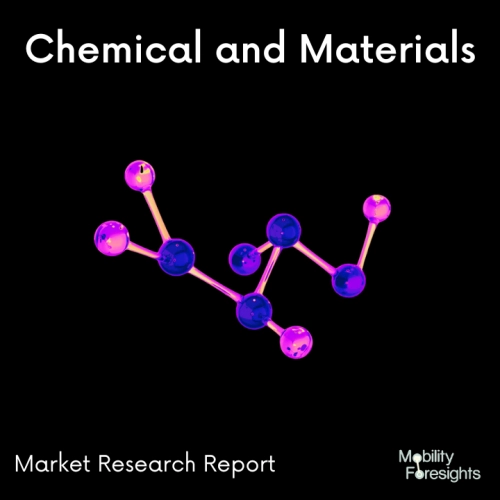
- Get in Touch with Us
Last Updated: Apr 25, 2025 | Study Period: 2024-2030
Heat transfer powder coating, sometimes referred to as sublimation powder coating or heat transfer printing, is an advanced coating technique used to transfer decorative patterns, designs, or images onto a variety of substrates. It entails applying pressure and heat to a coated surface in order to transfer a printed design from a heat-sensitive paper or film.
The following steps are commonly involved in the heat transfer powder coating process:
preparing the coating: Cleaning and coating preparation is done on the substrate, which could be made of metal, plastic, or another substance. In order to provide a homogeneous and smooth surface for the transfer process, a base coat powder is applied to the substrate.
The intended pattern or picture is printed using specialized sublimation inks onto a heat-sensitive film or piece of paper. These inks have the ability to sublimate, which allows them to go from a solid to a gas state when heated without going through the liquid phase.
Transfer procedure: The coated substrate is carefully placed on top of the printed film while the pattern is carefully aligned as necessary. The substrate and film are then put under pressure and heat using a heat press or other appropriate machinery.
The pressure aids in ensuring adequate adherence while the heat forces the sublimation inks on the film to vaporize and permeate the powder coating.
After the transfer procedure, the coated substrate is allowed to cool before completing. The transferred pattern is then left on the surface once the heat-sensitive coating has been removed. The transferred pattern can be covered with a clear topcoat powder to offer extra protection and durability.
The following are some benefits of heat transfer powder coating:
Heat transfer powder coating enables the application of complex and minute patterns, designs, or images onto a variety of substrates. It provides numerous options for customizing and customization.
Durability: By becoming a permanent part of the powder coating, the transferred design ensures strong adherence and resistance to flaking, peeling, and scratching. The end product's protection and durability are further improved by the clear topcoat.
Full-color printing: Heat transfer powder coating allows for the accurate and consistent reproduction of brilliant, full-color designs. Fine features and gradients that might be difficult to capture using conventional coating techniques can be captured.
Versatility in application: Metals, polymers, ceramics, and glass are just a few of the substrates that heat transfer powder coating can be used on. It is used in a variety of sectors, including those related to automotive, signage, consumer goods, promotional products, and more.
Heat transfer powder coating is distinct from conventional powder coating in that it includes applying the dry powder directly to a substrate and curing it with heat. The application of printed graphics to coated surfaces through the use of heat transfer powder coating is a specialized procedure.
The Global Heat Transfer Powder Coating Market accounted for $XX Billion in 2023 and is anticipated to reach $XX Billion by 2030, registering a CAGR of XX% from 2024 to 2030.
For applications involving heat-sensitive wood and wood composites, such as medium-density fiberboard (MDF), hardwood, plywood, and related goods, PPG (NYSE: PPG) has introduced PPG ENVIROCRONTM HeatSense powder coating.
PPG Envirocron HeatSense coating is designed to solve the challenges that have previously precluded powder coatings from being a viable alternative for the wood-finish market.
It was developed to complement the most recent developments in low-temperature cure technology. The coating can apply uniformly over heat-sensitive substrates, cure in as little as five minutes at 250 degrees Fahrenheit, and allow for the expansion and contraction of wood over the lifetime of the finished product.
Sl no | Topic |
1 | Market Segmentation |
2 | Scope of the report |
3 | Abbreviations |
4 | Research Methodology |
5 | Executive Summary |
6 | Introduction |
7 | Insights from Industry stakeholders |
8 | Cost breakdown of Product by sub-components and average profit margin |
9 | Disruptive innovation in the Industry |
10 | Technology trends in the Industry |
11 | Consumer trends in the industry |
12 | Recent Production Milestones |
13 | Component Manufacturing in US, EU and China |
14 | COVID-19 impact on overall market |
15 | COVID-19 impact on Production of components |
16 | COVID-19 impact on Point of sale |
17 | Market Segmentation, Dynamics and Forecast by Geography, 2024-2030 |
18 | Market Segmentation, Dynamics and Forecast by Product Type, 2024-2030 |
19 | Market Segmentation, Dynamics and Forecast by Application, 2024-2030 |
20 | Market Segmentation, Dynamics and Forecast by End use, 2024-2030 |
21 | Product installation rate by OEM, 2023 |
22 | Incline/Decline in Average B-2-B selling price in past 5 years |
23 | Competition from substitute products |
24 | Gross margin and average profitability of suppliers |
25 | New product development in past 12 months |
26 | M&A in past 12 months |
27 | Growth strategy of leading players |
28 | Market share of vendors, 2023 |
29 | Company Profiles |
30 | Unmet needs and opportunity for new suppliers |
31 | Conclusion |
32 | Appendix |