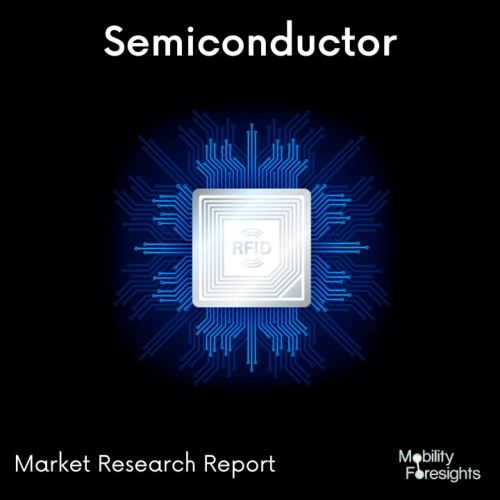
- Get in Touch with Us
Last Updated: Apr 25, 2025 | Study Period: 2023-2030
On the silicon wafer's surface, circuits are created during the Front-end Wafer Manufacturing Inspection. Thin slices of silicon ingots with a diameter ranging from 50 mm to 300 mm are known as wafers.
Numerous semiconductors with the same circuit are arranged in a lattice-like pattern on the surface of a wafer.The bottom of the wafer is where the transistor layer is created.
On top of a transistor layer, several wiring circuit layers are formed to create semiconductors. The three steps of film deposition, pattern transfer, and etching are repeated in the transistor and wiring circuit layers.
The processing that occurs in each process is described in the paragraphs that follow.Thin-film deposition: On wafers, thin films are created and employed as the building blocks for transistors and wiring. The thin sheet currently lacks any circuits or other designs.
Physical vapor deposition (PVD) and plasma CVD techniques are the major methods used for thin-film deposition. Techniques like vacuum deposition and sputtering are included in PVD.
Ionized material is impinged on the wafer surface during the sputtering process by an electrical discharge. Vacuum deposition involves exposing the deposition material to an electron beam in a vacuum to vaporize it, which then sticks to the water's surface to form the film.Electric current is used in plasma CVD to transform the raw material gas delivered on top of the substrate into a reactive plasma.
The Global Front-end Wafer Manufacturing Inspection market accounted for $XX Billion in 2022 and is anticipated to reach $XX Billion by 2030, registering a CAGR of XX% from 2023 to 2030.
As the CMP system, Advantech's Front-end Wafer Manufacturing Inspection edge solution was put in place. The system includes robotic handling equipment, a vision inspection system, CMP machinery, and uplink information for the IT database.
The location sensor then transmitted a triggering signal to the vision system after the wafers had been polished. The vision system received several images from various camera angles, analyzed them using VisionNavi software for defect checking, and then confirmed the wafers.
If a fault was found, the vision system sent either a "NG" signal to reject the wafer, or a "OK" signal to pick it up for the subsequent step. The customer's existing enterprise databases were connected with the restored image data.
Users don't have to worry about choosing appropriate goods thanks to Advantech's Front-end Wafer Manufacturing Inspection, which includes the global shutter, high-speed industrial cameras, a multi-channel computer platform, and vision software.Users of the VisionNavi software can simply construct and deploy vision inspection applications without any programming knowledge thanks to the software's graphical and flowchart-based interface.
Sl no | Topic |
1 | Market Segmentation |
2 | Scope of the report |
3 | Abbreviations |
4 | Research Methodology |
5 | Executive Summary |
6 | Introduction |
7 | Insights from Industry stakeholders |
8 | Cost breakdown of Product by sub-components and average profit margin |
9 | Disruptive innovation in the Industry |
10 | Technology trends in the Industry |
11 | Consumer trends in the industry |
12 | Recent Production Milestones |
13 | Component Manufacturing in US, EU and China |
14 | COVID-19 impact on overall market |
15 | COVID-19 impact on Production of components |
16 | COVID-19 impact on Point of sale |
17 | Market Segmentation, Dynamics and Forecast by Geography, 2022-2030 |
18 | Market Segmentation, Dynamics and Forecast by Product Type, 2022-2030 |
19 | Market Segmentation, Dynamics and Forecast by Application, 2022-2030 |
20 | Market Segmentation, Dynamics and Forecast by End use, 2022-2030 |
21 | Product installation rate by OEM, 2022 |
22 | Incline/Decline in Average B-2-B selling price in past 5 years |
23 | Competition from substitute products |
24 | Gross margin and average profitability of suppliers |
25 | New product development in past 12 months |
26 | M&A in past 12 months |
27 | Growth strategy of leading players |
28 | Market share of vendors, 2022 |
29 | Company Profiles |
30 | Unmet needs and opportunity for new suppliers |
31 | Conclusion |
32 | Appendix |