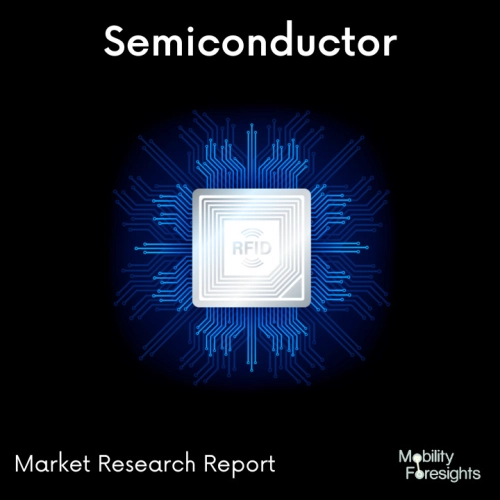
- Get in Touch with Us
Last Updated: Apr 26, 2025 | Study Period: 2023-2030
Oxygen, argon, CF4 or other suitable gases are used to form a plasma during the plasma etching process, which is used to remove material from a substrate's surface. In the semiconductor industry, etching is a crucial procedure for creating patterns on silicon wafers for microelectronic and dielectric devices.
In its vacuum chamber, the FPD Plasma Etch/Ash systems create plasma to etch thin-film and create electrical circuits on large-area glass substrates. Our solutions aid in the production of organic light-emitting diode displays (OLEDs) or liquid crystal displays (LCDs) on Gen6/Gen8/Gen10. 5 substrate.
Semiconducting materials are currently processed via plasma etching in order to utilise them in the creation of electronics. When utilised in electronic devices, small features can be etched onto the surface of a semiconducting material to improve efficiency or particular qualities.\
When one substance etchings much more quickly than another, it is said to be selective etching. The difference in the quantity of materials removed over time is the consequence.
The temperature of the sample can be regulated in some plasma etching systems. In order to protect the mask, which is frequently made of photoresist, the sample is typically held between 20 and 50 degrees Celsius and is continually chilled.
The Global FPD Plasma Etch system market accounted for $XX Billion in 2022 and is anticipated to reach $XX Billion by 2030, registering a CAGR of XX% from 2023 to 2030.
The new FPD plasma etch/ash system from Tokyo Electron Limited (TEL) can work with substrates used in the manufacturing of flat panel displays (FPD). Maintaining the etching velocity and homogeneity at the right levels while handling enormous substrates measuring more than 2m on one side offers a problem in plasma etching.
The Impressio is built to boost etching effectiveness and produce a consistent plasma density in process chambers. The new product includes six turbo molecular pumps allocated to each chamber as a standard feature, which enables big flow pumping in addition to supplying process gases at a high flow rate.
.
The design of Impressio places a focus on reliability, with throughput comparable to that of fifth- or sixth-generation systems, as well as simulation-based optimization of the transfer position for supporting substrates to reduce bending on glass substrates bigger than 2 metres in length.
FPD plasma etch/ash system chambers system offers high-quality and high reliability thanks to good utilisation of the expertise of these forerunners.
Sl no | Topic |
1 | Market Segmentation |
2 | Scope of the report |
3 | Abbreviations |
4 | Research Methodology |
5 | Executive Summary |
6 | Introduction |
7 | Insights from Industry stakeholders |
8 | Cost breakdown of Product by sub-components and average profit margin |
9 | Disruptive innovation in the Industry |
10 | Technology trends in the Industry |
11 | Consumer trends in the industry |
12 | Recent Production Milestones |
13 | Component Manufacturing in US, EU and China |
14 | COVID-19 impact on overall market |
15 | COVID-19 impact on Production of components |
16 | COVID-19 impact on Point of sale |
17 | Market Segmentation, Dynamics and Forecast by Geography, 2023-2030 |
18 | Market Segmentation, Dynamics and Forecast by Product Type, 2023-2030 |
19 | Market Segmentation, Dynamics and Forecast by Application, 2023-2030 |
20 | Market Segmentation, Dynamics and Forecast by End use, 2023-2030 |
21 | Product installation rate by OEM, 2023 |
22 | Incline/Decline in Average B-2-B selling price in past 5 years |
23 | Competition from substitute products |
24 | Gross margin and average profitability of suppliers |
25 | New product development in past 12 months |
26 | M&A in past 12 months |
27 | Growth strategy of leading players |
28 | Market share of vendors, 2023 |
29 | Company Profiles |
30 | Unmet needs and opportunity for new suppliers |
31 | Conclusion |
32 | Appendix |