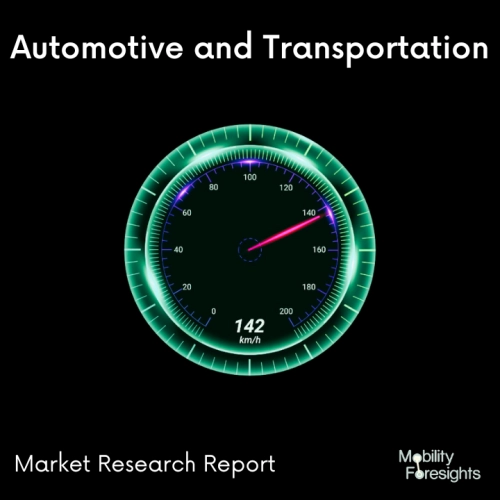
- Get in Touch with Us
Last Updated: Apr 25, 2025 | Study Period: 2023-2030
Anyone in the maintenance sector who has repaired a pump or gearbox knows that the lip seal is the one component that always appears to need changed during a rebuild. It is commonly destroyed during extraction or disassembly.
A mechanical seal is essentially a means of confining fluid within a vessel (usually pumps, mixers, etc.) in which a rotating shaft passes through a fixed housing or, on occasion, the housing revolves around the shaft.
A lip seal is a circular sealing device that encompasses either a revolving or reciprocating shaft. The lip seal excludes or includes (seals) a medium in one defined volume away from another, when leaking would indicate a product failure.
Perhaps the leaking was caused by the lip seal, which was removed from service. Whatever the case may be, lip seals are critical machine components. They keep oil and grease in while keeping impurities out. Lip seals appear to be on practically every piece of plant equipment.
PTFE (Polytetrafluoroethylene (PTFE) is a fluoropolymer that is popularly recognised by the brand name Teflon.) Low friction seals have the lowest coefficient of friction of any solid material known to man.
This enables PSI Duron® materials, which are constructed of PTFE and PTFE compounds, to create a low friction sealing system for your application.
The Global Fuel Cell Low Friction Lip Seal Market accounted for $XX Billion in 2022 and is anticipated to reach $XX Billion by 2030, registering a CAGR of XX% from 2023 to 2030.
Freudenberg Sealing Technologies provides conventional Forseal designs from its extensive, cost-effective catalog product range.
Forseal FOI as an internally sealing, axially moved rod seal and Forseal FOA as an externally sealing, axially moved piston seal are included.
This single active seal variety is constructed of PTFE 10/F56110 and comes with a metallic tensioning spring made of 1.4310 steel.
It is readily accessible for piston diameters ranging from 5 to 200 mm (in certain cases as stocked items). Furthermore, unique measurements can be produced upon request.
Forseal can also be tailored to individual material and design requirements as a customer-specific solution, such as a rotating seal with a radial/axial direction of action.
Forseal may be designed using a wide range of PTFE compounds and spring materials. Other Freudenberg Sealing Technologies compounds are available for unique requirements, such as those in medical technology.
That implies the seal may be tailored to meet specific needs. Forseal springs are typically made of stainless steel . Freudenberg Seal Technologies also supplies specific spring materials like Hastelloy C276 to reliably seal applications in demanding media.
Saint-Gobain's High Speed Lip Seals satisfy the severe demands of today's increasingly rapid EV electric drive units. They are built to withstand extremes in speed, friction, operating temperature, and, most importantly, frictional surface heat in both oil-cooled and water-glycol-cooled systems.
Their space-saving design comprises a PTFE seal within a protective metal casing. Each seal is specifically suited to your requirements and extensively tested against the circumstances of your application. It offers a low-cost, easy-to-assemble solution that may be produced in big or small quantities.
The incorporation of e-motors, gearing, and power electronics into e-axles is a relatively recent development for everyone in the business.
However, Saint-Gobain has a head start due to our familiarity with similar sealing issues in aircraft applications.
The High Speed Lip Seals' construction and shape provide dependable sealing in both forward and backward directions, with very minimal leakage.
The material's qualities, like those of other Rulon products, assure a long lifespan with no deterioration. As a result, the e-axle's performance remains steady throughout its lifespan.
High Speed Lip Seals are tested at speeds and at temperatures ranging from. Importantly, the organization investigates and precisely gauges temperature at frictional surfaces.
This is a critical issue since friction surface temperatures are greater than the overall operating temperature of the e-motor. The seals have been proven to resist at these surfaces.
Sl no | Topic |
1 | Market Segmentation |
2 | Scope of the report |
3 | Abbreviations |
4 | Research Methodology |
5 | Executive Summary |
6 | Introduction |
7 | Insights from Industry stakeholders |
8 | Cost breakdown of Product by sub-components and average profit margin |
9 | Disruptive innovation in the Industry |
10 | Technology trends in the Industry |
11 | Consumer trends in the industry |
12 | Recent Production Milestones |
13 | Component Manufacturing in US, EU and China |
14 | COVID-19 impact on overall market |
15 | COVID-19 impact on Production of components |
16 | COVID-19 impact on Point of sale |
17 | Market Segmentation, Dynamics and Forecast by Geography, 2023-2030 |
18 | Market Segmentation, Dynamics and Forecast by Product Type, 2023-2030 |
19 | Market Segmentation, Dynamics and Forecast by Application, 2023-2030 |
20 | Market Segmentation, Dynamics and Forecast by End use, 2023-2030 |
21 | Product installation rate by OEM, 2023 |
22 | Incline/Decline in Average B-2-B selling price in past 5 years |
23 | Competition from substitute products |
24 | Gross margin and average profitability of suppliers |
25 | New product development in past 12 months |
26 | M&A in past 12 months |
27 | Growth strategy of leading players |
28 | Market share of vendors, 2023 |
29 | Company Profiles |
30 | Unmet needs and opportunity for new suppliers |
31 | Conclusion |
32 | Appendix |