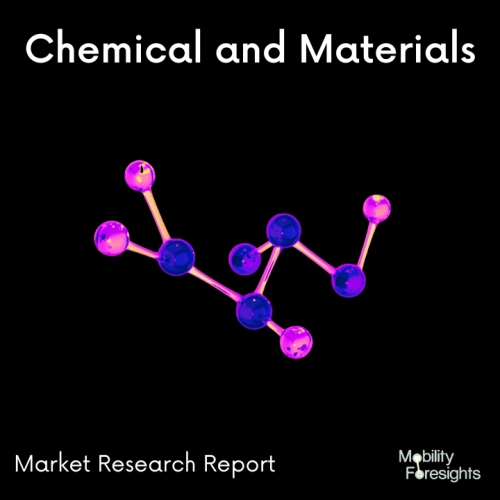
- Get in Touch with Us
Last Updated: Apr 25, 2025 | Study Period: 2024-2030
A type of coating called heat-resistant powder coating is made to withstand high temperatures without deteriorating or losing its qualities.
This kind of powder coating is frequently utilized in industrial, automotive, and aerospace applications where parts are subjected to high temperatures.
Special resins and heat-resistant pigments are used in the formulation of heat-resistant powder coatings. Metallic oxides and other inorganic substances that can provide the necessary heat resistance are frequently used as pigments in these coatings.
The thermosetting polymers epoxy, polyester, and polyurethane are frequently employed in heat-resistant powder coatings.
Heat-resistant powder coatings typically have a temperature resistance range of 250 to 600 degrees Celsius (482 to 1112 degrees Fahrenheit), though this might vary based on the exact composition.
Even temperatures beyond 1000 degrees Celsius (1832 degrees Fahrenheit) can be tolerated by some specialized formulations.
Electrostatic sprayers, fluidized bed applications, as well as other application techniques, can be used to apply heat-resistant powder coatings.
According to the manufacturer's specifications, the coating is normally cured in an oven at a certain temperature for a specific amount of time.
Overall, heat-resistant powder coatings offer improved corrosion and wear resistance, as well as aesthetic appeal, making them an efficient solution to shield components from high-temperature conditions.
The Global Heat-resistant Powder Coating Machine Market accounted for $XX Billion in 2023 and is anticipated to reach $XX Billion by 2030, registering a CAGR of XX% from 2024 to 2030.
D-Zolve 917, a product created by Peabody, Massachusetts-based Solvent Kleene Inc., is intended to remove powder coating that is resistant to high temperatures and chemicals.
In applications where it is critical that the coating survive extreme temperatures without discoloring, losing gloss, adhesion, or breaking, extreme heat, and chemical-resistant powder coating is employed.
Removing chemical-resistant high-temperature powder coating can be difficult since it is more durable than ceramic coating and has been tested at temperatures as high as 1200°F/ 649°C.
The powder coating from the substrate's surface is removed by D-Zolve 917. The solution operates at a low temperature of 110°F, is non-flammable, and doesn't contain peroxides or methylene chloride.
Immersion and agitation are used to remove the hot powder coating, which is then quickly rinsed off with water.
Sl no | Topic |
1 | Market Segmentation |
2 | Scope of the report |
3 | Abbreviations |
4 | Research Methodology |
5 | Executive Summary |
6 | Introduction |
7 | Insights from Industry stakeholders |
8 | Cost breakdown of Product by sub-components and average profit margin |
9 | Disruptive innovation in the Industry |
10 | Technology trends in the Industry |
11 | Consumer trends in the industry |
12 | Recent Production Milestones |
13 | Component Manufacturing in US, EU and China |
14 | COVID-19 impact on overall market |
15 | COVID-19 impact on Production of components |
16 | COVID-19 impact on Point of sale |
17 | Market Segmentation, Dynamics and Forecast by Geography, 2024-2030 |
18 | Market Segmentation, Dynamics and Forecast by Product Type, 2024-2030 |
19 | Market Segmentation, Dynamics and Forecast by Application, 2024-2030 |
20 | Market Segmentation, Dynamics and Forecast by End use, 2024-2030 |
21 | Product installation rate by OEM, 2023 |
22 | Incline/Decline in Average B-2-B selling price in past 5 years |
23 | Competition from substitute products |
24 | Gross margin and average profitability of suppliers |
25 | New product development in past 12 months |
26 | M&A in past 12 months |
27 | Growth strategy of leading players |
28 | Market share of vendors, 2023 |
29 | Company Profiles |
30 | Unmet needs and opportunity for new suppliers |
31 | Conclusion |
32 | Appendix |