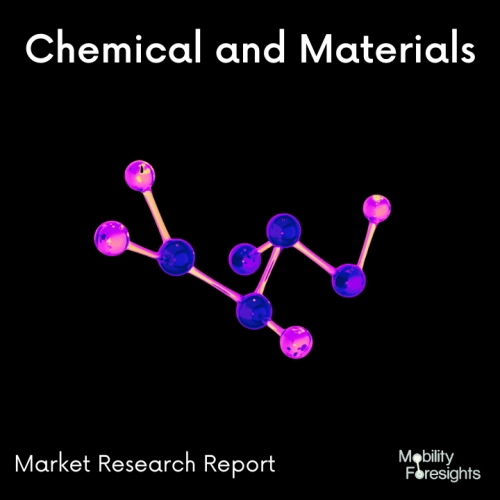
- Get in Touch with Us
Last Updated: Apr 25, 2025 | Study Period: 2024-2030
Ferritic stainless steels have a high Cr content and a low carbon content. They have strong strength and moderate to good corrosion resistance. They are not hardenable. Their weldability ranges from fair to poor. These steels are mostly used in household hardware, sinks, cutlery, and table tops. Ferritic alloys are utilized in the construction of steel buildings, walkways, and steps.
Molybdenum (Mo) has been added to super ferritic steels. This increases resistance to pitting and stress corrosion cracking (SCC). However, because of their low weldability, they are not commonly used to substitute austenitic steels in manufactured goods.
Ferritic stainless steels are Fe-Cr-C alloys containing ferrite stabilizers such as aluminum (Al), columbium (Cb), molybdenum (Mo), and titanium (Ti) to prevent austenite production during heating. As a result, they are not hardenable. Lower-alloy ferritic stainless steels have mechanical qualities that are similar to low-alloy austenitic stainless steels such as type 304 when annealed.
The normal yield strength is in the range. Alloys with greater chromium, molybdenum, and nickel content are stronger.The welding technique in high-chromium-containing alloys, such as UNS S44626, is generally created to minimize interstitial pickup during welding while retaining material toughness. These alloys are mostly used to make thin-walled tubes.
These alloys normally lose toughness as section thickness increases, and a maximum thickness has been defined for each alloy based on the toughness requirements. The interstitial contents of high-chromium alloys have been carefully regulated for this purpose.
First-generation ferritic alloys display low toughness and are prone to intergranular corrosion following welding.
Second-generation ferritic alloys include less chromium and carbon and have strong ferrite and carbide formers to minimize the quantity of carbon in solid solution. Although ferritic in nature, martensite can develop as a result of welding or heat treatment. Ferritic alloys are inexpensive and have good corrosion resistance but low hardness.
Recent advancements in melting techniques have resulted in third-generation ferritic alloys with extremely low melting points.The presence of adequate chromium and other stabilizers to effectively inhibit the production of austenite at increased temperatures is the most essential metallurgical property of the ferritic alloy. Because interstitials are present, most grades form some austenite.
These steels cannot be toughened by quenching because austenite does not develop and ferrite is stable at all temperatures up to melting. The soft ferrite easily accommodates the minor quantities of austenite that may be present.
Heat treatment cannot significantly strengthen ferritic stainless steels. These steels are typically utilized in the annealed state. The cooling rate from the selected annealing temperature is determined by the alloy.
TheGlobal High Temperature Ferritic Stainless Steel Market accounted for $XX Billion in 2023 and is anticipated to reach $XX Billion by 2030, registering a CAGR of XX% from 2024 to 2030.
To meet the changing demands of clients and to provide the highest quality products in the automotive sector, Jindal Stainless research and development team created grade 430J1L niobium stabilized ferritic stainless steel.
This specialized grade has a high concentration of Chromium as well as some copper. This stainless steel is mostly used to manufacture automotive components such as manifolds, catalytic converter shells and EGR (Exhaust gas recirculation). This grade is also utilized in car mufflers, where the condensate from exhaust gas causes severe corrosion.
The formability of 430J1L is excellent for shape forming and drawing of automobile components. Furthermore, in a comparable atmosphere of exhaust fumes, it has outstanding corrosion resistance, oxidation resistance, and high-temperature strength.
1 | Market Segmentation |
2 | Scope of the report |
3 | Abbreviations |
4 | Research Methodology |
5 | Executive Summary |
6 | Introduction |
7 | Insights from Industry stakeholders |
8 | Cost breakdown of Product by sub-components and average profit margin |
9 | Disruptive innovation in the Industry |
10 | Technology trends in the Industry |
11 | Consumer trends in the industry |
12 | Recent Production Milestones |
13 | Component Manufacturing in US, EU and China |
14 | COVID-19 impact on overall market |
15 | COVID-19 impact on Production of components |
16 | COVID-19 impact on Point of sale |
17 | Market Segmentation, Dynamics and Forecast by Geography, 2024-2030 |
18 | Market Segmentation, Dynamics and Forecast by Product Type, 2024-2030 |
19 | Market Segmentation, Dynamics and Forecast by Application, 2024-2030 |
20 | Market Segmentation, Dynamics and Forecast by End use, 2024-2030 |
21 | Product installation rate by OEM, 2023 |
22 | Incline/Decline in Average B-2-B selling price in past 5 years |
23 | Competition from substitute products |
24 | Gross margin and average profitability of suppliers |
25 | New product development in past 12 months |
26 | M&A in past 12 months |
27 | Growth strategy of leading players |
28 | Market share of vendors, 2023 |
29 | Company Profiles |
30 | Unmet needs and opportunity for new suppliers |
31 | Conclusion |
32 | Appendix |