateral M18 thread and connector pointing down and space-saving design, IFM's innovative OG-Cube photoelectric sensor is the ideal choice for all requirements in hygienic and wet situations. This brand-new photoelectric sensor from IFM can survive harsh cleaning agents and high-pressure cleaning thanks to its high-grade stainless steel housing, food-grade sealing material, shatter-proof plastic glass, and high protection rating.
A new series of IP69K-protected laser sensors from precision sensor manufacturer Micro-Epsilon are designed for measuring displacement, distance, and position in harsh manufacturing environments such as food and beverage processing.
The new optoNCDT 1402SC sensor series is protected by an IP69K-rated stainless steel enclosure. The sensor is resistant to aggressive cleaning solutions like hydrogen peroxide and other alkaline- or chlorine-based cleaning agents, as well as high-pressure jet washing and disinfectants.
VEGA is now able to assist customers in even more areas of the food and beverage production processes thanks to the introduction of its new low cost, high specification VEGABAR pressure switch/sensor and VEGAPOINT level switches. The new level and pressure devices have a universal adapter system of process fittings that provide the flexibility needed to keep installation and spares inventory costs low.
Visibility, safety, and process dependability are guaranteed by a special, eye-catching, 360° illuminated status display ring. Its status colours can be easily seen from any angle, even in bright sunlight, and can be customised. Some of the new pressure switch/sensors have displays and keypads with dual easy-read text and VDMA menus, which guarantees accurate setup each time and makes pressure measurement or switch status understandable.
The most demanding applications in the food and beverage industry are addressed by Rockwell Automation's Bulletin 871TS Food and Beverage Inductive Proximity sensors. They can withstand washdown under high pressure and heat while providing superior resistance to corrosion and damage from abrasive cleaning agents.
These sensors have undergone thorough chemical compatibility testing by ECOLAB, and the company has certified that they are compatible with some of the most widely used caustic cleaning and disinfecting solutions.
Sl no | Topic |
1 | Market Segmentation |
2 | Scope of the report |
3 | Abbreviations |
4 | Research Methodology |
5 | Executive Summary |
6 | Introduction |
7 | Insights from Industry stakeholders |
8 | Cost breakdown of Product by sub-components and average profit margin |
9 | Disruptive innovation in the Industry |
10 | Technology trends in the Industry |
11 | Consumer trends in the industry |
12 | Recent Production Milestones |
13 | Component Manufacturing in US, EU and China |
14 | COVID-19 impact on overall market |
15 | COVID-19 impact on Production of components |
16 | COVID-19 impact on Point of sale |
17 | Market Segmentation, Dynamics and Forecast by Geography, 2024-2030 |
18 | Market Segmentation, Dynamics and Forecast by Product Type, 2024-2030 |
19 | Market Segmentation, Dynamics and Forecast by Application, 2024-2030 |
20 | Market Segmentation, Dynamics and Forecast by End use, 2024-2030 |
21 | Product installation rate by OEM, 2023 |
22 | Incline/Decline in Average B-2-B selling price in past 5 years |
23 | Competition from substitute products |
24 | Gross margin and average profitability of suppliers |
25 | New product development in past 12 months |
26 | M&A in past 12 months |
27 | Growth strategy of leading players |
28 | Market share of vendors, 2023 |
29 | Company Profiles |
30 | Unmet needs and opportunity for new suppliers |
31 | Conclusion |
32 | Appendix |