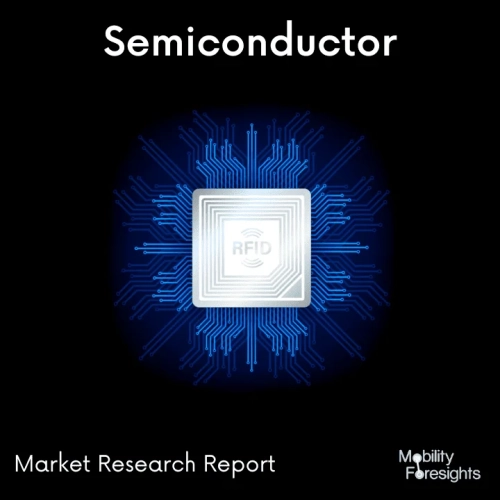
- Get in Touch with Us
Last Updated: Apr 25, 2025 | Study Period:
Since the cathodes have higher specific capacity and lower price, the high nickel layered oxide cathode is regarded as one of the most promising cathode materials for lithium-ion batteries.
However, residual lithium compounds, such as LiOH, Li2CO3, and others, necessarily exist on the surface of the cathode material as a result of the increased Ni concentration.
In addition, due to the high nickel cathode material's inherent instability, practical applications are hampered by structural degradation and severe capacity degradation. Here, we present a straightforward and scalable method that makes use of the hydrolysis and lithiation processes.
The effectiveness of high-Ni cathode materials is currently being improved, and industry leaders worldwide are developing new Ni-based cathode materials. Together, they anticipate a promising future for Ni-based cathodes given all the intriguing research that is now being done.
However, as the nickel concentration rises, the energy density rises along with the quantity of lithium that can be cycled into and out of the cathode.
By switching to nickel-rich cathodes, cobalt is also no longer required. The DR Congo, which provides around 50% of the cobalt ore, has ethical concerns about its mining techniques, which have a negative impact on cobalt output. The sustainability of the element cobalt is in doubt, and its price is therefore incredibly unstable.
The growth of electric vehicles (EVs) makes it essential to produce low-cost, high energy density batteries. High energy density cathodes have drawn a lot of attention since they form the foundation for high energy density lithium-ion batteries, which are necessary to get past the "range anxiety" that is preventing EV adoption worldwide.
In order to achieve the best possible balance between battery cost and performance, scientists and engineers from government laboratories, the academic community, and business have been collaborating to solve technical obstacles and constraints.
WMG Technologies is a leading mobiliser of the equipment in the market. The latest integration has been the technology wherein the dry environment used for cathode processing and storage results in a notable improvement in High-Ni battery performance.
The NMC-811 cathode was initially subjected to a range of temperatures and humidity levels. The material's performance and deterioration in a battery during a 28-day period were measured and examined for each sample. This analysis made use of a combination of physical, chemical, and electrochemical testing.
KAERI is part of the component manufacture trending companies in the current industry. The NMC with 90% nickel and found that a well-known defect, the Li/Ni disorder, actually decreases as the nickel content increases; however, it must be measured after cycling the cathodes because it significantly increases from the initially prepared material.
This was done using an advanced characterization technique called neutron diffraction. Contrary to popular belief, because overcharging removes passivating surface layers like nickel oxides, it is actually helpful for the issue of voltage decay.
Sl no | Topic |
1 | Market Segmentation |
2 | Scope of the report |
3 | Abbreviations |
4 | Research Methodology |
5 | Executive Summary |
6 | Introduction |
7 | Insights from Industry stakeholders |
8 | Cost breakdown of Product by sub-components and average profit margin |
9 | Disruptive innovation in the Industry |
10 | Technology trends in the Industry |
11 | Consumer trends in the industry |
12 | Recent Production Milestones |
13 | Component Manufacturing in US, EU and China |
14 | COVID-19 impact on overall market |
15 | COVID-19 impact on Production of components |
16 | COVID-19 impact on Point of sale |
17 | Market Segmentation, Dynamics and Forecast by Geography, 2022-2030 |
18 | Market Segmentation, Dynamics and Forecast by Product Type, 2022-2030 |
19 | Market Segmentation, Dynamics and Forecast by Application, 2022-2030 |
20 | Market Segmentation, Dynamics and Forecast by End use, 2022-2030 |
21 | Product installation rate by OEM, 2022 |
22 | Incline/Decline in Average B-2-B selling price in past 5 years |
23 | Competition from substitute products |
24 | Gross margin and average profitability of suppliers |
25 | New product development in past 12 months |
26 | M&A in past 12 months |
27 | Growth strategy of leading players |
28 | Market share of vendors, 2022 |
29 | Company Profiles |
30 | Unmet needs and opportunity for new suppliers |
31 | Conclusion |
32 | Appendix |