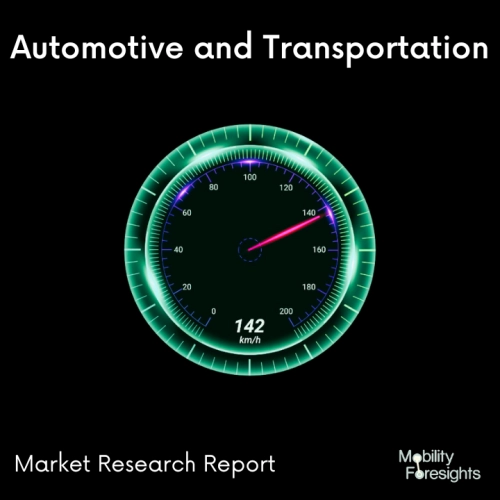
- Get in Touch with Us
Last Updated: Apr 25, 2025 | Study Period: 2023-2030
INTRODUCTION
A borescope is a tool used to peer into a building through a small opening.A sort of visual inspection known as a borescope inspection allows for the examination of difficult-to-reach or inaccessible components without destroying or disassembling them.
Multiple ultrasonic probe readings taken by DP FTS personnel provide a picture of the thickness of the tank's skin. This will show where the skin is getting so thin from corrosion that a leak is probably going to happen.
GLOBAL FUEL TANK INSPECTION BORESCOPE MARKET SIZE AND FORECAST
The Global Fuel Tank Inspection borescope Market accounted for $XX Billion in 2022 and is anticipated to reach $XX Billion by 2030, registering a CAGR of XX% from 2023 to 2030.
NEW PRODUCT LAUNCH
The Robotic Solution for Safe and Sound Tank Inspections.In order to check the coatings and basic material of the inner tank surface for damage caused by corrosion or erosion, cracks, bumps, pitting, and other conditions of the like, Shell contacted Eddyfi Technologies for an unmanned solution.
The tank wall, bottom, sides, reinforcing rings, welds, and internal components like drop tubes all needed to be inspected. Testing for wall thickness was necessary. The technology also needs to be able to investigate any problems further, such as pit depth and flaw location.For successful results, extensive cleaning is required prior to inspection, much like with a human operator.
During this testing, the robotic inspection system successfully established its ability to produce equal and better inspection data gathering than manned entry, despite the limiting factor of vessel cleanlinessual and better inspection data gathering than manned entry, despite the limiting factor of vessel cleanliness. Tank cleaning was not sufficient for a thorough examination.
The loosely integrated R-Scan probe and touchscreen Swift acquisition equipment, used in the UT section of this trial to determine loss to 1% of original tank thickness, provided the information needed while moving around on the Magg 310 crawler.
Prior to this examination, steps at a representative thickness (in this case, 5 and 10 mm based on a notional tank thickness of 6mm) were utilised in a calibration block made of a similar material, in this case, carbon steel. These were measured in order to verify the system's proper operation.
On the outer surface of the tank wall sample below, the laser scan line is visible projected, and the live acquisition data displays the coverage and laser intensity during scanning.
The trial data was gathered with the worst-case scenario in mind. With the aid of the Cloud Compare software, the output from the 3D scanner allows for accurate mapping, manipulation, and measuring of the plate sample.
For the coverage necessary to conduct an adequate investigation before making a decision, the use of complementary techniques (visual inspection, laser scanning, and ultrasonic testing) is crucial.
The robotic systems utilised in this experiment can be integrated with alternative methods like pulsed eddy current, eddy current array, tangential eddy current array, phased array ultrasonic testing, alternating current field measurement, and more developed internally by Eddyfi Technologies.
COMPANY PROFILE
THIS REPORT WILL ANSWER FOLLOWING QUESTIONS
Sl no | Topic |
1 | Market Segmentation |
2 | Scope of the report |
3 | Abbreviations |
4 | Research Methodology |
5 | Executive Summary |
6 | Introduction |
7 | Insights from Industry stakeholders |
8 | Cost breakdown of Product by sub-components and average profit margin |
9 | Disruptive innovation in the Industry |
10 | Technology trends in the Industry |
11 | Consumer trends in the industry |
12 | Recent Production Milestones |
13 | Component Manufacturing in US, EU and China |
14 | COVID-19 impact on overall market |
15 | COVID-19 impact on Production of components |
16 | COVID-19 impact on Point of sale |
17 | Market Segmentation, Dynamics and Forecast by Geography, 2023-2030 |
18 | Market Segmentation, Dynamics and Forecast by Product Type, 2023-2030 |
19 | Market Segmentation, Dynamics and Forecast by Application, 2023-2030 |
20 | Market Segmentation, Dynamics and Forecast by End use, 2023-2030 |
21 | Product installation rate by OEM, 2023 |
22 | Incline/Decline in Average B-2-B selling price in past 5 years |
23 | Competition from substitute products |
24 | Gross margin and average profitability of suppliers |
25 | New product development in past 12 months |
26 | M&A in past 12 months |
27 | Growth strategy of leading players |
28 | Market share of vendors, 2023 |
29 | Company Profiles |
30 | Unmet needs and opportunity for new suppliers |
31 | Conclusion |
32 | Appendix |