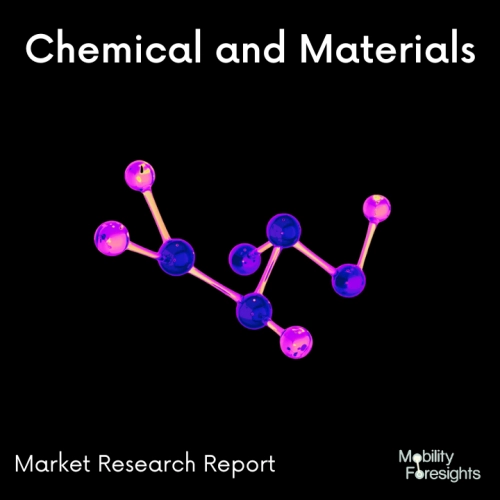
- Get in Touch with Us
Last Updated: Apr 25, 2025 | Study Period: 2024-2030
Grey iron, often known as gray cast iron, is a cast iron with a graphitic microstructure. It gets its name from the gray color of the crack it generates due to the presence of graphite. Based on weight, it is the most common cast iron and the most extensively used cast material.
It is utilized in housings where stiffness is more critical than tensile strength, such as cylinder blocks in internal combustion engines, pump housings, valve bodies, electrical boxes, and ornamental castings.
Grey cast iron is frequently used to create cast iron cookware and disc brake rotors due to its strong thermal conductivity and specific heat capacity. Grey iron is a popular engineering alloy due to its low cost.
Good machinability is due to the graphite lubricating the cut and breaking up the pieces. It also has high galling and wear resistance since the graphite flakes self-lubricate. Grey iron has a great dampening capability because graphite absorbs energy and turns it to heat. Grey iron cannot be worked (forged, extruded, rolled, etc.) even at high temperatures.
Grey iron also has less solidification shrinkage than other cast irons that do not produce a graphite microstructure. When casting, silicon enhances corrosion resistance and enhanced fluidity.
Grey iron is often thought to be simple to weld. Grey iron has limited tensile strength and flexibility when compared to more recent iron alloys, making impact and shock resistance essentially non-existent.
Grey cast iron (also known as gray iron castings) is a form of iron found in castings that is distinguished by its gray color and appearance due to graphite cracks in the substance. The graphite flake structure formed during the cooling process from the carbon in the component is what makes gray iron gray iron.
Grey iron is the product of both the materials used and the casting technique. In other words, the characteristics of gray iron will vary based on the elements fused together to pour into the mold and the casting procedure utilized.
Grey cast iron components (gray iron castings) are popular because they are one of the least expensive forms of iron castings to create. For most applications, it possesses enough ductility, tensile strength, yield strength, and impact resistance.
Grey iron is also great at dampening vibrations, making it perfect for equipment bases and a variety of housing applications. Grey iron has a high thermal conductivity, which means that heat travels more easily through the metal.
Another advantage of gray iron castings is its ability to tolerate heat cycling. Thermal cycling occurs when a component alternates between warmer and cooler temperatures. While heat cycling can cause stress and early failure in some metal castings, gray iron is not one of them.
TheGlobal Gray Cast Iron Market accounted for $XX Billion in 2023 and is anticipated to reach $XX Billion by 2030, registering a CAGR of XX% from 2024 to 2030.
Metalworking Solutions Company MITSUBISHI MATERIALS CORPORATION has introduced a variety of MC5100 coated carbide grades for cast iron turning. This series will be available for purchase. The MC5100 series is a collection of CVD coated carbide grades that may be used for a variety of machining applications.
There is a high wear resistance grade that is suited for high speed machining of gray cast iron, as well as an outstanding fracture resistance grade that is ideal for heavy interrupted machining of ductile cast iron.
The MC5115 grade, on the other hand, inhibits aberrant cutting edge damage during ductile cast iron turning while also achieving good wear and fracture resistance. Last but not least, MC5125 shows outstanding fracture resistance under severe interrupted cutting of high-strength ductile cast iron.
All three classes employ Super nano-texture technology to obtain the greatest level of crystal orientation control of the Al2O3 coating layer in the industry. With a top layer of the thickest coating paired with a high hardness carbide base material, MC5105 demonstrates remarkable wear resistance.
MC5115 offers great durability because to the Al2O3 layer, which has good abrasion resistance and a new adhesive layer with better peel resistance. Because of the microstructure of the intermediate layer, MC5125 has great stability and is ideal for ductile cast iron. This grade also has a TICN layer, which is suitable for coping with heavy interrupted cutting.
Sl no | Topic |
1 | Market Segmentation |
2 | Scope of the report |
3 | Abbreviations |
4 | Research Methodology |
5 | Executive Summary |
6 | Introduction |
7 | Insights from Industry stakeholders |
8 | Cost breakdown of Product by sub-components and average profit margin |
9 | Disruptive innovation in the Industry |
10 | Technology trends in the Industry |
11 | Consumer trends in the industry |
12 | Recent Production Milestones |
13 | Component Manufacturing in US, EU and China |
14 | COVID-19 impact on overall market |
15 | COVID-19 impact on Production of components |
16 | COVID-19 impact on Point of sale |
17 | Market Segmentation, Dynamics and Forecast by Geography, 2024-2030 |
18 | Market Segmentation, Dynamics and Forecast by Product Type, 2024-2030 |
19 | Market Segmentation, Dynamics and Forecast by Application, 2024-2030 |
20 | Market Segmentation, Dynamics and Forecast by End use, 2024-2030 |
21 | Product installation rate by OEM, 2023 |
22 | Incline/Decline in Average B-2-B selling price in past 5 years |
23 | Competition from substitute products |
24 | Gross margin and average profitability of suppliers |
25 | New product development in past 12 months |
26 | M&A in past 12 months |
27 | Growth strategy of leading players |
28 | Market share of vendors, 2023 |
29 | Company Profiles |
30 | Unmet needs and opportunity for new suppliers |
31 | Conclusion |
32 | Appendix |