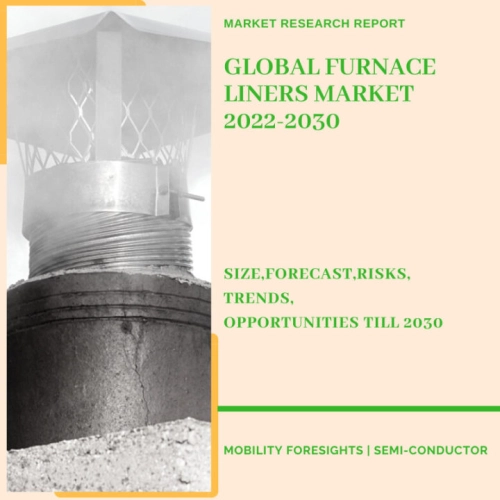
- Get in Touch with Us
Last Updated: Apr 25, 2025 | Study Period: 2022-2030
For oxidation, diffusion, and CVD purposes, silicon wafers are typically heated in a furnace known as a diffusion or oxidation furnace during the semiconductor manufacturing process.
In a diffusion furnace, silicon wafers are heated by being placed inside an inner tube such as a liner tube or diffusion tube. While the diffusion tube is typically made of silicon carbide or quartz, the liner tube is typically made of silicon carbide, quartz, or mullite.
The heating coils that surround the inner tube of the diffusion furnace deteriorate and sag into touch with the tube over time and repeatedly operate the furnace. The silicon carbide tube tends to crack as a result of arcing when it comes into contact with the heating coils.
The Global Furnace liners market accounted for $XX Billion in 2021 and is anticipated to reach $XX Billion by 2030, registering a CAGR of XX% from 2022 to 2030.
Isothermal Furnace Liners (IFLs) are liquid metal heat pipes in the form of rings that offer a working environment with a constant temperature. Boyd Corporation's IFLs achieve isothermal wall temperature to maximise production while saving time and energy. The IFL has no moving parts, is easy to install, offers design flexibility, and is incredibly dependable and economical.
The IFL does not rely on heat transfer channels connecting to adjacent walls or the outside environment, unlike probes. Boyd IFLs use a single heater and controller to create a single, uniform temperature zone in the majority of applications.
Two or more IFLs may be used in sequence for various, individually regulated zones or step changes in temperature profile. Frequent profile readings are not required for temperature adjustment, which is a straightforward one-step procedure.
The blast furnace liners have steadily developed from a relatively slender blast furnace to a relatively squat furnace type that complies with the raw material conditions and operating system due to the improvement of raw fuel conditions and operation. The blast furnace technology tends to be squat and extend horizontally with the further improvement of raw material circumstances and operating levels.
The lining is primarily formed of clay refractory bricks; the thickness of the lining at the furnace's bottom is 2700 mm to 3200mm, and the thickness of the lining above the furnace waist is 900mm to 1150mm pricing of sillimanite bricks.At this point, there is, nevertheless, a propensity to use advanced refractory materials blindly, which leads to substantial investment and little benefit.
The refractories for blast furnaces liners in China have not altered considerably, despite the appearance of the second and third generations of cooling staves elsewhere. Graphite or semi-graphite carbon bricks, silicon carbide bricks coupled with silicon nitride, sillimanite bricks, and other materials are used to line the blast furnace.
The lower portion of the furnace body was where the disagreement over the blast furnace's duration was transferred from the bottom of the furnace, and this is where attention was first drawn to the lower portion of the furnace body's lifespan.
Therefore, new technologies including the cooling stave, copper cooling stave and cooling plate, soft water closed-circuit circulation cooling, as well as other new equipment and new procedures, have emerged to extend the life of the lower part of the furnace body.
The blast furnace's inside lining has undergone significant modifications. The tuyere, iron mouth, and slag mouth areas use combined refractory bricks; the furnace waist and furnace body are made of silicon carbide bricks, aluminium carbon bricks, silicon nitride combined silicon carbide bricks, and other parts with different materials of refractory materials.
The furnace bottom uses a water-cooled thin furnace bottom, and the furnace bottom and hearth use carbon bricks, hot-pressed carbon bricks, or ceramic cup bricks, etc.The high-alumina refractory bricks and clay bricks used in the brick-inlaid cooling stave have given way to aluminium-inlaid carbon bricks, silicon carbide bricks, or high-efficiency refractory ramming materials.
Sl no | Topic |
1 | Market Segmentation |
2 | Scope of the report |
3 | Abbreviations |
4 | Research Methodology |
5 | Executive Summary |
6 | Introduction |
7 | Insights from Industry stakeholders |
8 | Cost breakdown of Product by sub-components and average profit margin |
9 | Disruptive innovation in the Industry |
10 | Technology trends in the Industry |
11 | Consumer trends in the industry |
12 | Recent Production Milestones |
13 | Component Manufacturing in US, EU and China |
14 | COVID-19 impact on overall market |
15 | COVID-19 impact on Production of components |
16 | COVID-19 impact on Point of sale |
17 | Market Segmentation, Dynamics and Forecast by Geography, 2022-2030 |
18 | Market Segmentation, Dynamics and Forecast by Product Type, 2022-2030 |
19 | Market Segmentation, Dynamics and Forecast by Application, 2022-2030 |
20 | Market Segmentation, Dynamics and Forecast by End use, 2022-2030 |
21 | Product installation rate by OEM, 2022 |
22 | Incline/Decline in Average B-2-B selling price in past 5 years |
23 | Competition from substitute products |
24 | Gross margin and average profitability of suppliers |
25 | New product development in past 12 months |
26 | M&A in past 12 months |
27 | Growth strategy of leading players |
28 | Market share of vendors, 2022 |
29 | Company Profiles |
30 | Unmet needs and opportunity for new suppliers |
31 | Conclusion |
32 | Appendix |