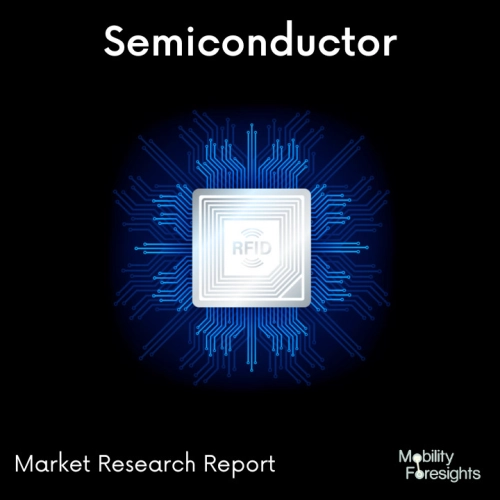
- Get in Touch with Us
Last Updated: Apr 25, 2025 | Study Period: 2023-2030
INTRODUCTION
Vapor phase etching (VPE) is a form of chemical etching that uses vaporized chemicals for etching. This etching process is commonly used for creating patterns on the surfaces of various materials, such as metals and semiconductors. It can also be used to create very small features and structures.
Vapor phase etching is a dry process that requires no liquid, making it faster and more efficient than wet etching processes. This means that it is ideal for high-volume production, as it can be quickly and easily implemented. Vapor phase etching is also very precise and can be used to create intricate patterns and structures on the surface of the material being etched.
The process involves the use of a specialized vapor phase etcher, which is a vacuum chamber that contains various chemicals which are vaporized and then used to etch the material. The vapor phase etcher is filled with a vapor phase etchant, which is a combination of gases and other elements. These materials are heated and then condensed on the surface of the material to be etched.
The vapor phase etching process is highly reliable and can be used to create intricate patterns and structures with high accuracy. It is also an effective way to clean the surface of the material, as it removes any impurities or contaminants that may have been present before the etching process began.
Overall, vapor phase etching is an efficient and effective way to create intricate patterns and structures on the surfaces of various materials. It is also a quick and easy process, making it ideal for high-volume production.
GLOBAL HF VAPOR PHASE ETCHER MARKET SIZE AND FORECAST
The Global HF Vapor Phase Etcher Market accounted for $XX Billion in 2022 and is anticipated to reach $XX Billion by 2030, registering a CAGR of XX% from 2023 to 2030.
The largest selection of dry HF vapour release devices is offered by SPTS, which offers everything from multi-chambered cluster instruments for high volume production to lab systems for research and development.
To release silicon microstructures in MEMS devices, or photonic components, sacrificial silicon oxide layers are removed using the industry-leading Primaxx® HF vapour etch release technology.
Their unique dry technique prevents damage to delicate components and stiction of released moving parts, which are major problems with traditional wet processing technologies.
A wide, stable process window that can handle varying oxide compositions and thicknesses is created by combining anhydrous HF vapour and alcohol vapour at reduced pressure and elevated temperature. This combination maintains high selectivity to other common materials found in MEMS designs, such as exposed aluminium/alloy features like mirrors and bond pads.
The HF Vapour Etcher from AMMT fully operates in the vapour phase to solve the issue. Applications like structure thinning, dicing-free release, SOI-MEMS, surface micromachining, and many more are well suited for the HF Vapour Etcher.Positioning the etching side down, the wafer is placed onto the reaction cell.
An insignificant liquid reservoir at the reaction cell's base passively produces HF vapour. The volatile SiF4 that is produced when the HF vapour combines with the SiO2 on the wafer surface easily desorbs from. Only trace amounts of surface water are necessary for the reaction to occur.
A precise heater plate resistant to HF is used to gently heat the wafer from the back in order to ensure a minuscule water film on the surface without creating droplets that could cause sticking.
Just a few degrees above ambient temperature is sufficient to cause the water coating on the wafer to evaporate. A temperature increase causes the etch rate to drop; at 50°C and above, it entirely stops.
Its unique heater design reduces temperature differences across the wafer, which could interfere with the etch rate and result in a superior etching homogeneity. For thermal oxides, typical lateral etch rates range from 3 to 5 µm/hr; for CVD oxides, the rates can be up to twice as high.
THIS REPORT WILL ANSWER FOLLOWING QUESTIONS
Sl no | Topic |
1 | Market Segmentation |
2 | Scope of the report |
3 | Abbreviations |
4 | Research Methodology |
5 | Executive Summary |
6 | Introduction |
7 | Insights from Industry stakeholders |
8 | Cost breakdown of Product by sub-components and average profit margin |
9 | Disruptive innovation in the Industry |
10 | Technology trends in the Industry |
11 | Consumer trends in the industry |
12 | Recent Production Milestones |
13 | Component Manufacturing in US, EU and China |
14 | COVID-19 impact on overall market |
15 | COVID-19 impact on Production of components |
16 | COVID-19 impact on Point of sale |
17 | Market Segmentation, Dynamics and Forecast by Geography, 2023-2030 |
18 | Market Segmentation, Dynamics and Forecast by Product Type, 2023-2030 |
19 | Market Segmentation, Dynamics and Forecast by Application, 2023-2030 |
20 | Market Segmentation, Dynamics and Forecast by End use, 2023-2030 |
21 | Product installation rate by OEM, 2023 |
22 | Incline/Decline in Average B-2-B selling price in past 5 years |
23 | Competition from substitute products |
24 | Gross margin and average profitability of suppliers |
25 | New product development in past 12 months |
26 | M&A in past 12 months |
27 | Growth strategy of leading players |
28 | Market share of vendors, 2023 |
29 | Company Profiles |
30 | Unmet needs and opportunity for new suppliers |
31 | Conclusion |
32 | Appendix |