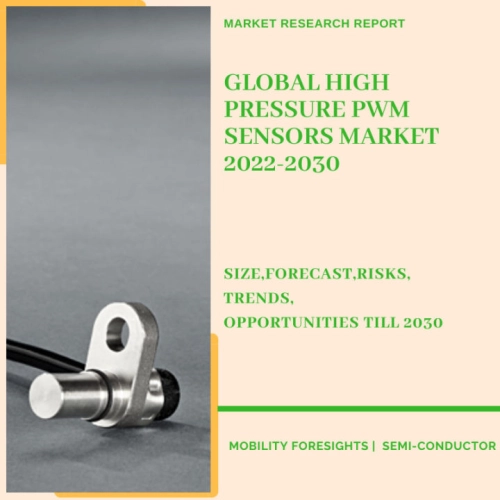
- Get in Touch with Us
Last Updated: Apr 25, 2025 | Study Period: 2022-2030
PWM, which stands for "Pulse Width Modulation," is a communication technique that modifies the pulse wave's altered duty ratio.
Only the breadth of the high level (ON) of the pulse is altered; the voltage magnitude and cycle are left unaffected. It is utilised for the inverter circuit, pump, hydraulic, control valve, and DC motor control.
PWM output sensors have resistance to ground potential change and voltage noise. The microcomputer's timer or counter board can read the PWM signal with ease.
PWM controls the amount of current flowing to a device, such as an LED, by pulsating DC current and altering how long each pulse remains "on." Since PWM is digital, it only has two states: on and off (which correspond to 1 and 0 in the binary context).
TheGlobal High Pressure PWM Sensors marketaccounted for $XX Billion in 2021 and is anticipated to reach $XX Billion by 2030, registering a CAGR of XX% from 2022 to 2030.
Wheel speed sensors with direction detection like the XENSIVTM TLE5046iC from Infineon are made for complex vehicle control systems.
The TLE5046iC is the finest option for wheel speed applications because it exhibits best-in-class jitter performance.
The sensor can be employed as a part of indirect tyre pressure monitoring systems since it can accurately measure rotational speed (iTPMS). Integrated magneto resistance serves as its foundation (iGMR).
Over a large temperature range, excellent sensitivity to magnetic field is described. Robustness to electrostatic discharge (ESD) and electromagnetic compatibility (EMC) were optimised to fulfil stringent automotive requirements without the need of extra external components.
Sl no | Topic |
1 | Market Segmentation |
2 | Scope of the report |
3 | Abbreviations |
4 | Research Methodology |
5 | Executive Summary |
6 | Introduction |
7 | Insights from Industry stakeholders |
8 | Cost breakdown of Product by sub-components and average profit margin |
9 | Disruptive innovation in the Industry |
10 | Technology trends in the Industry |
11 | Consumer trends in the industry |
12 | Recent Production Milestones |
13 | Component Manufacturing in US, EU and China |
14 | COVID-19 impact on overall market |
15 | COVID-19 impact on Production of components |
16 | COVID-19 impact on Point of sale |
17 | Market Segmentation, Dynamics and Forecast by Geography, 2022-2030 |
18 | Market Segmentation, Dynamics and Forecast by Product Type, 2022-2030 |
19 | Market Segmentation, Dynamics and Forecast by Application, 2022-2030 |
20 | Market Segmentation, Dynamics and Forecast by End use, 2022-2030 |
21 | Product installation rate by OEM, 2022 |
22 | Incline/Decline in Average B-2-B selling price in past 5 years |
23 | Competition from substitute products |
24 | Gross margin and average profitability of suppliers |
25 | New product development in past 12 months |
26 | M&A in past 12 months |
27 | Growth strategy of leading players |
28 | Market share of vendors, 2022 |
29 | Company Profiles |
30 | Unmet needs and opportunity for new suppliers |
31 | Conclusion |
32 | Appendix |