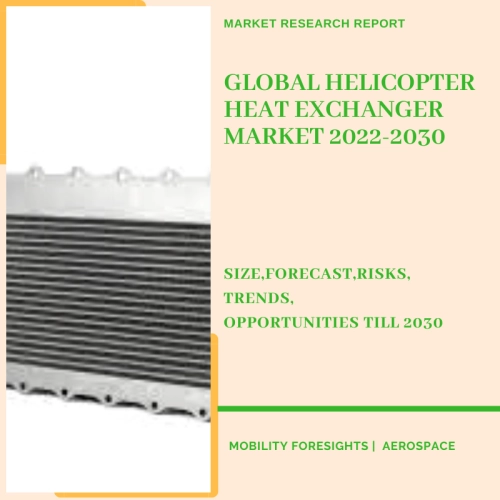
- Get in Touch with Us
Last Updated: Apr 25, 2025 | Study Period: 2022-2030
Helicopter engines, avionics, and environmental control systems all use heat exchangers to assist regulate heat and maintain temperature by removing extra heat from the systems. Heat exchangers, which are housed inside the gasoline tank, are used to cool hydraulic fluid.
In mission-critical aviation and other aerospace applications, heat exchangers are crucial. They are crucial for the proper operation of aviation electronics, for the best performance of jet engines, and for a satellite's ability to serve a variety of functions without overheating.
The global helicopter heat exchanger market accounted for $XX Billion in 2021 and is anticipated to reach $XX Billion by 2030, registering a CAGR of XX% from 2022 to 2030.
In mission-critical aviation and various other aerospace applications, heat exchangers are essential. The demand for heat transfer equipment has been boosted by increased energy demands from the oil and gas, petrochemical, and power industries as well as rising investments in upgrading existing aviation, space, helicopter and energy infrastructure.
For example, heat exchangers are a crucial part for the proper operation of jet engines, crucial for the precise operation of aircraft electronics, and crucial for a satellite's ability to carry out a variety of tasks without overheating.The heat exchanger fouling problems, on the other hand, are likely to impede the profit margins. A further boost for the helicopter heat exchanger will come from the growing fleet of commercial and combat aircraft as well as the rising demand for efficient cooling and heating in commercial aircraft.The aerospace industry is especially well suited for the additive manufacturing's vast potential.
For example, components that are weight-optimized benefit the aircraft's overall mass. Parts that optimize flow improve the efficiency of rocket and aviation engines. Additionally, hydraulic modules can be made to be much more efficient, which has advantages for both the individual component and the entire system. The availability of replacement parts can reduce the amount of time prototypes take to develop and minimize downtime. In this way, additive manufacturing can be very important to OEM manufacturers in the aerospace industry, especially when traditional manufacturing techniques reach their limits due to the complexity of the components or when time becomes a major factor due to the associated expenses.
Sl no | Topic |
1 | Market Segmentation |
2 | Scope of the report |
3 | Abbreviations |
4 | Research Methodology |
5 | Executive Summary |
6 | Introduction |
7 | Insights from Industry stakeholders |
8 | Cost breakdown of Product by sub-components and average profit margin |
9 | Disruptive innovation in the Industry |
10 | Technology trends in the Industry |
11 | Consumer trends in the industry |
12 | Recent Production Milestones |
13 | Component Manufacturing in US, EU and China |
14 | COVID-19 impact on overall market |
15 | COVID-19 impact on Production of components |
16 | COVID-19 impact on Point of sale |
17 | Market Segmentation, Dynamics and Forecast by Geography, 2022-2030 |
18 | Market Segmentation, Dynamics and Forecast by Product Type, 2022-2030 |
19 | Market Segmentation, Dynamics and Forecast by Application, 2022-2030 |
20 | Market Segmentation, Dynamics and Forecast by End use, 2022-2030 |
21 | Product installation rate by OEM, 2022 |
22 | Incline/Decline in Average B-2-B selling price in past 5 years |
23 | Competition from substitute products |
24 | Gross margin and average profitability of suppliers |
25 | New product development in past 12 months |
26 | M&A in past 12 months |
27 | Growth strategy of leading players |
28 | Market share of vendors, 2022 |
29 | Company Profiles |
30 | Unmet needs and opportunity for new suppliers |
31 | Conclusion |
32 | Appendix |