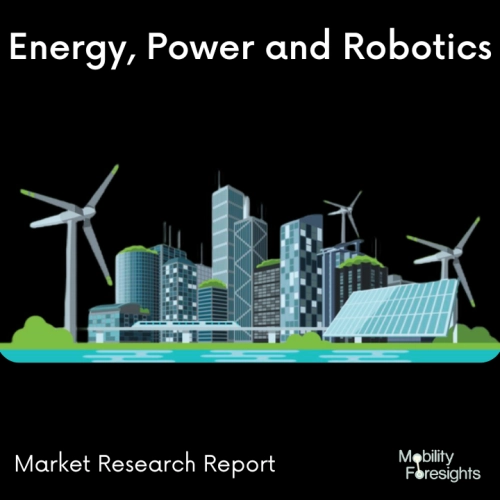
- Get in Touch with Us
Last Updated: Apr 25, 2025 | Study Period: 2023-2030
A turbine inspection system is an essential component in the regular maintenance of a turbine. It is a comprehensive system that inspects and evaluates the condition of its components, such as blades, vanes, seals, and bearings. This ensures that the turbine operates safely, efficiently, and reliably.
Turbine inspection systems are designed to identify potential problems before they become serious and require costly repairs. This is done by performing routine inspections and tests on the turbine components.
These inspections include visual inspections, vibration monitoring, and acoustic emission testing. The latter two use specialized equipment to measure the vibration and sound created by the turbine while it is in operation.
This data can then be used to identify potential issues and allow for timely maintenance and repairs.
The system also includes sensors that monitor the temperature, pressure, and flow of the turbine components. This data is analyzed to detect any anomalies or changes in the turbineâs performance.
These changes can indicate an impending failure, allowing for a timely response and corrective action.
The turbine inspection system is essential for keeping the turbine operating effectively and efficiently. It helps prevent expensive repairs and downtime, which can have a significant impact on a businessâs bottom line.
Regular inspections and maintenance also help ensure that the turbine meets safety and environmental regulations.
The Global Gas turbine inspection system market accounted for $XX Billion in 2022 and is anticipated to reach $XX Billion by 2030, registering a CAGR of XX% from 2023 to 2030.
GE Introduced the First 6B Repowering Gas Turbine Solution in Industry. In addition, GE revealed that it has inked its first deal for the solution with a multinational chemical business, repowering three 6B gas turbines and generating considerable annual fuel savings at its Asian location.
With a global fleet reliability of 98.4 percent, around 2 percent higher than the industry average, this fleet has acquired a reputation for being dependable. The 6B fleet is getting older at the same time that demand for improved performance is rising.
The recent addition of the Advanced Gas Path technology to the 6B fleet demonstrates how they will continue to invest in their seasoned fleets to support industrial operators and power producers in staying competitive in a highly dynamic market.
The new 6B Repowering Solution, which is a component of GE's Fleet360 platform of whole plant services, uses cutting-edge F and H class technologies to boost the machine's performance to industry-leading levels for its class.
The repowering turns the 6B unit into a GE 6F.01 gas turbine, which is also offered as a new unit, and includes a complete "flange-to-flange" upgrade of all major components, including the combustion system, hot gas path, and compressor.
Performance in gas turbine and combined-cycle operation can be improved with the new 6B Repowering upgrade, which fits inside the current 6B footprint.Increasing the major inspection period to 64,000 hours (from 48,000 hours) and the hot gas path inspection interval to 32,000 hours (from 24,000 hours).
Across the globe, GE has a fleet of more than 1,150 6B turbines that power industrial applications and energy production facilities in industries like cement production, petrochemicals, oil and gas, and exploration.
Currently, there are more than 900 6Bs in use, of which 55% are running constantly. Since its first shipment and installation at Montana-Dakota Utilitiesâ Glendive Power Plant, the 6B fleet has achieved numerous significant milestones.
At the moment, this unit runs at peak power during times of high heat or cold, when additional power is required. Most notably, the unit has proven to be incredibly flexible in accommodating Montana's huge temperature variations, which can range from -30 to 110 degrees Fahrenheit.
Sl no | Topic |
1 | Market Segmentation |
2 | Scope of the report |
3 | Abbreviations |
4 | Research Methodology |
5 | Executive Summary |
6 | Introduction |
7 | Insights from Industry stakeholders |
8 | Cost breakdown of Product by sub-components and average profit margin |
9 | Disruptive innovation in the Industry |
10 | Technology trends in the Industry |
11 | Consumer trends in the industry |
12 | Recent Production Milestones |
13 | Component Manufacturing in US, EU and China |
14 | COVID-19 impact on overall market |
15 | COVID-19 impact on Production of components |
16 | COVID-19 impact on Point of sale |
17 | Market Segmentation, Dynamics and Forecast by Geography, 2023-2030 |
18 | Market Segmentation, Dynamics and Forecast by Product Type, 2023-2030 |
19 | Market Segmentation, Dynamics and Forecast by Application, 2023-2030 |
20 | Market Segmentation, Dynamics and Forecast by End use, 2023-2030 |
21 | Product installation rate by OEM, 2023 |
22 | Incline/Decline in Average B-2-B selling price in past 5 years |
23 | Competition from substitute products |
24 | Gross margin and average profitability of suppliers |
25 | New product development in past 12 months |
26 | M&A in past 12 months |
27 | Growth strategy of leading players |
28 | Market share of vendors, 2023 |
29 | Company Profiles |
30 | Unmet needs and opportunity for new suppliers |
31 | Conclusion |
32 | Appendix |