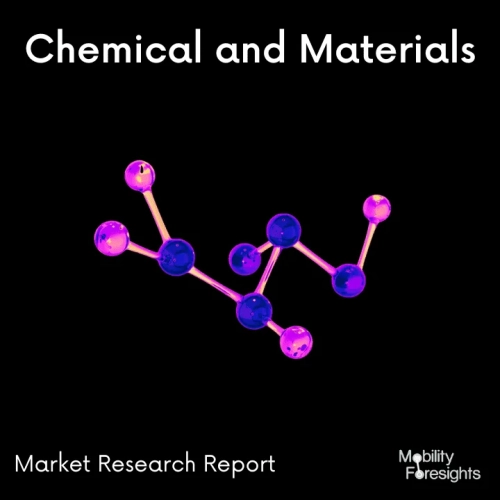
- Get in Touch with Us
Last Updated: Jul 07, 2025 | Study Period: 2025-2031
The demand for lightweight and fuel-efficient vehicles in GCC is significantly driving the adoption of automotive composites across OEMs and Tier 1 suppliers.
Increasing electric vehicle (EV) production in GCC is accelerating the need for high-performance, lightweight composite materials to improve energy efficiency.
Stringent emission regulations and sustainability mandates in GCC are compelling automakers to shift from traditional metals to recyclable and bio-based composites.
Growing use of carbon fiber and glass fiber composites in both structural and non-structural automotive parts is reshaping design and engineering capabilities in GCC.
Rising adoption of advanced manufacturing techniques like resin transfer molding (RTM) and compression molding is reducing production costs in GCC.
Collaborations between automotive manufacturers and material science companies in GCC are fostering innovation in hybrid composites and multifunctional components.
The increasing penetration of composites in interior, exterior, and under-the-hood applications is driving volume growth across luxury and mid-range vehicle segments in GCC.
The GCC Automotive Composites Market is projected to grow from USD 3.6 billion in 2025 to approximately USD 7.8 billion by 2031, registering a Compound Annual Growth Rate (CAGR) of 13.5%during the forecast period.
This growth is primarily driven by the automotive industry’s transition to lightweight design, increasing EV production, and the integration of composite materials in a broader range of vehicle parts to enhance strength-to-weight ratios and fuel economy.
The GCC Automotive Composites Market focuses on the production and utilization of advanced composite materials—mainly carbon fiber, glass fiber, and natural fiber-reinforced polymers—in the automotive industry. These materials offer superior mechanical strength, corrosion resistance, and weight reduction benefits compared to conventional metals.
In GCC, automotive composites are playing a critical role in the transformation of vehicle architecture, contributing to lightweighting initiatives, safety enhancements, and energy efficiency. With rising regulatory pressures and the electrification of mobility, composites are increasingly being adopted across structural, interior, and aesthetic vehicle applications.
Rising Demand for Fuel Efficiency and Weight Reduction
Automakers in GCC are under increasing pressure to improve fuel economy and reduce vehicle emissions, prompting the replacement of heavy metal parts with lighter composite alternatives.
Acceleration of Electric Vehicle (EV) Production
As EV adoption surges in GCC, manufacturers are prioritizing lightweight materials like carbon fiber and thermoplastic composites to offset battery weight and extend driving range.
Stringent Emission and Safety Regulations
Regulatory bodies in GCC are imposing stricter emission standards and crash safety requirements, which composites help meet due to their superior energy absorption and lightweight properties.
Advancements in Composite Manufacturing Technologies
The rise of automated and cost-effective production techniques such as resin transfer molding (RTM), vacuum infusion, and compression molding is enabling scalable composite manufacturing in GCC.
Expansion of Premium and Luxury Automotive Segments
High-end vehicles in GCC are increasingly incorporating composite materials in body panels, roof structures, and suspension systems to deliver performance advantages and aesthetic appeal.
Increased Use of Hybrid Composites
Manufacturers in GCC are combining carbon and glass fibers or integrating thermoplastics with natural fibers to develop cost-effective, performance-optimized hybrid composites.
Integration in EV Battery Enclosures and Structural Parts
Composite materials are being adopted in GCC for battery casings, underbody panels, and crash structures in EVs to ensure thermal stability, EMI shielding, and structural strength.
Growth in Recyclable and Bio-Based Composites
Sustainability goals are driving the development of bio-composites and recyclable thermoplastics in GCC, particularly for interior components and decorative trims.
Localization of Composite Supply Chains
Automotive OEMs in GCC are focusing on near-shore sourcing and domestic production of composite materials to reduce lead times and enhance supply chain resilience.
Smart Composites and Functional Integration
Research in GCC is expanding toward smart composites embedded with sensors, actuators, or energy-harvesting capabilities for next-gen connected and autonomous vehicles.
High Material and Processing Costs
Despite long-term benefits, the upfront costs of carbon fiber and advanced composites remain high in GCC, limiting their use in mass-market vehicles.
Complexity in Recycling and End-of-Life Management
Thermoset composites and multi-material assemblies present recycling challenges, requiring specialized processes that are not yet widely implemented in GCC.
Design and Engineering Constraints
Incorporating composites into vehicle structures in GCC often requires re-engineering components and manufacturing processes, increasing time-to-market.
Limited Skilled Workforce and Technical Know-how
The shortage of professionals trained in composite design and fabrication techniques is slowing adoption across smaller automotive manufacturers in GCC.
Competition from Advanced High-Strength Steels and Aluminum
In some applications, high-strength metals continue to offer cost advantages over composites, especially in commercial vehicle segments in GCC.
Carbon Fiber Composites
Glass Fiber Composites
Natural Fiber Composites
Hybrid Composites
Others (Aramid, Basalt, etc.)
Thermoset Resins
Epoxy
Polyester
Vinyl Ester
Thermoplastic Resins
Polypropylene
Polyamide
Polycarbonate
Resin Transfer Molding (RTM)
Injection Molding
Compression Molding
Vacuum Infusion
Filament Winding
Hand Layup and Spray-Up
Exterior Components (Bumpers, Hoods, Panels)
Interior Components (Dashboards, Door Panels, Seats)
Powertrain and Under-the-Hood
Structural Components (Chassis, Suspension, Roof)
Battery Enclosures (EVs)
Others (Crash Structures, Floor Trays)
Passenger Cars
Light Commercial Vehicles (LCVs)
Heavy Commercial Vehicles (HCVs)
Electric Vehicles (EVs)
Sports and Luxury Vehicles
Original Equipment Manufacturers (OEMs)
Aftermarket and Tier Suppliers
SGL Carbon SE
Toray Industries, Inc.
Teijin Limited
Owens Corning
Mitsubishi Chemical Corporation
Hexcel Corporation
UFP Technologies, Inc.
Solvay SA
BASF SE
SABIC
Toray Industries expanded its carbon fiber production facility in GCC to meet growing demand from electric vehicle manufacturers.
Teijin Limited collaborated with a leading OEM in GCC to develop high-performance carbon composite panels for lightweight SUVs.
Hexcel Corporation partnered with aerospace suppliers in GCC to repurpose aerospace-grade composites for high-end automotive applications.
Owens Corning introduced a new range of glass fiber mats in GCC optimized for battery enclosure insulation and thermal protection.
SGL Carbon launched thermoplastic carbon fiber prepregs in GCC to support automated mass production for mid-range passenger vehicles.
Sl no | Topic |
1 | Market Segmentation |
2 | Scope of the report |
3 | Research Methodology |
4 | Executive summary |
5 | Key Predictions of GCC Automotive Composites Market |
6 | Avg B2B price of GCC Automotive Composites Market |
7 | Major Drivers For GCC Automotive Composites Market |
8 | Global GCC Automotive Composites Market Production Footprint - 2024 |
9 | Technology Developments In GCC Automotive Composites Market |
10 | New Product Development In GCC Automotive Composites Market |
11 | Research focus areas on new GCC Automotive Composites |
12 | Key Trends in the GCC Automotive Composites Market |
13 | Major changes expected in GCC Automotive Composites Market |
14 | Incentives by the government for GCC Automotive Composites Market |
15 | Private investements and their impact on GCC Automotive Composites Market |
16 | Market Size, Dynamics, And Forecast, By Type, 2025-2031 |
17 | Market Size, Dynamics, And Forecast, By Output, 2025-2031 |
18 | Market Size, Dynamics, And Forecast, By End User, 2025-2031 |
19 | Competitive Landscape Of GCC Automotive Composites Market |
20 | Mergers and Acquisitions |
21 | Competitive Landscape |
22 | Growth strategy of leading players |
23 | Market share of vendors, 2024 |
24 | Company Profiles |
25 | Unmet needs and opportunities for new suppliers |
26 | Conclusion |