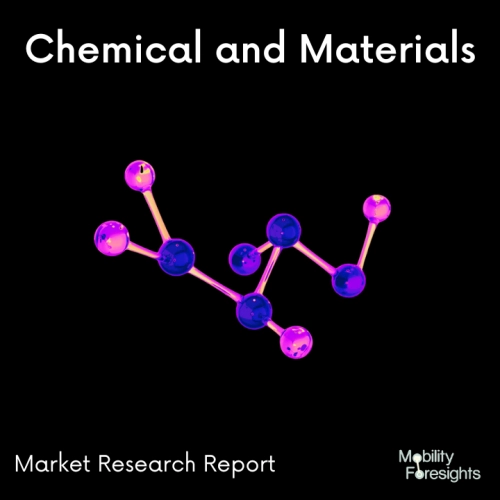
- Get in Touch with Us
Last Updated: Apr 25, 2025 | Study Period: 2024-2030
A glass lined reactor is used given their compatibility with a wide range of chemicals. The reactor is a vessel with an agitator that allow the mixing of chemicals in a contained environment.
The reactor can be pressurized and operate in a range of temperatures. The top section of the reactor allows the process nozzles to connect which bring in the chemicals and gases as appropriate and allow for cleaning head nozzles.
They have a number of sizes.A reactor works by allowing the chemicals into a contained space and agitating them via the centrally mounted agitator. The vessel will typically have baffles included to ensure the sufficient level of turbulence inside to mix / blend the chemicals and enable the reactor.
Normal chemical reactions take place given the correct catalysts present, the chemicals and pressure / temperature conditions and contact time. The end product could be crystalline or liquid.
Glass Lined Reactors consist of a main body, top section with connecting nozzles & man way, baffles, dip pipes, agitator with mechanical seal, tank outlet valve and jacket for thermal transfer. Smaller components such as bursting discs and sight glasses are also used frequently for pressure relief and visibility.
The Global Glass Lined Reactor market accounted for $XX Billion in 2023 and is anticipated to reach $XX Billion by 2030, registering a CAGR of XX% from 2024 to 2030.
PFAUDLER - Typically, a glass-lined reactor, whether DIN standard or customized, consists of: A glass-lined inner vessel: starting from 4 liters, up to 80,000 liters, in which the reactive media is loaded and processed ; An external heating cooling system, in most cases, a jacket with agitating nozzles or, for specific conditions.
half pipe circuits ; An agitator, single or multi-stage. (up to 7 stages already achieved by P fiddler through its Cryo-Lock system) ; Internals, such as removable baffles, dip pipes, instrument carriers.
(temperature, pH, corrosion monitoring, sampling systems, cleaning lances, etc.) ; An agitator drive with motor, gear box, coupling, mechanical shaft sealing units and now the modern INTERSEAL dry9000 technology for shaft sealing
Sl no | Topic |
1 | Market Segmentation |
2 | Scope of the report |
3 | Abbreviations |
4 | Research Methodology |
5 | Executive Summary |
6 | Introduction |
7 | Insights from Industry stakeholders |
8 | Cost breakdown of Product by sub-components and average profit margin |
9 | Disruptive innovation in the Industry |
10 | Technology trends in the Industry |
11 | Consumer trends in the industry |
12 | Recent Production Milestones |
13 | Component Manufacturing in US, EU and China |
14 | COVID-19 impact on overall market |
15 | COVID-19 impact on Production of components |
16 | COVID-19 impact on Point of sale |
17 | Market Segmentation, Dynamics and Forecast by Geography, 2024-2030 |
18 | Market Segmentation, Dynamics and Forecast by Product Type, 2024-2030 |
19 | Market Segmentation, Dynamics and Forecast by Application, 2024-2030 |
20 | Market Segmentation, Dynamics and Forecast by End use, 2024-2030 |
21 | Product installation rate by OEM, 2023 |
22 | Incline/Decline in Average B-2-B selling price in past 5 years |
23 | Competition from substitute products |
24 | Gross margin and average profitability of suppliers |
25 | New product development in past 12 months |
26 | M&A in past 12 months |
27 | Growth strategy of leading players |
28 | Market share of vendors, 2023 |
29 | Company Profiles |
30 | Unmet needs and opportunity for new suppliers |
31 | Conclusion |
32 | Appendix |