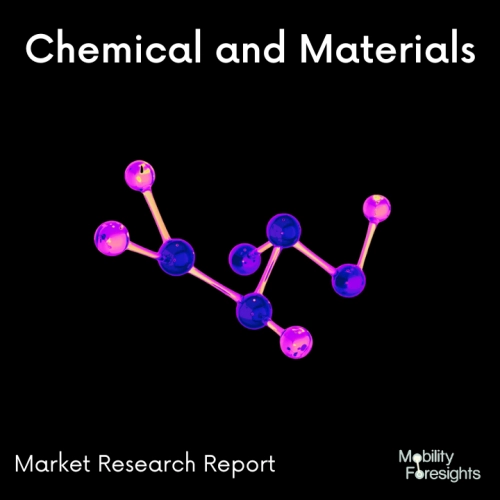
- Get in Touch with Us
Last Updated: Apr 25, 2025 | Study Period: 2024-2030
Glass refractories play a vital role in various industrial applications, offering exceptional resistance to high temperatures and harsh chemical environments.
These specialized materials are essential for the construction of furnaces, kilns, and other thermal processing units utilized in the glass manufacturing, metallurgy, cement, and petrochemical industries.
Their unique properties enable them to withstand extreme conditions, ensuring the smooth operation and longevity of the industrial processes they support.
At its core, a glass refractory is a material that exhibits high refractoriness, meaning it can withstand and retain its strength and shape at elevated temperatures without undergoing significant deformation or degradation.
This characteristic is particularly crucial in glassmaking processes, where molten glass is produced and shaped at temperatures exceeding 1,000°C (1,832°F).
Regular materials would fail under such extreme conditions, making refractories indispensable.
One of the primary components of glass refractories is silica (SiO2), which possesses excellent thermal resistance and chemical stability.
However, various other materials are incorporated, including alumina, magnesia, zirconia, and carbon, depending on the specific application and operating conditions.
These additives help tailor the refractory properties to meet the specific requirements of each industrial process, such as withstanding corrosive molten glass, reducing thermal conductivity, or enhancing mechanical strength.
Glass refractories are typically formed into bricks, blocks, or shaped components to create linings within industrial furnaces and kilns.
These linings protect the surrounding structures from the intense heat generated during the manufacturing processes, ensuring operational safety and efficiency.
Despite their remarkable properties, glass refractories are not immune to wear and erosion caused by continuous exposure to extreme temperatures and chemical attacks.
Consequently, industries must carefully select the appropriate refractory material and regularly maintain and replace worn-out linings to maximize their service life.
The Global Glass refractory market accounted for $XX Billion in 2023 and is anticipated to reach $XX Billion by 2030, registering a CAGR of XX% from 2024 to 2030.
Pyro Glass Inc.
has an illustrious reputation for engineering innovative fire-resistant materials, and Elite Fire is the latest testament to their commitment to excellence.
This state-of-the-art refractory material is meticulously engineered using a proprietary blend of advanced ceramics, reinforced with microfibers, and integrated with a cutting-edge binding agent.
The result is a glass refractory with unparalleled fire resistance, capable of withstanding extreme temperatures and thermal shocks, ensuring maximum safety and durability in critical environments.
"Ultra Vision" by Crystal Shield Co. - a revolutionary breakthrough in optical clarity and durability for glass applications.
Ultra Vision employs state-of-the-art nanotechnology, resulting in a super-thin, transparent coating that eliminates glare and enhances light transmission.
This innovative solution offers crystal-clear vision, making it an ideal choice for windows, windshields, and display panels across industries.
The advanced scratch-resistant properties ensure long-lasting performance, maintaining pristine clarity over time.
Ultra Vision's cutting-edge technology sets a new standard for glass coatings, transforming the way we experience transparency in our everyday lives.
Crystal Shield Co. continues to lead the market with their commitment to exceptional clarity and vision.
Radiance Pro" - an innovative glass refractory product proudly crafted by Radiant Refractories Ltd., a leading company known for its expertise in developing high-quality refractory solutions.
Radiant Refractories Ltd.
is renowned for its commitment to research and development, and Radiance Pro is a testament to their dedication to providing cutting-edge refractory solutions.
This revolutionary glass refractory is meticulously engineered using a combination of premium-grade raw materials, including high-purity alumina, zirconia, and silicon carbide.
The result is a refractory with exceptional thermal shock resistance, superior corrosion protection, and outstanding mechanical strength, ensuring optimal efficiency and extended service life.
Sl no | Topic |
1 | Market Segmentation |
2 | Scope of the report |
3 | Abbreviations |
4 | Research Methodology |
5 | Executive Summary |
6 | Introduction |
7 | Insights from Industry stakeholders |
8 | Cost breakdown of Product by sub-components and average profit margin |
9 | Disruptive innovation in the Industry |
10 | Technology trends in the Industry |
11 | Consumer trends in the industry |
12 | Recent Production Milestones |
13 | Component Manufacturing in US, EU and China |
14 | COVID-19 impact on overall market |
15 | COVID-19 impact on Production of components |
16 | COVID-19 impact on Point of sale |
17 | Market Segmentation, Dynamics and Forecast by Geography, 2024-2030 |
18 | Market Segmentation, Dynamics and Forecast by Product Type, 2024-2030 |
19 | Market Segmentation, Dynamics and Forecast by Application, 2024-2030 |
20 | Market Segmentation, Dynamics and Forecast by End use, 2024-2030 |
21 | Product installation rate by OEM, 2023 |
22 | Incline/Decline in Average B-2-B selling price in past 5 years |
23 | Competition from substitute products |
24 | Gross margin and average profitability of suppliers |
25 | New product development in past 12 months |
26 | M&A in past 12 months |
27 | Growth strategy of leading players |
28 | Market share of vendors, 2023 |
29 | Company Profiles |
30 | Unmet needs and opportunity for new suppliers |
31 | Conclusion |
32 | Appendix |