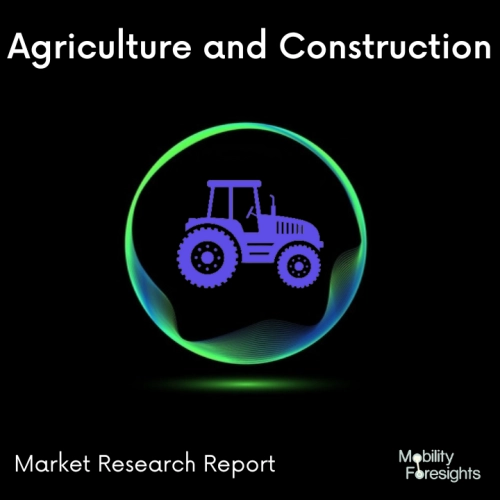
- Get in Touch with Us
Last Updated: Apr 25, 2025 | Study Period: 2023-2030
In contrast to conventional Portland cement, green cement is made with a smaller carbon footprint and strives to have less of an impact on the environment. It is also referred to as sustainable cement or environmentally-friendly cement. This ground-breaking method of making cement addresses the serious environmental issues connected to the building sector, which is one of the biggest producers of carbon emissions worldwide.
The main ingredients of Portland cement, the type of traditional cement, are limestone, clay, and other minerals. These raw materials are heated to high temperatures throughout the manufacturing process, which contributes significantly to atmospheric carbon dioxide (CO2) emissions. An estimated 8% of the world's CO2 emissions are brought on by the manufacture of cement.
The goal of green cement, on the other hand, is to lessen these negative environmental effects. Reducing the amount of clinker used to make cement is one typical strategy. Clinker, a crucial component of Portland cement, must be processed at high temperatures and contributes significantly to CO2 emissions.
Green cement can minimize its clinker content and carbon footprint by using alternative ingredients and cutting-edge manufacturing processes.Adding waste goods and industrial byproducts to the cement mixture is another method for making green cement. Fly ash, slag, silica fume, and rice husk ash are some examples of these substances, also referred to as supplemental cementitious materials (SCMs).
Manufacturers can lower their consumption of raw materials and the amount of energy needed for production by using SCMs, which lowers CO2 emissions.Additionally, green cement frequently emphasizes the utilization of renewable energy sources and alternative fuels during the manufacturing process. Fossil fuels are largely used in conventional cement manufacture, which increases greenhouse gas emissions.
However, producers can greatly lessen the environmental effect associated with cement production by switching to cleaner energy sources like biomass, solar, wind, or even fuels sourced from trash. Green cement is being developed in response to the pressing need to stop climate change and meet environmental objectives.
The green cement accounted for $XX Billion in 2022 and is anticipated to reach $XX Billion by 2030, registering a CAGR of XX% from 2023 to 2030.
One of the top manufacturers of construction materials in the world, LafargeHolcim, has made tremendous progress in creating and promoting green cement alternatives. LafargeHolcim has created a variety of cutting-edge and ecologically responsible cement products as part of its commitment to sustainability and minimizing the carbon footprint of the building industry.
ECOPact is one of LafargeHolcim's premier green cement brands. ECOPact is a group of low-carbon concrete products that achieve high performance standards while drastically reducing carbon emissions.
By utilizing cutting-edge components and manufacturing processes, this line of products attempts to address the issue of cement production that is highly carbon-intensive. From ECOPact Zero, a carbon-neutral concrete, to ECOPact Max, which achieves the highest level of carbon reduction, ECOPact offers a variety of alternatives.
ECOPact by LafargeHolcim is intended to have a less carbon footprint than conventional cement and concrete solutions. It accomplishes this by implementing a number of measures, including the use of alternative raw materials, improving the energy efficiency of production processes, and lowering the content of clinker.
A major amount of cement production's carbon emissions are caused by clinker, a crucial ingredient. ECOPact reduces CO2 emissions significantly by lowering the clinker content and using substitute materials, like supplementary cementitious materials, or SCMs.ECOPact also makes use of LafargeHolcim's extensive global network of R&D facilities to continuously innovate and raise the sustainability of their cement products.
The business explores novel materials and procedures by working with industry partners and investing in cutting-edge technologies. LafargeHolcim is able to maintain its leadership position in the production of sustainable cement thanks to its dedication to research and development.
LafargeHolcim has also unveiled other green cement alternatives in addition to ECOPact. For instance, the business sells Durabric, a masonry product manufactured from recycled aggregates, sand, and cement. In comparison to conventional bricks, durabric uses fewer resources and produces less CO2 during production.
Additionally, Solidia Cement was created by LafargeHolcim and Solidia Technologies. In comparison to conventional cement production, Solidia Cement uses a low-lime formulation and unique curing technique to cut CO2 emissions by up to 70%. Despite having a substantially lower environmental impact than ordinary cement, Solidia Cement offers equivalent performance qualities.
Susteno is another significant LafargeHolcim green cement product. Susteno is a line of blended cements that lowers the clinker content by adding extra cementitious components such fly ash, slag, and limestone. Susteno minimizes carbon emissions while retaining excellent performance by making the best use of these substitute materials.
One of the top global manufacturers of construction materials, CEMEX, has made tremendous progress in developing green cement products that address the environmental issues connected to the production of regular cement. With a focus on sustainability, CEMEX has created cutting-edge products that increase energy efficiency, lower carbon emissions, and use alternative materials.
Vertua, one of CEMEX's premier environmentally friendly cement products, is a significant step toward producing concrete with a net-zero carbon footprint. To lessen concrete's carbon footprint, Vertua uses low-carbon cement and cutting-edge manufacturing techniques.
It contains cutting-edge carbon capture technology developed by CEMEX, which assures that CO2 emissions produced during the cement manufacturing process are permanently stored. With the aid of this technology, Vertua greatly reduces the embodied carbon of concrete, making it a greener and more sustainable material for building projects.
Sl no | Topic |
1 | Market Segmentation |
2 | Scope of the report |
3 | Abbreviations |
4 | Research Methodology |
5 | Executive Summary |
6 | Introduction |
7 | Insights from Industry stakeholders |
8 | Cost breakdown of Product by sub-components and average profit margin |
9 | Disruptive innovation in the Industry |
10 | Technology trends in the Industry |
11 | Consumer trends in the industry |
12 | Recent Production Milestones |
13 | Component Manufacturing in US, EU and China |
14 | COVID-19 impact on overall market |
15 | COVID-19 impact on Production of components |
16 | COVID-19 impact on Point of sale |
17 | Market Segmentation, Dynamics and Forecast by Geography, 2023-2030 |
18 | Market Segmentation, Dynamics and Forecast by Product Type, 2023-2030 |
19 | Market Segmentation, Dynamics and Forecast by Application, 2023-2030 |
20 | Market Segmentation, Dynamics and Forecast by End use, 2023-2030 |
21 | Product installation rate by OEM, 2023 |
22 | Incline/Decline in Average B-2-B selling price in past 5 years |
23 | Competition from substitute products |
24 | Gross margin and average profitability of suppliers |
25 | New product development in past 12 months |
26 | M&A in past 12 months |
27 | Growth strategy of leading players |
28 | Market share of vendors, 2023 |
29 | Company Profiles |
30 | Unmet needs and opportunity for new suppliers |
31 | Conclusion |
32 | Appendix |