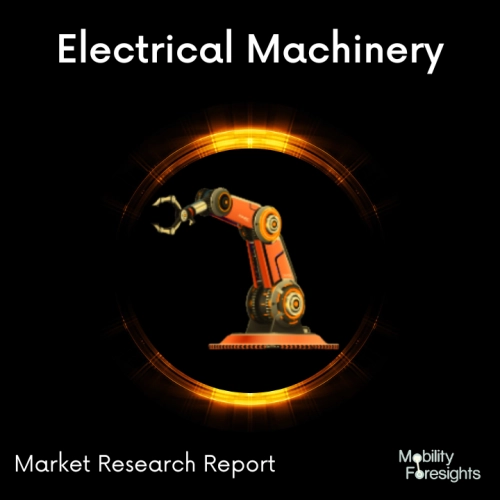
- Get in Touch with Us
Last Updated: Apr 25, 2025 | Study Period: 2023-2030
Grinding machinery is a vital industrial tool used to shape and refine various materials through the process of abrasion.
This essential equipment plays a critical role in manufacturing processes across a wide range of industries, such as metalworking, woodworking, automotive, aerospace, and construction.
By removing excess material from workpieces and achieving precise dimensions and surface finishes, grinding machinery significantly contributes to the production of high-quality components and products.
At its core, grinding is a material removal process that involves the use of an abrasive wheel or belt to wear away material from a workpiece's surface.
The abrasive grains on the grinding wheel or belt act as cutting tools, removing small chips of material as the wheel or belt rotates against the workpiece.
This repetitive action allows for the accurate shaping and finishing of materials, making it an indispensable process in modern manufacturing.
Grinding machinery comes in various forms, each designed to cater to specific industrial applications and material types.
Some of the most commonly used grinding machines include surface grinders, cylindrical grinders, centerless grinders, and tool and cutter grinders.
Surface grinders are primarily used to produce flat surfaces on workpieces.
The workpiece is mounted on a table that moves back and forth under the grinding wheel.
As the wheel grinds against the workpiece's surface, it removes material, creating a smooth and even finish.
Cylindrical grinders, on the other hand, are employed to produce cylindrical or tapered surfaces.
These machines have a rotating wheel or belt that traverses the length of the workpiece, grinding it to the desired shape and dimension.
Centerless grinders are unique in that they do not require a centering mechanism to hold the workpiece in place.
Instead, the workpiece is supported by a work rest blade and a regulating wheel pushes it against the grinding wheel.
This configuration allows for high-precision grinding of cylindrical components without the need for center holes.
Tool and cutter grinders are utilized for sharpening and reconditioning cutting tools used in machining processes.
These machines are equipped with various attachments and fixtures to accommodate different types of cutting tools, such as end mills, drills, and reamers.
The success of grinding machinery lies in the selection of the right abrasive material, wheel or belt type, and the appropriate grinding parameters.
Different abrasives, such as aluminum oxide, silicon carbide, and cubic boron nitride (CBN), are chosen based on the workpiece material and the desired finish.
Additionally, the grit size of the abrasive determines the surface roughness achievable during the grinding process.
Modern grinding machinery often incorporates computer numerical control (CNC) technology, which enables automated and highly precise grinding operations.
CNC-controlled grinding machines can follow complex tool paths and adjust grinding parameters in real-time, resulting in improved productivity and consistency in the manufacturing process.
In high-precision grinding applications, advanced monitoring systems and sensors are integrated into the machinery.
These systems continuously monitor critical parameters, such as grinding forces, temperature, and vibration, to ensure optimal process stability and prevent damage to the workpiece or the machine.
One of the essential aspects of grinding machinery is the coolant or lubrication system. Grinding generates a significant amount of heat, which can cause thermal damage to the workpiece or prematurely wear down the abrasive wheel.
Coolant or lubrication fluids are introduced during the grinding process to dissipate heat, wash away chips, and reduce friction between the wheel and the workpiece, leading to improved surface quality and extended tool life.
Safety is of utmost importance when operating grinding machinery.
Proper training and adherence to safety protocols are crucial to prevent accidents and ensure the well-being of machine operators.
Safety features, such as interlocks, emergency stop buttons, and protective enclosures, are often incorporated into grinding machines to minimize risks and hazards.
In conclusion, grinding machinery is an indispensable tool in modern manufacturing processes, providing precision shaping and finishing of materials across diverse industries.
With its ability to remove excess material and achieve precise dimensions and surface finishes, grinding machinery plays a critical role in the production of high-quality components and products.
Various types of grinding machines, including surface grinders, cylindrical grinders, centerless grinders, and tool and cutter grinders, cater to specific applications and material types.
Incorporation of CNC technology and advanced monitoring systems has further enhanced the productivity and precision of grinding machinery.
The proper selection of abrasive materials, wheel types, and grinding parameters, along with efficient coolant or lubrication systems, ensures optimal performance and extends the lifespan of grinding machinery.
As industries continue to demand higher levels of precision and quality, grinding machinery will remain a fundamental element in the manufacturing landscape.
The Global Grinding Machinery Market accounted for $XX Billion in 2022 and is anticipated to reach $XX Billion by 2030, registering a CAGR of XX% from 2023 to 2030.
Hermle recently launched the C400-5X Ultrasonic Cylindrical Grinder, which is a high-precision machine that uses ultrasonic vibrations to remove material from cylindrical workpieces.
This results in a smoother, more accurate surface finish, and can also help to reduce the risk of chatter.
The C400-5X also features a number of other advanced features, such as a high-speed spindle, a closed-loop control system, and a dust collection system.
Ultrasonic grinding is a process that uses ultrasonic vibrations to remove material from a workpiece.
The vibrations are created by a transducer, which is a piezoelectric device that converts electrical energy into mechanical energy.
The transducer is attached to the grinding wheel, which is then brought into contact with the workpiece.
As the wheel rotates, the vibrations cause the material to be removed from the workpiece in a very controlled manner.
Ultrasonic grinding is a very precise process, and it can be used to achieve very high surface finishes.
It is also a very efficient process, and it can be used to remove material quickly and easily.
Grob recently launched the G550 5-Axis CNC Grinding Machine, which is a high-performance machine that can be used for a wide variety of applications.
The G550 features a 5-axis CNC control system, which allows it to perform complex grinding operations with ease.
The machine also features a high-speed spindle, a large work envelope, and a variety of other advanced features.
A 5-axis CNC grinding machine is a machine that can control the movement of the workpiece in five axes.
This allows the machine to perform complex grinding operations that would not be possible with a 3-axis machine.
The five axes of movement are typically the X, Y, and Z axes, as well as two rotary axes.
5-axis CNC grinding machines are used for a wide variety of applications, including the grinding of complex parts for the aerospace, automotive, and medical industries.
Okuma recently launched the Genos M400-5AX CNC Grinding Machine, which is a high-speed, high-precision machine that is designed for the demanding requirements of the aerospace and medical industries.
The Genos M400-5AX features a 5-axis CNC control system, a high-speed spindle, and a large work envelope.
The machine also features a number of other advanced features, such as a closed-loop control system and a dust collection system.
A CNC grinding machine is a machine that uses a computer numerical control (CNC) system to control the movement of the workpiece and the grinding wheel. This allows the machine to perform complex grinding operations with great precision.
CNC grinding machines are used for a wide variety of applications, including the grinding of complex parts for the aerospace, automotive, and medical industries.
Sl no | Topic |
1 | Market Segmentation |
2 | Scope of the report |
3 | Abbreviations |
4 | Research Methodology |
5 | Executive Summary |
6 | Introduction |
7 | Insights from Industry stakeholders |
8 | Cost breakdown of Product by sub-components and average profit margin |
9 | Disruptive innovation in the Industry |
10 | Technology trends in the Industry |
11 | Consumer trends in the industry |
12 | Recent Production Milestones |
13 | Component Manufacturing in US, EU and China |
14 | COVID-19 impact on overall market |
15 | COVID-19 impact on Production of components |
16 | COVID-19 impact on Point of sale |
17 | Market Segmentation, Dynamics and Forecast by Geography, 2023-2030 |
18 | Market Segmentation, Dynamics and Forecast by Product Type, 2023-2030 |
19 | Market Segmentation, Dynamics and Forecast by Application, 2023-2030 |
20 | Market Segmentation, Dynamics and Forecast by End use, 2023-2030 |
21 | Product installation rate by OEM, 2023 |
22 | Incline/Decline in Average B-2-B selling price in past 5 years |
23 | Competition from substitute products |
24 | Gross margin and average profitability of suppliers |
25 | New product development in past 12 months |
26 | M&A in past 12 months |
27 | Growth strategy of leading players |
28 | Market share of vendors, 2023 |
29 | Company Profiles |
30 | Unmet needs and opportunity for new suppliers |
31 | Conclusion |
32 | Appendix |