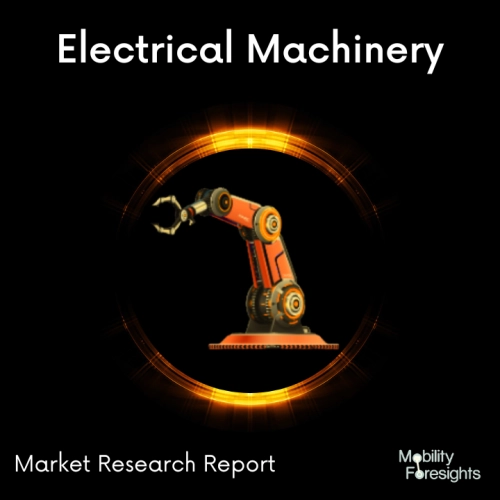
- Get in Touch with Us
Last Updated: Apr 25, 2025 | Study Period: 2023-2030
The machining of curved items, such as intricate precision moulds and cutting tools, frequently uses profile grinding. A common precision machining technique for contour surfaces is optical-enlargement-based profile grinding, and machining mistakes in this technique are typically checked manually with vision.
A projection screen is created by optically enlarging the contour of a curve component. The theoretical profile is then compared to the enlarged profile image, enabling the operator to visually check for profile errors.
Low efficiency and manual dependency are drawbacks of this approach. Consequently, it is essential to increase the precision and effectiveness of profile grinding. Together with creating powerful computerised numerical control machine tools to increase accuracy, Studies have looked into compensation approaches, which have the benefits of being low cost and very effective in improving accuracy, for minimising machining errors in a range of industrial processes.
This study offered a self-developed digital profile grinding machine as the foundation for a machine-vision-based profile error detection and compensating method.
A cutting-edge digital machine that projects a workpiece under magnification to create a fine, high-accuracy shape and uses a CCD camera for automatic on-machine measurement and automatic compensation can address issues with efficiency, quality fluctuation, and ultrafine workpiece grinding that are present in conventional projectors. Workpieces can be treated while their profiles are being examined using original drawings that are being projected at a 20-fold magnification.
The Global Graphical Profile Grinder market accounted for $XX Billion in 2022 and is anticipated to reach $XX Billion by 2030, registering a CAGR of XX% from 2023 to 2030.
The graphical profile grinder DPG-150 was launched by AMADA MACHINERY CO., LTD. The DPG-150 is a ground-breaking device that advances profile grinding through digitalization and makes it simple for anyone to use.
When extremely precise grinding is required, a profile grinder is utilised. When using a profile grinder, the operator's visual judgement is used to execute accuracy, measurement, and corrective processing. The DPG-150 is the first product in its field to have a digital projector.
This makes use of patented proprietary imaging technologies. Additionally, the first all-purpose digital measurement system in the industry and automatic measuring and correction processing functions make it possible for operators with little expertise to execute high-precision processing, which drastically cuts down on training time. Productivity is significantly increased when ATC/AWC robots are installed since they can operate continuously and automatically.
Sl no | Topic |
1 | Market Segmentation |
2 | Scope of the report |
3 | Abbreviations |
4 | Research Methodology |
5 | Executive Summary |
6 | Introduction |
7 | Insights from Industry stakeholders |
8 | Cost breakdown of Product by sub-components and average profit margin |
9 | Disruptive innovation in the Industry |
10 | Technology trends in the Industry |
11 | Consumer trends in the industry |
12 | Recent Production Milestones |
13 | Component Manufacturing in US, EU and China |
14 | COVID-19 impact on overall market |
15 | COVID-19 impact on Production of components |
16 | COVID-19 impact on Point of sale |
17 | Market Segmentation, Dynamics and Forecast by Geography, 2023-2030 |
18 | Market Segmentation, Dynamics and Forecast by Product Type, 2023-2030 |
19 | Market Segmentation, Dynamics and Forecast by Application, 2023-2030 |
20 | Market Segmentation, Dynamics and Forecast by End use, 2023-2030 |
21 | Product installation rate by OEM, 2023 |
22 | Incline/Decline in Average B-2-B selling price in past 5 years |
23 | Competition from substitute products |
24 | Gross margin and average profitability of suppliers |
25 | New product development in past 12 months |
26 | M&A in past 12 months |
27 | Growth strategy of leading players |
28 | Market share of vendors, 2023 |
29 | Company Profiles |
30 | Unmet needs and opportunity for new suppliers |
31 | Conclusion |
32 | Appendix |