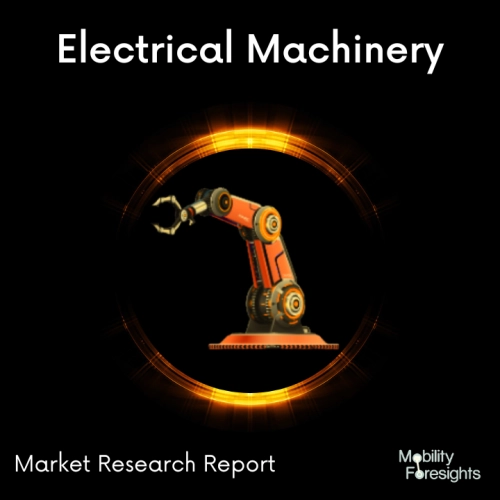
- Get in Touch with Us
Last Updated: Apr 25, 2025 | Study Period: 2023-2030
Forging presses are powerful machines used in the industry to shape and form metal parts during the forging process. They play a key role in the production of many products, from auto parts to aerospace components. Thanks to the enormous power and precision, forging presses enable the creation of strong and durable metal parts that meet the strict requirements of various industries.
At the heart of the forging press is a strong frame designed to withstand the tremendous forces generated during the forging process. The frame provides a stable structure that supports other components and ensures smooth and precise operation. It is usually made of durable steel and designed to withstand the high pressures and shocks associated with forging.
A hydraulic or mechanical power system is used in a forging press to generate the force necessary to shape the metal. Hydraulic forging presses use hydraulic cylinders and pumps to generate and control power, while mechanical forging presses use mechanical linkages and flywheels. Both systems are capable of generating high force, which allows metal to be accurately and precisely deformed.
One of the main components of a forging press is the die, which is responsible for forming the metal workpiece. The molds are made of hardened steel and are designed to withstand the forces and temperatures of the forging process.
The mold consists of two halves: the upper part, known as the upper mold, and the lower half, called the bottom. These halves connect the workpiece and form it into the desired shape. The molds can be adapted to produce different shapes and sizes, which allows the production of complex and intricate metal parts.
Forging presses can be classified by operating mode, such as mechanical, hydraulic or hybrid. Mechanical forging presses use a mechanical power system, usually powered by an electric motor, to generate the force required for forging.
These clamps offer fast performance and precise control, making them suitable for applications where speed and accuracy are critical. Hydraulic forging presses, on the other hand, use hydraulic power to generate force. They offer great strength and are often used for heavy forging work.
Hybrid forging presses combine the advantages of both mechanical and hydraulic systems, offering a balance between speed, power and controllability.
The Global Forging Presses Market accounted for $XX Billion in 2022 and is anticipated to reach $XX Billion by 2030, registering a CAGR of XX% from 2023 to 2030.
Product: Mecmold 1000T hydraulic forging press
Company: Mecmold
Description: The Mecmold 1000T hydraulic forging press is a high-performance press capable of producing complex parts with tight tolerances. It has a load capacity of 1000 tons, a travel length of 20 meters and the ability to forge with a closed die. The press also has several features that improve accuracy and productivity, such as a closed-loop control system and a hydraulic servo motor.
Product: SMS Meer 3000MT vise
Company: SMS Meer
Description: The screw press SMS Meer 3000MT is a high capacity press capable of producing large and heavy parts. It has a load capacity of 3,000 tons, a travel length of 10 meters and a screw drive mechanism. The press also has several features that improve accuracy and productivity, such as a closed-loop control system and a hydraulic servo motor.
Product: Komatsu 2000 ton hydraulic forging press
Company: Komatsu
Description: The Komatsu 2000 Ton Hydraulic Forging Press is a high-performance press capable of producing complex parts with tight tolerances. It has a load capacity of 2,000 tons, a travel length of 15 meters and a closed die forging capability. The press also has several features that improve accuracy and productivity, such as a closed-loop control system and a hydraulic servo motor.
Sl no | Topic |
1 | Market Segmentation |
2 | Scope of the report |
3 | Abbreviations |
4 | Research Methodology |
5 | Executive Summary |
6 | Introduction |
7 | Insights from Industry stakeholders |
8 | Cost breakdown of Product by sub-components and average profit margin |
9 | Disruptive innovation in the Industry |
10 | Technology trends in the Industry |
11 | Consumer trends in the industry |
12 | Recent Production Milestones |
13 | Component Manufacturing in US, EU and China |
14 | COVID-19 impact on overall market |
15 | COVID-19 impact on Production of components |
16 | COVID-19 impact on Point of sale |
17 | Market Segmentation, Dynamics and Forecast by Geography, 2023-2030 |
18 | Market Segmentation, Dynamics and Forecast by Product Type, 2023-2030 |
19 | Market Segmentation, Dynamics and Forecast by Application, 2023-2030 |
20 | Market Segmentation, Dynamics and Forecast by End use, 2023-2030 |
21 | Product installation rate by OEM, 2023 |
22 | Incline/Decline in Average B-2-B selling price in past 5 years |
23 | Competition from substitute products |
24 | Gross margin and average profitability of suppliers |
25 | New product development in past 12 months |
26 | M&A in past 12 months |
27 | Growth strategy of leading players |
28 | Market share of vendors, 2023 |
29 | Company Profiles |
30 | Unmet needs and opportunity for new suppliers |
31 | Conclusion |
32 | Appendix |