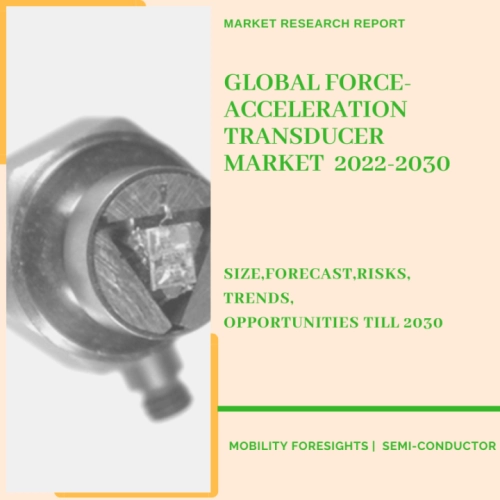
- Get in Touch with Us
Last Updated: Apr 25, 2025 | Study Period: 2022-2030
By definition, a force sensor is a particular kind of transducerâa force transducer. It transforms a mechanical force that is being applied as an input, such as load, weight, tension, compression, or pressure, into another physical variable, in this example, an electrical output signal that can be measured, converted, and standardised.
An increase in force acting on the force sensor causes a proportionate change in the electrical signal.Transducers have become a crucial component in a wide range of industries, including robotics, aerospace & defence, medical & pharmaceuticals, high precision manufacturing, automotive, and industrial automation.
Recent developments in Collaborative Robots (Cobots) and Surgical Robotics have led to the emergence of numerous unique force measurement applications.
One needs to comprehend the underlying physics and material science of the strain gauge, which is the basis for strain gauge force measurement (sometimes referred to as Strain gauge). A sensor called a metal foil strain gauge changes electrical resistance in response to applied force.
To put it another way, it transducesâor convertsâforce, pressure, tension, compression, torque, weight, etc. into a change in electrical resistance that can be measured.
TheGlobal Force-acceleration transducer marketaccounted for $XX Billion in 2021 and is anticipated to reach $XX Billion by 2030, registering a CAGR of XX% from 2022 to 2030.
A combination force-acceleration transducer that enables adjusting for acceleration forces in dynamic measurements on test rigs is the newest patented product from GTM company. However, the force transducer and one or more MEMS acceleration sensors with varying degrees of sensitivity are combined in the unique force-acceleration transducer.
One of the sensors has a high sensitivity in the low frequency and low acceleration band. Another sensor has a range of up to kilohertz and can perform readings at higher acceleration rates. Extending the application's scope is possible with the option of adding additional sensors. Users select and attach the acceleration sensor that best meets their needs for measuring.
The ARJ series acceleration transducer is compact and offers exceptional responsiveness. This series has been developed to gauge the acceleration of various types of machinery, vehicles, ships, buildings, and other civil engineering constructions.
The series also includes the uni-axial model ARJ-A, the bi-axial model ARJ-A-D, which is identical in terms of size and weight to the uni-axial model, and the tri-axial model ARJ-A-T, which is identical in terms of height to the uni- and bi-axial models and weighs twice as much as the bi-axial model. It is made to be compact and light so that installation won't interfere with the measurement object's vibration mode.
Using a Device acceleration sensor, the ARGH-A is a compact and highly responsive acceleration transducer. This transducer can be used for measurement in many different industries, including machinery, vehicles, ships, civil engineering, and construction, thanks to its compact, lightweight, and durable structure.
Without the need for an external power source, this transducer can be utilised by just attaching it to our dynamic strain metre in dc mode. Its output level was determined by an internal amplifier to be the same as a strain gauge-style acceleration transducer.
Compared to strain gauge type acceleration transducers, there is a larger permitted overload. Having an instrument attached to a power source is all that is required to measure something. A mass that is spring-loaded against a crystal is used to build electromechanical accelerometers.
Depending on which way the transducer is accelerated, the force acting on the crystal will change or increase. An electrical charge across the crystal's opposing faces that is proportional to the applied force will be created by the force acting on the crystal. Accelerometers are often the name given to transducers that are used to measure acceleration. The most frequent purpose for them is to gauge an object's vibration.
Sl no | Topic |
1 | Market Segmentation |
2 | Scope of the report |
3 | Abbreviations |
4 | Research Methodology |
5 | Executive Summary |
6 | Introduction |
7 | Insights from Industry stakeholders |
8 | Cost breakdown of Product by sub-components and average profit margin |
9 | Disruptive innovation in the Industry |
10 | Technology trends in the Industry |
11 | Consumer trends in the industry |
12 | Recent Production Milestones |
13 | Component Manufacturing in US, EU and China |
14 | COVID-19 impact on overall market |
15 | COVID-19 impact on Production of components |
16 | COVID-19 impact on Point of sale |
17 | Market Segmentation, Dynamics and Forecast by Geography, 2022-2030 |
18 | Market Segmentation, Dynamics and Forecast by Product Type, 2022-2030 |
19 | Market Segmentation, Dynamics and Forecast by Application, 2022-2030 |
20 | Market Segmentation, Dynamics and Forecast by End use, 2022-2030 |
21 | Product installation rate by OEM, 2022 |
22 | Incline/Decline in Average B-2-B selling price in past 5 years |
23 | Competition from substitute products |
24 | Gross margin and average profitability of suppliers |
25 | New product development in past 12 months |
26 | M&A in past 12 months |
27 | Growth strategy of leading players |
28 | Market share of vendors, 2022 |
29 | Company Profiles |
30 | Unmet needs and opportunity for new suppliers |
31 | Conclusion |
32 | Appendix |