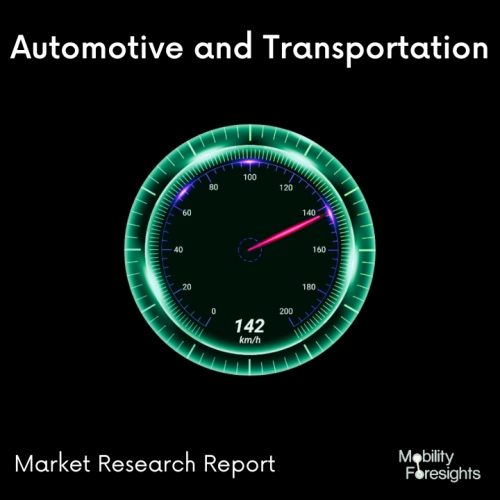
- Get in Touch with Us
Last Updated: Apr 25, 2025 | Study Period: 2023-2030
In order to power an electrical system, such as an energy storage system or an electric vehicle (EV), a battery pack is a device that stores electrical energy (ESS). The battery pack has cells that are all interconnected and used to store energy.
Due to their significantly higher energy density as compared to weight, lithium-ion and lithium polymer batteries are typically seen in modern electric vehicles. Lithium, manganese, cobalt, graphite, steel, and nickel are the main chemical components needed in lithium-ion batteries.
They are created using lithium salt, metal oxide, carbon or graphite, and carbon. These substances interact with electrolytes to form the positive and negative electrodes, which are what generate electric current.
Although the specific chemistry frequently differs from that of consumer electronics batteries, the majority of all-electric and plug-in hybrid vehicles on the road today use lithium-ion batteries. In order to lower their relatively high cost, increase their usable life, and address safety issues with overheating, research and development are still being done on these products.
There are three main battery kinds that can be used by consumers. They are lithium ion, nickel metal hydride, and alkaline. Each type has benefits and drawbacks. Each of them has a unique place in the history of technology.
Primary and secondary, or rechargeable, battery packs are the two main categories. Primary batteries are non-rechargeable, single-use items. Once they run out of energy, they need to be replaced. Active components in secondary or rechargeable batteries can be renewed.
The Global Glass-Fiber PP EV Battery Pack market accounted for $XX Billion in 2022 and is anticipated to reach $XX Billion by 2030, registering a CAGR of XX% from 2023 to 2030.
SABIC is introducing To meet the demand for lighter, thinner, and more crash-resistant battery modules and housings two new grades of NORYL resin. The NORYL NHP6011 and NHP6012 resins, two new cutting-edge materials, meet crucial consumer demands for increased safety, range, and power.
They provide improved strong impact strength and flame retardancy to fulfil strict industrial safety standards, as well as thin-wall moulding capability to reduce weight and fit more cells, assisting in extending vehicle range and improving performance.
These innovative polyphenylene ether (PPE)-copolymer-based glass fiber-reinforced NORYL resins are the most recent additions to SABIC's expanding NHP family of materials for mobility applications.
In order to increase the use of electric vehicles and reap the full sustainability benefits of e-mobility, batteries must be optimised for Resins & Compounds in SABIC's Specialties business. "Our new NORYL resins can assist manufacturers in enhancing EV batteries through improved safety, more energy density, and reduced weight, which can also serve to increase the customer attractiveness of their vehicles.
Sl no | Topic |
1 | Market Segmentation |
2 | Scope of the report |
3 | Abbreviations |
4 | Research Methodology |
5 | Executive Summary |
6 | Introduction |
7 | Insights from Industry stakeholders |
8 | Cost breakdown of Product by sub-components and average profit margin |
9 | Disruptive innovation in the Industry |
10 | Technology trends in the Industry |
11 | Consumer trends in the industry |
12 | Recent Production Milestones |
13 | Component Manufacturing in US, EU and China |
14 | COVID-19 impact on overall market |
15 | COVID-19 impact on Production of components |
16 | COVID-19 impact on Point of sale |
17 | Market Segmentation, Dynamics and Forecast by Geography, 2023-2030 |
18 | Market Segmentation, Dynamics and Forecast by Product Type, 2023-2030 |
19 | Market Segmentation, Dynamics and Forecast by Application, 2023-2030 |
20 | Market Segmentation, Dynamics and Forecast by End use, 2023-2030 |
21 | Product installation rate by OEM, 2023 |
22 | Incline/Decline in Average B-2-B selling price in past 5 years |
23 | Competition from substitute products |
24 | Gross margin and average profitability of suppliers |
25 | New product development in past 12 months |
26 | M&A in past 12 months |
27 | Growth strategy of leading players |
28 | Market share of vendors, 2023 |
29 | Company Profiles |
30 | Unmet needs and opportunity for new suppliers |
31 | Conclusion |
32 | Appendix |