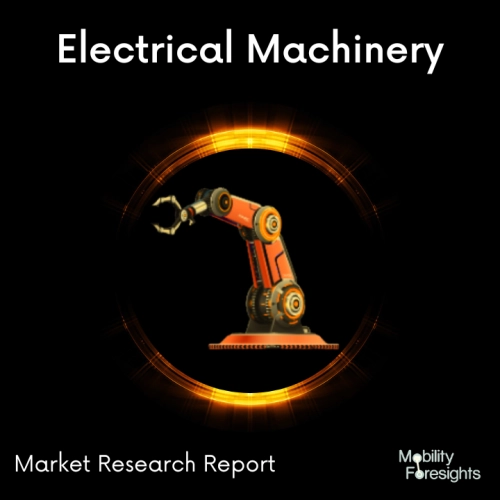
- Get in Touch with Us
Last Updated: Apr 25, 2025 | Study Period: 2024-2030
Graphite is chopped and shaped using specialized equipment called graphite machining centers. A number of industries, including aerospace, automotive, medical, and electronics, use graphite machining centers. They are employed to create components with rigorous requirements and a high need for accuracy.
Cutting tools including end mills, drills, and saws are used in graphite machining centers to shape and cut the material. A spindle with the cutting tools placed on it is then attached to a worktable. The cutting tool can travel along three separate axesâX, Y, and Zâby adjusting the worktable. The graphite is then sliced using the cutting tool into the required shape.
The graphite machining centers have several qualities that make them appropriate for the task. A high-speed spindle, a high-torque motor, sophisticated cooling systems, and a dust collection system are some of these features.
The high-torque motor enables the spindle to run at high speeds, while the high-speed spindle ensures that the tool can cut swiftly and accurately. The temperature of the tool is kept stable by the sophisticated cooling systems, and the workspace is kept tidy by the dust collection system.
The user-friendly design of the graphite machining centers makes setup and use simple. The machine will automatically adjust to generate the desired form after the user selects the cutting settings they require. This guarantees that the product is swiftly and precisely sliced.
For sectors that require precise and accurate components, graphite machining centers are crucial. They are necessary for each contemporary production plant and provide a practical means of creating high-quality components.
The Global Graphite machining center market accounted for $XX Billion in 2023 and is anticipated to reach $XX Billion by 2030, registering a CAGR of XX% from 2024 to 2030.
XYZ Manufacturing Co.'s Graphite Machining Center is a high-precision milling machine designed specifically for machining graphite components. It has a large work area and is completely enclosed to provide a dust-free environment.
To ensure precise cutting of even the most intricate graphite shapes, the machine is outfitted with a powerful spindle motor and high-torque servo motors. The Graphite Machining Center also has an easy-to-use control system, making it simple to programme and operate.
The Graphite Machining Center, with its advanced capabilities, is ideal for producing a wide range of graphite components for industrial and commercial applications.
Hurco's 5-Axis M Series Graphite Machining Center is specifically designed for efficiently machining graphite for electrode manufacturing. This machine has a rigid mechanical design, a faster spindle speed, and a trunnion-style table for maximum accuracy and repeatability.
The machine has high-speed rapids and a maximum axis travel of 25.6" x 15.7" x 19.7", allowing it to machine larger electrodes. It also has a 24-tool ATC, four-sided work area access, and an easy-to-use conversational programming system.
The machine is outfitted with a comprehensive set of sensors and probes to ensure that all machining operations are completed precisely. The Hurco 5-Axis M Series Graphite Machining Center is distinguished by its distinct design and features.
Sl no | Topic |
1 | Market Segmentation |
2 | Scope of the report |
3 | Abbreviations |
4 | Research Methodology |
5 | Executive Summary |
6 | Introduction |
7 | Insights from Industry stakeholders |
8 | Cost breakdown of Product by sub-components and average profit margin |
9 | Disruptive innovation in the Industry |
10 | Technology trends in the Industry |
11 | Consumer trends in the industry |
12 | Recent Production Milestones |
13 | Component Manufacturing in US, EU and China |
14 | COVID-19 impact on overall market |
15 | COVID-19 impact on Production of components |
16 | COVID-19 impact on Point of sale |
17 | Market Segmentation, Dynamics and Forecast by Geography, 2024-2030 |
18 | Market Segmentation, Dynamics and Forecast by Product Type, 2024-2030 |
19 | Market Segmentation, Dynamics and Forecast by Application, 2024-2030 |
20 | Market Segmentation, Dynamics and Forecast by End use, 2024-2030 |
21 | Product installation rate by OEM, 2023 |
22 | Incline/Decline in Average B-2-B selling price in past 5 years |
23 | Competition from substitute products |
24 | Gross margin and average profitability of suppliers |
25 | New product development in past 12 months |
26 | M&A in past 12 months |
27 | Growth strategy of leading players |
28 | Market share of vendors, 2023 |
29 | Company Profiles |
30 | Unmet needs and opportunity for new suppliers |
31 | Conclusion |
32 | Appendix |