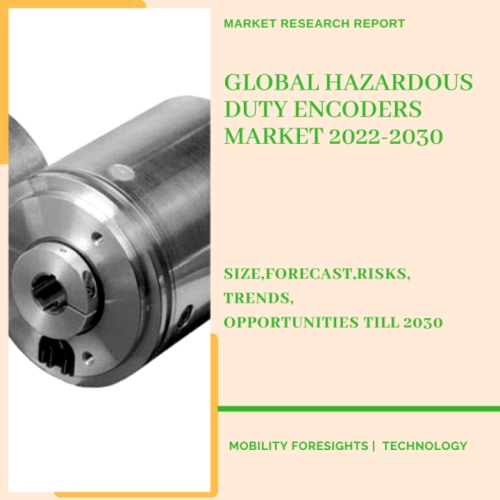
- Get in Touch with Us
Last Updated: Apr 25, 2025 | Study Period: 2022-2030
A wide range of industries and applications, including machine tools, automation, packing, printing, and label/marking equipment, use hazardous and absolute encoders to measure angular position.
They can also be referred to as rotary encoders or shaft encoders. The terms absolute and incremental allude to how the encoders function; the two methods differ from one another.
An electro-mechanical device called an incremental encoder converts the angle of the shaft into digital or pulse signals using an optical disc. Each pulse, which is an increment equivalent to the specified resolution, is produced in a predetermined number of pulses each revolution. Although it cannot measure the absolute position, an incremental encoder can measure the change in position.
The Global hazardous duty encoders market accounted for $XX Billion in 2021 and is anticipated to reach $XX Billion by 2030, registering a CAGR of XX% from 2022 to 2030.
The durable Hazardous Series HSD35 optical encoder is a new addition to Dynapar's line of hazardous encoders. With the addition of this sturdy encoder to the current lineup of hazardous series encoders, which also includes the AX71, EN42, EN44, ISD37, ISD25, ISW38, X25, Hazardous Series HD20, and Hazardous Series HD25, customers will have a wider range of options when choosing an encoder to suit their needs.
The Hazardous Series HSD35 was designed with a few key components to provide more robust feedback in hazardous environments and will be available in a variety of mechanical configurations to custom fit customer application. It has been certified by UL for Class I, Division 2, Groups A, B, C & D; Class II, Division 2, Groups F & G operation.
Sl no | Topic |
1 | Market Segmentation |
2 | Scope of the report |
3 | Abbreviations |
4 | Research Methodology |
5 | Executive Summary |
6 | Introduction |
7 | Insights from Industry stakeholders |
8 | Cost breakdown of Product by sub-components and average profit margin |
9 | Disruptive innovation in the Industry |
10 | Technology trends in the Industry |
11 | Consumer trends in the industry |
12 | Recent Production Milestones |
13 | Component Manufacturing in US, EU and China |
14 | COVID-19 impact on overall market |
15 | COVID-19 impact on Production of components |
16 | COVID-19 impact on Point of sale |
17 | Market Segmentation, Dynamics and Forecast by Geography, 2022-2030 |
18 | Market Segmentation, Dynamics and Forecast by Product Type, 2022-2030 |
19 | Market Segmentation, Dynamics and Forecast by Application, 2022-2030 |
20 | Market Segmentation, Dynamics and Forecast by End use, 2022-2030 |
21 | Product installation rate by OEM, 2022 |
22 | Incline/Decline in Average B-2-B selling price in past 5 years |
23 | Competition from substitute products |
24 | Gross margin and average profitability of suppliers |
25 | New product development in past 12 months |
26 | M&A in past 12 months |
27 | Growth strategy of leading players |
28 | Market share of vendors, 2022 |
29 | Company Profiles |
30 | Unmet needs and opportunity for new suppliers |
31 | Conclusion |
32 | Appendix |