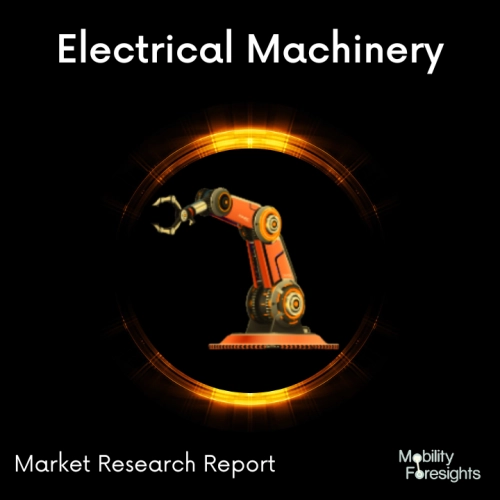
- Get in Touch with Us
Last Updated: Apr 25, 2025 | Study Period: 2023-2030
Gear inspection is a crucial step in making sure that the created gear is of a high enough standard overall. It also offers information on the effectiveness and degree of control of the manufacturing process.
There is no way to trace an effect back to its cause without knowing the exact geometry of the gear that is being tested. Any two gears will interact with one another depending on their contact geometry and the lubrication layer controlling the transfer of energy.
The Global Gear Inspection Machine market accounted for $XX Billion in 2022 and is anticipated to reach $XX Billion by 2030, registering a CAGR of XX% from 2023 to 2030.
The new M62 Laser Profiler for Gear Inspection from Marposs, which makes use of optical triangulation and laser profile sensors, has been launched.
The profiler's use of laser technology makes it easier to adapt for checking a variety of gear sizes and forms in a short amount of time as compared to specialised gear gauging systems or gear laboratory machines.
An image sensor situated behind the optical receiver is used by the laser profilers to project a laser line onto the gear at a precise angle, collecting data to create the whole Z-X profile.
The requested measurement and inspection tasks are subsequently carried out by the system. In order to find any irregularities, line operators can quickly evaluate photos and move to the desired level of detail.
The laser profiler has the ability to measure characteristics with tolerances up to 5 to 10 m and can inspect odd or even toothed helical and spur gears with exterior diameters of 30 to 300 mm and heights of 15 to 40 mm.
It has the accuracy to precisely analyse micro-geometric parameters, such as Profile crowning (C), Profile slope deviation (fh), and Total profile form deviation (Ffa), with a cycle time of around 40 seconds.
This noncontact system can interface with Marposs electronic measurement display units, like the potent E9066 industrial computer, which has a sophisticated graphic display algorithm for gear analysis as well as thorough statistical calculations. This noncontact system can also be used with other Marposs gear measurement solutions.
Sl no | Topic |
1 | Market Segmentation |
2 | Scope of the report |
3 | Abbreviations |
4 | Research Methodology |
5 | Executive Summary |
6 | Introduction |
7 | Insights from Industry stakeholders |
8 | Cost breakdown of Product by sub-components and average profit margin |
9 | Disruptive innovation in the Industry |
10 | Technology trends in the Industry |
11 | Consumer trends in the industry |
12 | Recent Production Milestones |
13 | Component Manufacturing in US, EU and China |
14 | COVID-19 impact on overall market |
15 | COVID-19 impact on Production of components |
16 | COVID-19 impact on Point of sale |
17 | Market Segmentation, Dynamics and Forecast by Geography, 2023-2030 |
18 | Market Segmentation, Dynamics and Forecast by Product Type, 2023-2030 |
19 | Market Segmentation, Dynamics and Forecast by Application, 2023-2030 |
20 | Market Segmentation, Dynamics and Forecast by End use, 2023-2030 |
21 | Product installation rate by OEM, 2023 |
22 | Incline/Decline in Average B-2-B selling price in past 5 years |
23 | Competition from substitute products |
24 | Gross margin and average profitability of suppliers |
25 | New product development in past 12 months |
26 | M&A in past 12 months |
27 | Growth strategy of leading players |
28 | Market share of vendors, 2023 |
29 | Company Profiles |
30 | Unmet needs and opportunity for new suppliers |
31 | Conclusion |
32 | Appendix |