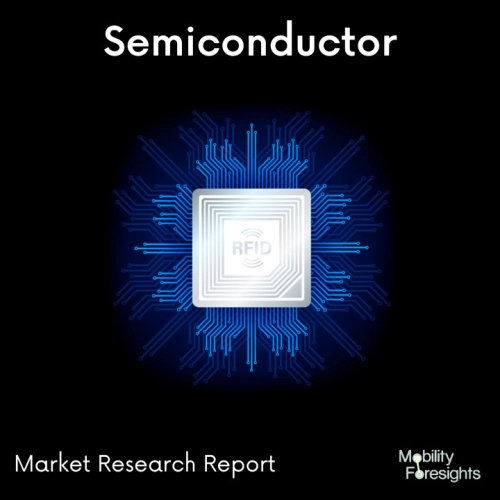
- Get in Touch with Us
Last Updated: Apr 25, 2025 | Study Period: 2023-2030
A method that is comparatively underutilized but allows for the creation of three-dimensional (3-D) microstructures in photosensitive polymers is grayscale lithography. (photoresists).
During the writing process, one can alter the depth at which photoresist develops by spatially manipulating the UV dosage. As a result, intricate shapes and structures that were previously too expensive or labor-intensive to make can now be easily created.
However, the time-consuming production of mask files needed to produce complicated surface topography poses the biggest obstacle to the widespread use of grayscale.
We outline a procedure and related software tool for automatically creating grayscale mask files from 3-D models built using widely used CAD software. By transferring the responsibility for designing microelectromechanical systems (MEMS) to widely used CAD tools appropriate for complicated surfaces.
The Global Grayscale lithography system Market accounted for $XX Billion in 2022 and is anticipated to reach $XX Billion by 2030, registering a CAGR of XX% from 2023 to 2030.
A 2 W optical power light source is used by the HighFive C high-dynamic grayscale lithography system, which was developed recently. It uses UV LEDs of various wavelengths. In order to create the necessary projected pattern, sophisticated optics modify the LED's illumination profile to fit the succeeding micro-display's rectangular shape.
Due to the underlying working theory, each pixel can modify the UV polarization angle with a 10-bit resolution, defining a portion of the light levels that can be used to create the projected image.
The final picture is projected onto the substrate using an interchangeable objective after the required polarization state has been extracted with a beamsplitter. Users have the option of customizing the processing time and resolution tradeoffs for their application by selecting from 1.25x down to 100x demagnification.
The resist-coated substrate is placed on a high-speed motion positioning system with a travel range of 500 Ã 500 mm2. Numerous feedback systems such as linear encoders, an optical autofocus, laser interferometers, and a temperature control unit allow for a repeatability better than 100 nm.
The accurate orientation of lithographic patterning with respect to a previous generated structure level is assisted by an additional alignment microscope. Figure 3 shows a schematic of the grayscale lithography setup.
Sl no | Topic |
1 | Market Segmentation |
2 | Scope of the report |
3 | Abbreviations |
4 | Research Methodology |
5 | Executive Summary |
6 | Introduction |
7 | Insights from Industry stakeholders |
8 | Cost breakdown of Product by sub-components and average profit margin |
9 | Disruptive innovation in the Industry |
10 | Technology trends in the Industry |
11 | Consumer trends in the industry |
12 | Recent Production Milestones |
13 | Component Manufacturing in US, EU and China |
14 | COVID-19 impact on overall market |
15 | COVID-19 impact on Production of components |
16 | COVID-19 impact on Point of sale |
17 | Market Segmentation, Dynamics and Forecast by Geography, 2023-2030 |
18 | Market Segmentation, Dynamics and Forecast by Product Type, 2023-2030 |
19 | Market Segmentation, Dynamics and Forecast by Application, 2023-2030 |
20 | Market Segmentation, Dynamics and Forecast by End use, 2023-2030 |
21 | Product installation rate by OEM, 2023 |
22 | Incline/Decline in Average B-2-B selling price in past 5 years |
23 | Competition from substitute products |
24 | Gross margin and average profitability of suppliers |
25 | New product development in past 12 months |
26 | M&A in past 12 months |
27 | Growth strategy of leading players |
28 | Market share of vendors, 2023 |
29 | Company Profiles |
30 | Unmet needs and opportunity for new suppliers |
31 | Conclusion |
32 | Appendix |